Sand for casting metal is a cornerstone of the foundry industry, playing a pivotal role in the production of complex metal parts. Its usage dates back centuries and remains irreplaceable due to its unique properties. The primary advantage of using sand in metal casting processes includes its adaptability, reusability, and cost efficiency, making it the choice for industries ranging from automotive to aerospace.
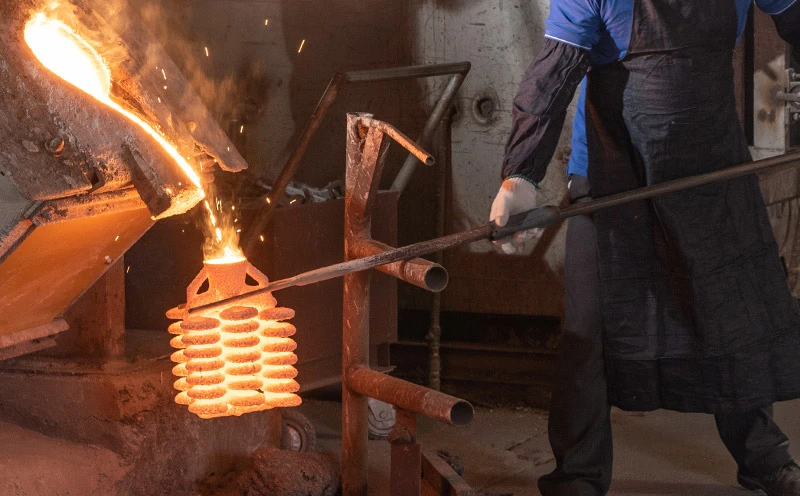
When discussing sand for casting, one must address the various types available. Green sand, the most commonly used, consists of silica sand, clay, water, and other additives. It is named for the ‘green’ strength it possesses, allowing for a solid but flexible mold. This type of sand provides excellent thermal stability and the ability to produce molds with intricate details. Its reusability adds to cost-effectiveness by minimizing waste and reducing the need for new raw materials.
For more precise casting needs, chemically bonded sands, such as furan and phenolic resins, offer enhanced strength and superior finish. These sands cure via chemical reactions, resulting in a rigid mold that holds high tolerance precision. Industries like aerospace, requiring exacting detail and finish, benefit significantly from these sands. They provide excellent dimensional accuracy and surface finish, essential for high-performance components.
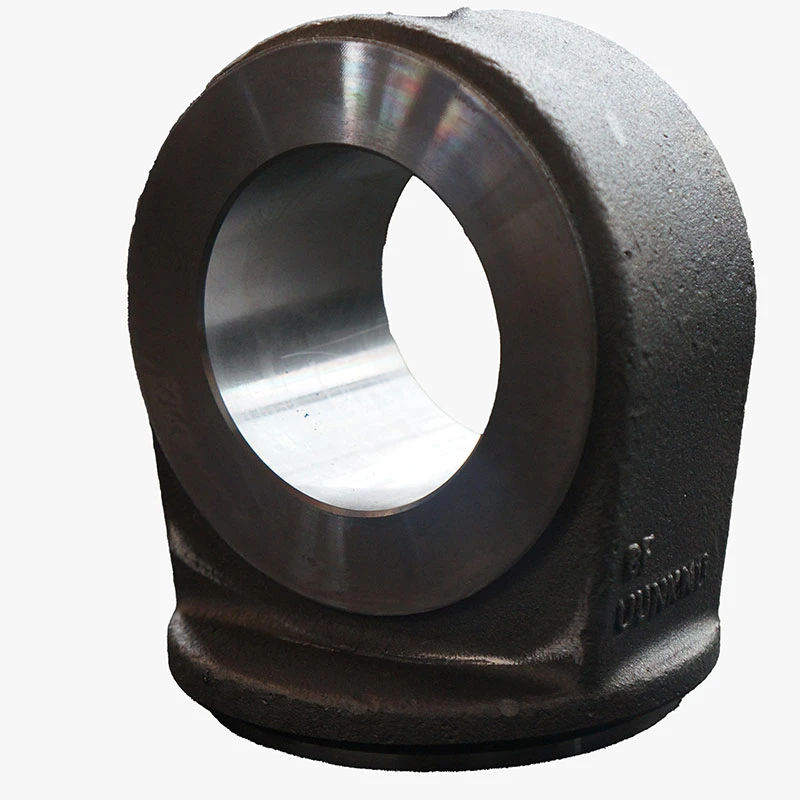
The importance of sand properties is paramount; grain size and shape directly influence casting quality. Fine-grained sands produce smooth surface finishes, crucial for aesthetic and functional requirements. Conversely, coarse grains can enhance permeability, allowing gases to escape during the casting process, reducing defects like porosity.
sand for casting metal
Expertise in mixing and reclaiming sand can drastically affect a foundry’s operational success. Consistent mixing procedures ensure homogeneity, reducing the likelihood of defects in the cast metal. Moreover, efficient sand reclamation systems enhance sustainability and reduce costs by enabling the reuse of sand without degrading quality. This aligns with modern environmental standards, promoting a circular economy within the casting industry.
Authoritative sources such as foundry industry associations and technical institutes provide extensive research on optimizing sand for casting processes. Publications detailing advancements in sand analysis technologies and reclamation strategies offer invaluable insights for industry professionals seeking to improve their practices. These resources serve to bolster a professional’s knowledge, ensuring that they remain at the forefront of technological advancements and industry standards.
Trustworthiness in sand supply and preparation is fundamental, ensuring the final product's integrity. Suppliers with ISO certification or similar credentials provide reassurance of quality and consistency, critical for maintaining production standards. Regular audits and quality checks on sand sources and preparation facilities further enhance reliability, ensuring the resulting castings meet stringent specifications.
In conclusion, sand for casting metal is an indispensable component of the foundry process, offering flexibility, cost-efficiency, and the potential for producing high-quality metal components. With continuous advancements in sand technology and reclamation methods, foundries can achieve greater efficiency and environmental compliance. By leveraging expertise, authoritative resources, and a commitment to trustworthiness, companies can excel in cast metal production, ensuring precision and quality in every piece produced.