Progressive die stamping, a pinnacle in modern manufacturing, serves as a luminary beacon in the realms of efficiency and precision in the metalworking industry. This intricate process has transformed production lines, streamlining outputs while minimizing human error — an achievement made possible through decades of expertise and innovation. With an amalgamation of advanced tooling and sophisticated press machines, progressive die stamping addresses complex manufacturing challenges with unparalleled ease and accuracy.
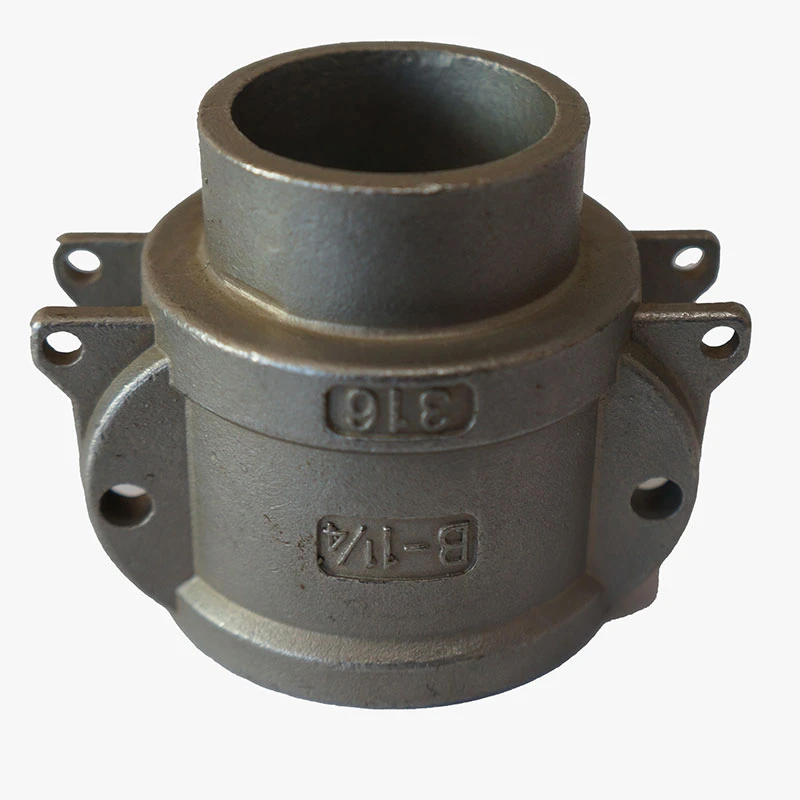
In the heart of this process lies the progressive die — a robust hero in its own right. It is specifically designed for high-volume production and involves a series of stations where various actions such as cutting, bending, and punching occur as the strip of metal travels through the press. This seamless integration of operations reduces wastages and enhances the consistency of metal parts, attaining precision that stands the test of both time and scrutiny.
Expertise in progressive die stamping is crafted through years of meticulous diligence and rigorous testing. Industry professionals wield this expertise by engineering dies to perform multiple operations in a single press stroke, bringing efficiency to the forefront of manufacturing. They ensure that every design aspect of the die conforms to the specifications required by diverse industries, from automotive to consumer electronics. This bespoke manufacturing capability highlights the adaptability of progressive die stamping in meeting diverse and complex customer requirements.
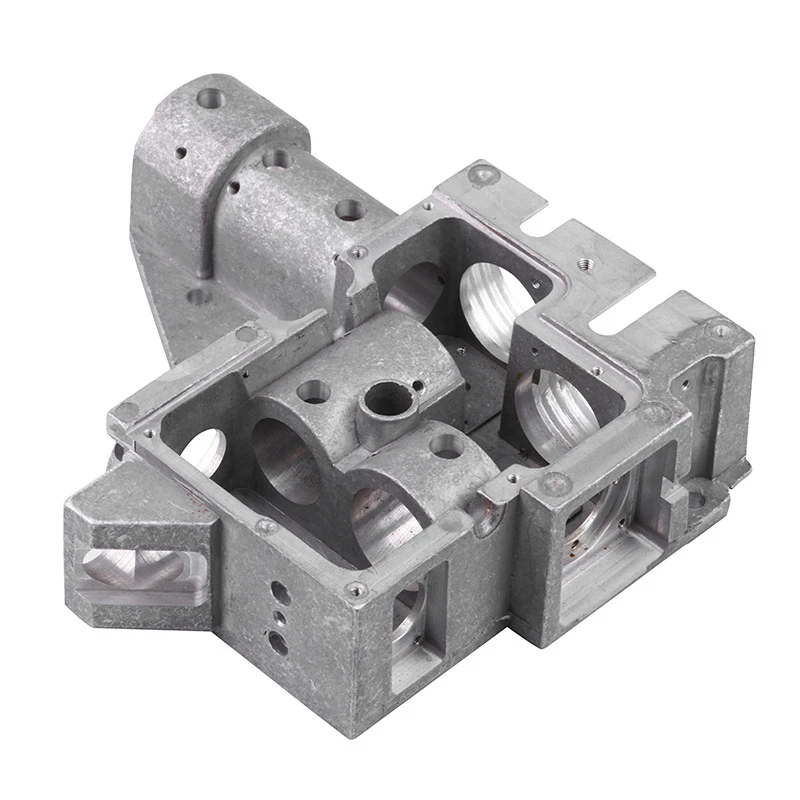
Authoritativeness in this domain is built upon a foundation of extensive research and continuous technological advancement. Progressive die stamping experts contribute to the field by sharing insights gained from intensive testing and successful application in high-pressure environments. This unwavering dedication to innovation and quality assurance has solidified progressive die stamping as an authoritative process, trusted by industries worldwide to deliver superior, high-precision components. The authoritative voice in this sphere is cultivated from a deep understanding of metallurgy, mechanical dynamics, and computer-aided design, which together forge the bedrock of progressive die stamping's unparalleled reliability.
progressive die & stamping
Trustworthiness is amplified through real-world applications and documented successes. Industries that rely on progressive die stamping do so because of the demonstrable trust in its processes, which have been validated over numerous decades. The precision, consistency, and speed provided by progressive die stamping are not just theoretical ideals but have been proven time and time again in manufacturing environments. This trustworthiness is further cemented through rigorous quality control and continuous monitoring, ensuring that each stamped part meets the highest standards of durability and functionality before it reaches the client.
Progressive die stamping stands as a testament to what is possible when experience and innovation intersect. It leverages advanced technology to foster environments where precision manufacturing is not merely an aspiration but a reality. Behind each successful application are teams of skilled engineers and toolmakers whose expertise seamlessly translate concepts into tangible high-quality products. Their commitment to excellence has not only enhanced manufacturing efficiencies but has also set a benchmark for quality that competitors aspire to reach.
In conclusion, progressive die stamping is more than just a manufacturing process; it is a paradigm of excellence born from rigorous experience, honed expertise, and unwavering trust in its methodologies. As industries continue to evolve and demands for precision and efficiency climb, progressive die stamping remains an indispensable ally, championing the cause of quality and consistency in the manufacturing landscape. It is an exemplar of how experience, expert knowledge, authoritativeness, and trustworthiness coalesce to drive innovation and maintain the highest echelons of manufacturing standards.