Unlocking the Potential of Zamak Die Casting A Comprehensive Exploration
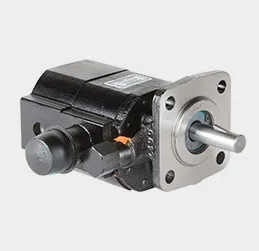
Zamak die casting has emerged as a cornerstone of modern manufacturing, providing unparalleled advantages across a spectrum of industries. Understanding the intricacies and benefits of this process unveils the reasons behind its growing popularity and its pivotal role in producing high-quality, durable components.
For over eight decades, Zamak, a family of alloys primarily composed of zinc, aluminum, magnesium, and copper, has been integral to the die casting industry. The name 'Zamak' is an acronym derived from the German names of these metals. This unique blend results in an alloy known for its remarkable properties such as dimensional stability, corrosion resistance, and incredible casting fluidity.
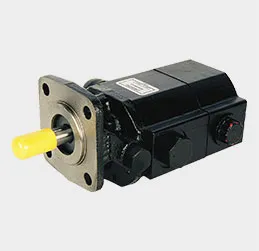
Manufacturers lean towards Zamak die casting for its superior precision and efficiency. Products cast from Zamak exhibit excellent surface finish and intricate detailing, making them ideal for applications where aesthetics and accuracy are paramount. This precision is achieved through the ability of Zamak to be cast with minimal shrinkage, maintaining the integrity and specifications of complex designs without additional processing.
In the realm of product manufacturing, Zamak die casting offers an exceptional cost-benefit balance. Due to the alloy’s lower melting point compared to other metals like aluminum or steel, Zamak die casting consumes less energy. This energy efficiency, coupled with the faster production cycles enabled by die casting, translates to reduced costs and quicker turnaround times. The lifespan and durability of Zamak components further enhance their cost-effectiveness, minimizing the need for frequent replacements and repairs.
zamak die casting
The versatility of Zamak alloys is highlighted across various sectors, from automotive and consumer electronics to furniture and toys. Its robustness and weight-to-strength ratio allow Zamak-cast components to undergo rigorous use while retaining functionality and safety. Furthermore, the smooth surface finish of Zamak castings often eliminates the need for extensive machining or additional finishing treatments, streamlining the manufacturing process.
Zamak die casting not only excels in technical proficiency but also adheres to sustainable manufacturing practices. The primary metal, zinc, used in Zamak alloys, is abundant and recyclable, aligning with industries' growing commitment to environmental responsibility. This sustainability factor, coupled with the alloy's minimal waste production during casting, positions Zamak die casting as an environmentally sound choice.
Safety is paramount in manufacturing, and Zamak alloys contribute significantly in this aspect. Their non-sparking characteristics, combined with high ductility and impact resistance, make them suitable for sensitive applications requiring heightened safety protocols.
To leverage the full potential of Zamak die casting, expertise and experience in the die casting process are essential. Manufacturers skilled in optimizing casting parameters can exploit the nuances of Zamak alloys to create components that excel in both performance and aesthetics. Selecting a manufacturer with a proven track record in Zamak die casting ensures that products will meet the demanding standards expected in today’s competitive market.
In conclusion, the unparalleled benefits of Zamak die casting — from cost efficiency and high precision to sustainability and safety — highlight its prominence and necessity in modern manufacturing. Its continued evolution promises even greater innovations, ensuring Zamak die casting remains at the forefront of industrial advancements. For industries seeking reliability, strength, and efficiency, Zamak die casting stands as the superior choice, paving the way for high-quality, durable products that meet and exceed expectations.