The stamping process is integral to the manufacturing world, a critical technique that has evolved to satisfy the demands of industries ranging from automotive to electronics. Understanding the intricacies of the stamping process provides valuable insight into both its application and its critical role across various sectors.
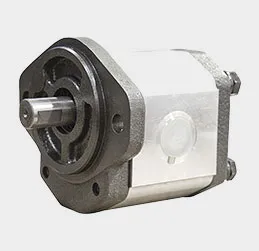
Stamping is a formidable technique characterized by its efficiency and precision. It involves placing a flat sheet of metal, typically a blank, into a stamping press where a tool and die surface form the metal into a desired shape. This process, reliant on the profound interplay of material science and engineering, can encompass a plethora of forming operations such as punching, bending, and embossing. Each operation demands an exact conformity to design specifications, ensuring that the resulting parts meet strict quality standards.
Experience with stamping reveals its unique ability to produce high volumes of complex components at relatively low costs. The economies of scale achieved through stamping make it an attractive choice for manufacturers, where minimizing production expenses while maximizing output is paramount. The repeatability of the process ensures that every stamped component is consistent with its predecessors, a factor crucial when aiming for zero defects in high-volume production runs.
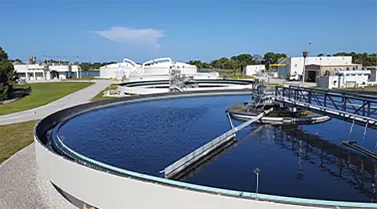
From an expertise standpoint, the stamping process is underpinned by advanced material sciences and precise engineering principles. It requires an accurate understanding of the mechanical properties of metals, as well as the stress and strain each metal can endure during the stamping operation. Innovation in tooling design is equally vital. The precision crafting of dies is a highly specialized skill requiring not just technical knowledge, but also vast experience to ensure that each tool performs reliably under the intense conditions of a stamping press.
The authoritativeness of the stamping process is seen in its adoption by leading manufacturing industries worldwide. Its application is vital in the automotive industry for creating car body panels and structural components. In electronics, it is used for producing myriad small intricate parts such as heat sinks and connectors, vital to the function of modern devices. Aerospace, too, relies heavily on stamping for lightweight, precise components crucial to flight safety and efficiency.
what is the stamping process
Trustworthiness in stamping emerges from its long history of delivering durable and reliable components. The process has been honed over decades, evolving with technological advances and incorporating innovative techniques such as computer-aided design (CAD) and finite element analysis (FEA) to predict and resolve potential issues before production commences. This predictive approach mitigates risks, ensuring that the stamped products perform their intended functions without fail.
Today's stamping processes are enhanced further by cutting-edge technologies like servo-drive presses that offer superior control over speed, force, and position. Such advancements ensure that the stamping process can accommodate modern materials including high-strength steels and aluminum, catering to the industry's ongoing shift towards lightweighting without compromising strength.
Moreover, the stamping industry is continuously adapting to environmental and sustainability concerns. Manufacturers are now more conscious of the need to minimize waste and utilize recyclable materials wherever possible, a testament to the process's adaptability and its alignment with global sustainability goals.
In conclusion, the stamping process is a cornerstone of modern manufacturing, vital to producing high-quality, reliable, and cost-effective components. Its success is not rooted solely in its technological capabilities but also in the deep expertise and accumulated experience of those who refine and implement it daily. As industries continue to evolve, so will stamping, continuing to serve as a trustworthy and authoritative manufacturing process for the future.