Vacuum assisted high pressure die casting (HPDC) represents a revolutionary advancement in the field of manufacturing, one which merges precision engineering with efficiency to create superior cast components. In exploring this cutting-edge technology, it's important to delve into its practical applications, benefits, and why it stands as a benchmark in die casting processes.
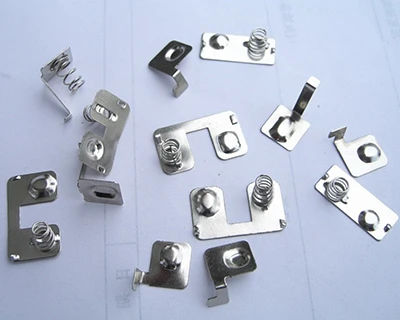
One major advantage of vacuum assisted HPDC is its ability to produce components with reduced porosity. Traditional high pressure die casting frequently encounters issues with gas entrapment, leading to weak spots and inconsistencies in the final product.
By incorporating vacuum assistance, the air within the die cavity is evacuated prior to metal injection. This reduces the potential for gas pockets and results in denser, more structurally sound components. Manufacturers report that this increased density enhances the fatigue strength of parts, making them ideal for high-stress applications like automotive and aerospace components.
In terms of surface finish, vacuum assisted HPDC excels by reducing the occurrence of defects such as blisters and surface porosity. This improved surface integrity not only enhances the aesthetic appeal of a component but also increases its suitability for post-casting treatments such as powder coating or plating, often demanded by clients in competitive markets.
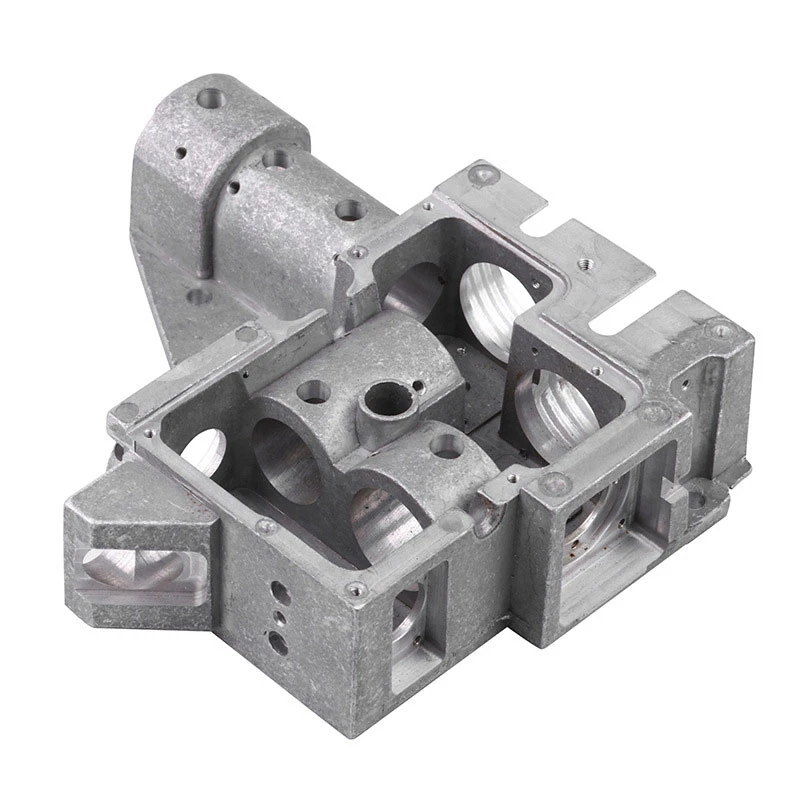
Vacuum assisted HPDC also allows for the casting of thinner walls without compromising strength. This capability is crucial for industries that are constantly pushing the boundaries of lightweight materials in pursuit of fuel efficiency and reduced emissions. Automotive manufacturers, for instance, utilize this technology to produce lighter but robust parts, contributing to the overall energy efficiency of vehicles. Case studies reveal that leading automotive companies have successfully replaced traditional steel parts with aluminum and magnesium cast parts, achieving significant weight reductions and concomitant performance gains.
vacuum assisted high pressure die casting
From an environmental and economic perspective, vacuum assisted HPDC presents significant advantages. The process minimizes waste by reducing scrap rates and improving yield, as fewer parts are rejected due to casting defects. This efficiency translates directly into cost savings for manufacturers, as well as a reduced environmental footprint due to less material usage and waste. Furthermore, the improved quality and reliability of components mean fewer replacements and repairs over the product lifecycle, reducing resource consumption even further.
When discussing expertise and authoritativeness, industry leaders with decades of experience in die casting emphasize the transformative impact of vacuum assisted technology. Engineers and metallurgists underscore its role in elevating the standards of component production, describing it as a game-changer in the industry. This sentiment is echoed by industry publications and academic papers that highlight successful integrations of the technology into manufacturing lines, demonstrating measurable improvements in product performance and production efficiency.
In terms of trustworthiness, case studies from reputable manufacturers provide concrete evidence of the technology's benefits. These studies often include performance data and customer testimonials that vouch for the reliability and superiority of vacuum assisted HPDC parts. The consistent quality assurance associated with this process has led industries to trust and adopt it widely, making it a staple in modern manufacturing.
In conclusion, vacuum assisted high pressure die casting not only exemplifies technological advancement but also delivers tangible benefits across multiple dimensions of manufacturing. It is a process that ensures components are manufactured to the highest quality, economically and sustainably, underpinning its growing adoption and esteemed reputation in the industry. As technology continues to evolve, vacuum assisted HPDC stands poised to meet the challenges of tomorrow's manufacturing landscapes.