Sand casting, a revered method in the manufacturing industry, serves as a cornerstone for creating a multitude of products. It remains one of the most versatile and cost-effective methods for forming complex metal parts. As industries have evolved, so too have the techniques and materials used in sand casting. Understanding the different types of sand casting processes can provide deeper insight into their applications and benefits, enhancing both your manufacturing strategy and product quality.
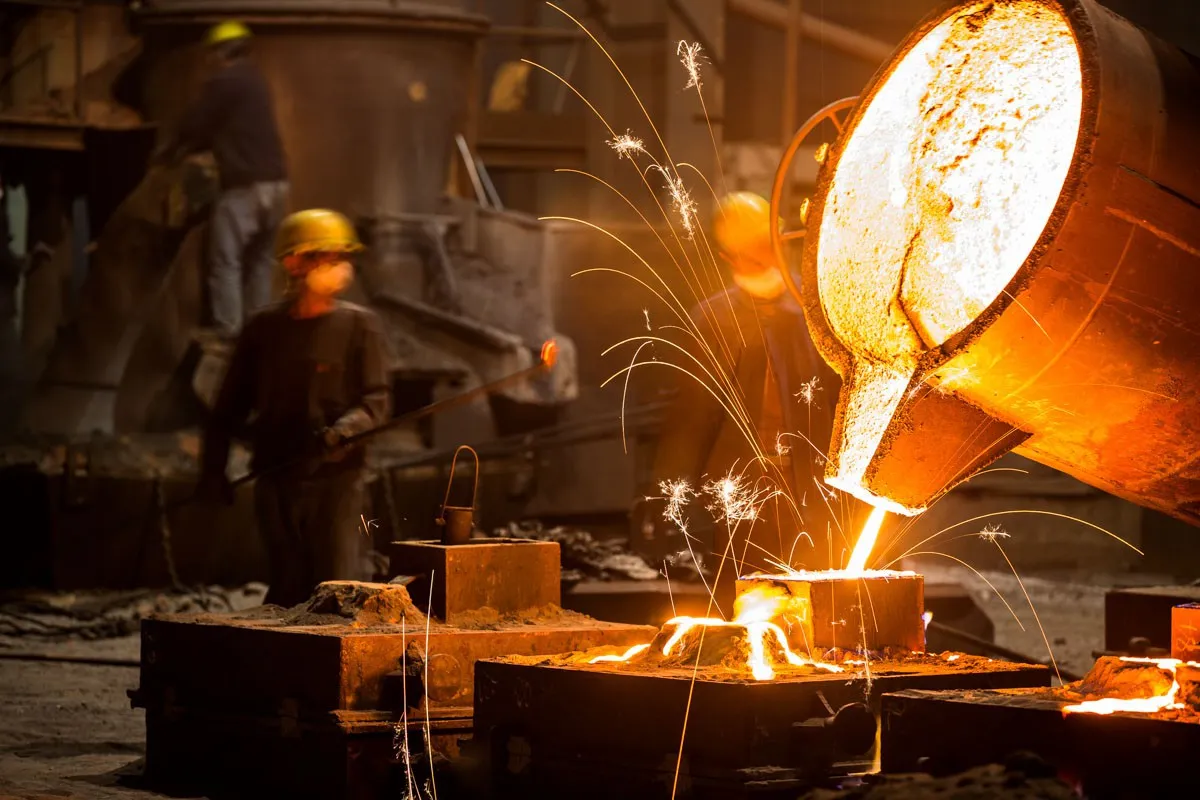
Green sand casting is arguably the most traditional form of sand casting, favored for its cost-efficiency and adaptability. This technique employs a mixture of sand, clay, water, and other additives to create a moldable compound. Its name derives from the fact that the sand is not ‘green’ in color, but rather ‘wet’ or ‘damp’. Green sand casting is ideal for high-volume production due to its relatively low cost and ability to quickly form and reshape molds. It's particularly effective for non-ferrous metal casting, including aluminum and brass, and widely used in automotive and machinery component production.
Another vital variation is the dry sand casting technique. This method involves using organic binders instead of clay, along with drying or baking the mold, which enhances its rigidity and accuracy. By doing so, it reduces the likelihood of defects and improves dimensional tolerance. While slightly more costly and time-consuming than green sand molds, dry sand casting offers superior surface finish and is better suited for intricate parts that require a higher level of detail and accuracy. Hence, it finds usage in the aerospace and automotive sectors for casting critical and detailed components.
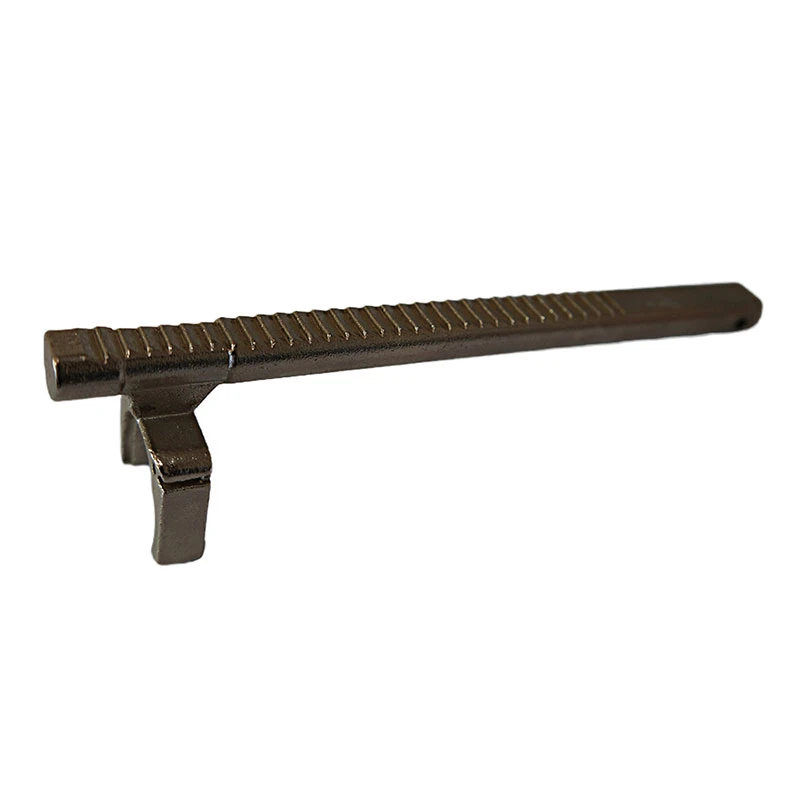
Resin sand casting, also known as no-bake casting, distinguishes itself by using a chemically bonded sand mixture. This method offers significant advantages in producing high-precision and high-quality castings, enabling excellent surface finishes and dimensional accuracy without the need for heat-based hardening processes. Resin sand casting is particularly valued when manufacturing low-volume, oversized components such as pumps, valves, or heavy-duty machinery parts due to its superior strength and stability.
types of sand casting
The shell mold casting is another specialized process involving the creation of a mold from a thin shell of sand bonded by a thermosetting resin. This technique provides exceptional accuracy, smooth surface finish, and excellent dimensional tolerances, even when casting complex geometries. It's highly suitable for intricate designs and often used in the manufacture of small to medium-sized parts with detailed contours, applicable in the automotive and hardware industries.
Further advancing casting technology, the vacuum mold casting method uses un-bonded sand and a vacuum to hold the mold together. This method eradicates certain issues like moisture-related defects and ensures a reduced environmental impact due to the absence of binders. Although limited in its extensive adoption due to higher costs, vacuum mold casting is beneficial for specialized applications requiring exceptionally high precision and strength.
In terms of expert application, understanding the nuances of each sand casting type is essential. It enables manufacturers to select the appropriate technique based on the complexity of the design, the metal to be cast, production volume, and budget considerations. By optimizing these factors, businesses can enhance production efficiency, product quality, and ultimately maintain a competitive edge in the industry.
Selecting the right sand casting process is a decisive factor in manufacturing excellence. From simple shapes to highly complex structures, each technique offers unique benefits, ensuring there's a specific sand casting method tailored to meet each company's needs. Embracing the right technology not only refines production capabilities but also solidifies a reputation for quality and reliability in the competitive market landscape. This strategic approach underscores the significance of a well-informed, detailed understanding of sand casting types, paving the way for innovation and growth in manufacturing domains.