Die casting is a versatile and widely employed manufacturing process that produces complex metal parts with excellent dimensional accuracy and smooth finishing. Understanding the different types of die casting is crucial for manufacturers and product designers to select the most appropriate method for their applications. This choice impacts the quality, cost,
and performance of the final components. As industries strive for efficiency and innovation, let's explore the prominent types of die casting and their unique advantages.
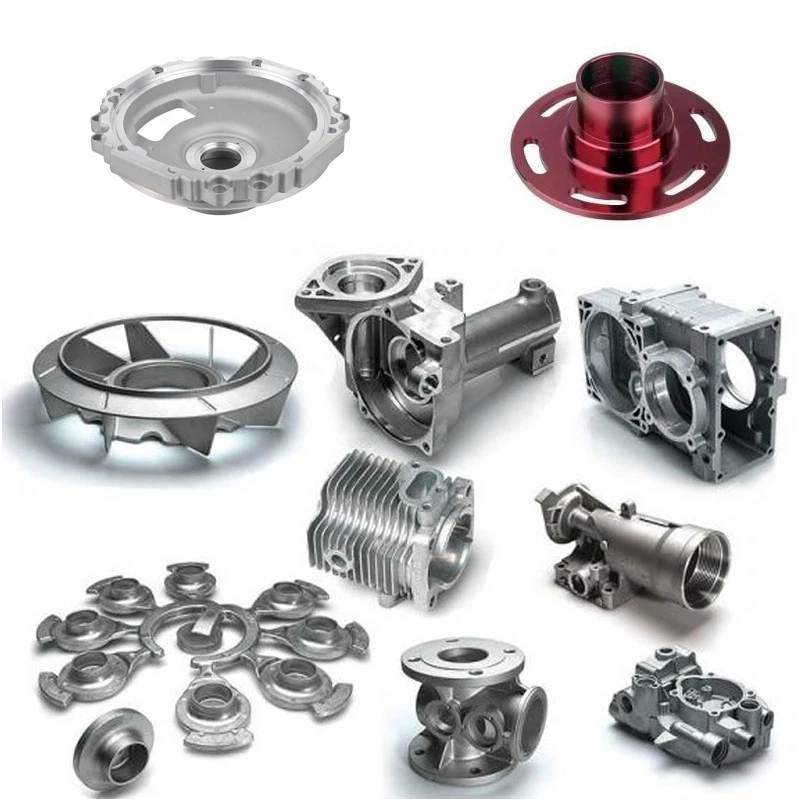
Pressure die casting, also known as high-pressure die casting (HPDC), is the most common form used today. This method involves forcing molten metal into a mold cavity under high pressure, creating strong and durable components. Emphasizing precision and speed, high-pressure die casting is ideal for producing large volumes of small to medium-sized parts, typically used in automotive, electronics, and consumer products. The efficiency of HPDC is reflected in the minimal post-process machining required, reducing both production time and waste, which is a crucial consideration for manufacturers aiming for sustainable practices.
In contrast, low-pressure die casting (LPDC) uses significantly lower metal injection pressure, offering distinct advantages in producing parts that require superior mechanical properties and aesthetic qualities. LPDC is particularly beneficial for manufacturing complex shapes with intricate details and is widely used in the production of high-quality aluminum wheels, structural components, and parts for the aerospace sector. The slower injection process allows for better control over the material flow, reducing the chances of defects such as porosity, and ensuring uniform material properties across the component.
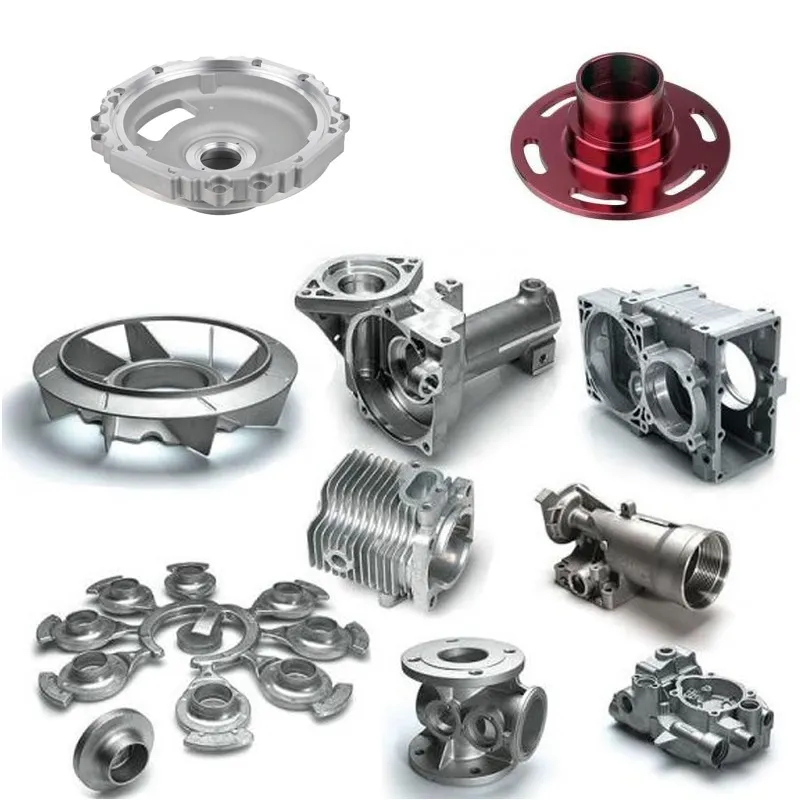
On the other hand, gravity die casting, often termed as permanent mold casting, leverages gravity to fill the mold with molten metal without additional pressure. This method is best suited for thicker-walled and less complex parts, providing excellent surface finish and dimensional accuracy for specific applications like automotive engine components and industrial machinery parts. While generally slower than pressure-based methods, gravity die casting offers benefits in terms of lower initial tooling costs and higher flexibility for small to medium production runs.
types of die casting
For applications requiring even more specialized approaches, vacuum die casting presents a sophisticated variation wherein air is evacuated from the mold cavity before metal injection. This practice minimizes air entrapment within the mold, substantially reducing porosity and increasing the mechanical integrity of the final product. Vacuum die casting is indispensable in producing lightweight, high-strength components essential for the aerospace and high-performance automotive industries. Manufacturers leveraging this method benefit from enhanced component reliability and longevity, critical in safety-centric sectors.
Squeeze casting is another noteworthy method, combining the benefits of conventional casting and forging. By exerting high pressure on the molten metal within a closed die, squeeze casting yields parts with superior mechanical properties comparable to wrought materials. This technique is most advantageous for high-strength applications, including structural components and heavy-duty machinery, where toughness and fatigue resistance are paramount. The ability to produce dense, fine-grained structures makes squeeze casting a game-changer for industries demanding exceptional performance standards.
Each type of die casting presents unique benefits and limitations, demanding a thorough understanding of the specific requirements of the intended application. Cost considerations, desired production volume, material selection, and part complexity are vital factors influencing the decision-making process. Furthermore, advancements in die casting technologies continue to emerge, offering manufacturers opportunities to enhance product quality while minimizing environmental impact and resource consumption.
Embracing the insights gained from understanding die casting types empowers industries to push boundaries in innovation and product development. Staying informed about the latest advancements and trends in die casting not only guides better decision-making but also fosters a culture of learning and adaptation crucial for sustaining competitiveness in the dynamic global market. Manufacturers poised to leverage the right die casting techniques can achieve remarkable improvements in efficiency, quality, and sustainability, thereby reinforcing their position as industry leaders.