Titanium die casting stands out as a compelling process in the manufacturing sector, known for its precision and ability to produce complex shapes with high strength and low weight—a combination that few other materials can match. Deriving from extensive industry experience, the science behind titanium die casting reflects expertise and innovation, making it a crucial process across various sectors, including aerospace, automotive, and medical devices.
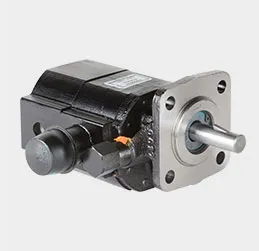
Experience in the field of titanium die casting reveals its superiority over other metals like aluminum and zinc, primarily due to its exceptional corrosion resistance. In real-world applications, products manufactured using titanium die casting have demonstrated longevity and robust performance, qualities highly desired in aerospace applications where materials are subject to extreme conditions. For instance, aerospace engineers often choose titanium components for parts exposed to sea environments or those needing to withstand significant thermal variations without compromising structural integrity.
From an expertise standpoint, the process of titanium die casting requires a deep understanding of the alloy’s properties, particularly its melting range and reactivity. Titanium's high melting point, around 1668 degrees Celsius, presents challenges that demand specialized equipment and processes to achieve optimal results. Cooling rates, mold design, and the handling of molten titanium are crucial factors affecting the final product’s quality. Technological advancements have introduced ceramic and graphite molds tailored to enhance titanium die casting by improving heat distribution and reducing the likelihood of defects such as porosity or cracking.
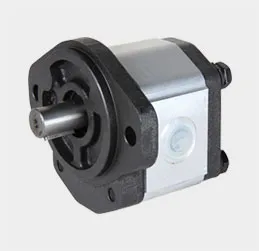
Authoritativeness in the domain of titanium die casting is established through innovative engineering and state-of-the-art research facilities committed to continuous improvement of the process. Companies leading the charge are often those that invest significantly in prototyping and simulation technologies, allowing engineers to perfect die cast designs before actual production. These leaders collaborate closely with industry-specific regulatory bodies to ensure their processes meet rigorous international standards, further certifying their roles as authoritative figures within the industry.
titanium die casting
Trustworthiness is built upon decades of proven performance and compliance with international quality certifications. Manufacturers involved in titanium die casting adhere strictly to environmental and safety regulations, assuring clients of their commitment to sustainable practices and worker safety. Additionally, these companies provide exhaustive testing and quality assurance protocols; each titanium component undergoes rigorous non-destructive testing to confirm its reliability and performance potential before being sold to clients.
In the medical device industry,
the biocompatibility of titanium is a critical advantage. Titanium die casting techniques have advanced the production of surgical tools and implants, highlighting their role in developing devices that safely integrate with the human body. The trust placed in these products is due to the detailed quality control and emphasis on using certified, pure titanium, ensuring patients’ safety and the efficacy of medical treatments.
In conclusion, the landscape of titanium die casting is one marked by exemplary expertise, profound experience, and esteemed authority within the manufacturing industry. The process is not merely about shaping titanium but mastering its physical properties to forge components that excel in conditions where lesser materials would fail. Trustworthiness is not just an implied promise but a foundational element practiced daily in this niche, solidifying titanium die casting as an indispensable part of modern manufacturing and innovation.