In the world of manufacturing, the price of stamping parts is a critical factor that influences decision-making, budgeting, and overall production efficacy. Understanding the variables that affect the price of these essential components can lead to more informed purchasing choices and improve the overall operational efficiency of manufacturing processes.
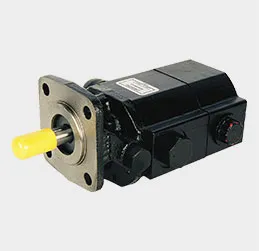
Stamping parts are integral to various industries, including automotive, aerospace, electronics, and appliances. The complexity of the design, the choice of materials, and the precision required during production combine to affect the final cost. A discerning buyer must navigate these elements to achieve a balance between quality and cost.
The materials chosen for stamping parts have a significant impact on pricing. Common materials include steel, aluminum, brass, and copper, each offering distinct advantages and cost implications. Steel is favored for its strength and durability, while aluminum is valued for its lightweight and corrosion resistance. The choice of material is often dictated by the part’s intended application, which in turn influences the final price. Manufacturers must consider the material’s cost per pound, availability, and any special treatments required, such as galvanizing or anodizing, which can add to the overall expense.
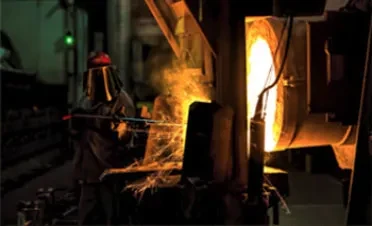
Another decisive factor in the cost of stamping parts is the complexity of the design. Intricate designs may require more advanced machinery, precision tools, and a higher degree of skilled labor, all contributing to an increased price. It’s crucial to engage in a thorough design for manufacturability analysis to ensure that parts are optimized for production without compromising quality. Simplifying a component’s design where possible can lead to considerable cost savings without affecting performance.
The production volume is also a key determinant of pricing. Higher volumes generally allow for economies of scale, reducing the cost per unit as the fixed costs of production are spread over more units. It's beneficial to forecast demand accurately to achieve optimal pricing.
Tooling costs further influence the price of stamping parts. Creating custom dies and molds, which are essential for part production, involves upfront costs that can be substantial. However, investing in high-quality tooling can enhance production efficiency and part quality, ultimately offering a better return on investment. Evaluating the cost of tooling relative to its lifespan and the volume of parts it will produce is essential.
stamping parts price
The geographical location of the manufacturer can play a role in cost determination due to differences in labor rates, material costs, and overhead expenses. While outsourcing to regions with lower labor costs might seem attractive, it is vital to consider factors such as transportation costs, import duties, and potential risks associated with long supply chains, such as delays or quality control challenges.
Furthermore, the precision required in stamping can influence costs. Tighter tolerances generally require more rigorous quality control and advanced machinery, which may increase production time and cost. Communicating tolerance requirements effectively with manufacturers ensures that they understand the critical dimensions that must adhere to specific standards and those that allow for more flexibility, thereby optimizing manufacturing efficiency.
In recent years, technological advancements and process automation have also impacted stamping part prices. The integration of CAD/CAM systems and robotic automation in stamping facilities can lead to enhanced accuracy and reduced labor costs, offering competitive pricing advantages. Staying updated with the latest technologies and choosing manufacturers who invest in modern production techniques can lead to improved quality and cost efficiencies.
Choosing the right supplier is paramount in controlling costs and ensuring high-quality outcomes. It is advisable to partner with suppliers who have a proven track record, industry certifications, and transparent pricing models. Building a long-term relationship with a reliable supplier can provide insights into cost-saving opportunities, such as bulk ordering discounts or alternative material options, and ensure timely delivery of parts.
Buyers must practice due diligence, seeking quotes from multiple suppliers and conducting thorough cost analyses to ensure competitiveness. Moreover, considering a supplier's expertise, manufacturing capabilities, and quality assurance processes is critical. Suppliers that provide comprehensive value-added services such as design support, prototyping, and just-in-time delivery can offer significant advantages.
Ultimately, understanding the dynamics of stamping part pricing requires a blend of technical knowledge, market research, and strategic supplier engagement. By thoughtfully examining these factors, businesses can optimize their purchasing strategies, achieve cost efficiencies, and maintain a competitive edge in their respective markets. Implementing a comprehensive approach to purchasing stamping parts not only impacts the bottom line positively but also aligns with broader operational goals of quality assurance and supply chain robustness.