Small metal stamping parts have become pivotal components across various industries due to their versatility, durability, and precision. These parts, often unnoticed by the general public, form the backbone of countless products and applications, ranging from automotive and electronics to medical devices and construction tools. Understanding their manufacturing process, application, and benefits provides insight into why they are trusted by professionals worldwide.
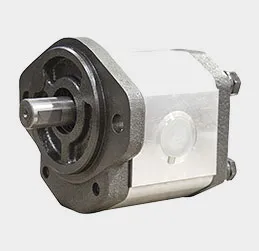
The production of small metal stamping parts involves intricate processes that require advanced technology and expertise. Utilizing high-tonnage presses, manufacturers can produce parts that meet exact specifications in both dimensions and material properties. This precision is crucial, particularly in sectors like aerospace and electronics, where even the smallest deviation can lead to significant performance issues. Expert technicians carefully design dies and tools, ensuring that every stamp aligns perfectly to create uniform, dependable parts.
One of the foremost advantages of metal stamping is its cost-effectiveness, particularly in large-scale production. The ability to reproduce identical parts rapidly without compromising quality allows businesses to meet tight production timelines and cost requirements. Furthermore, stamping utilizes materials efficiently, reducing waste significantly compared to other manufacturing methods. This efficiency not only lowers production costs but also aligns with sustainable manufacturing practices, a growing concern in today’s industrial landscape.
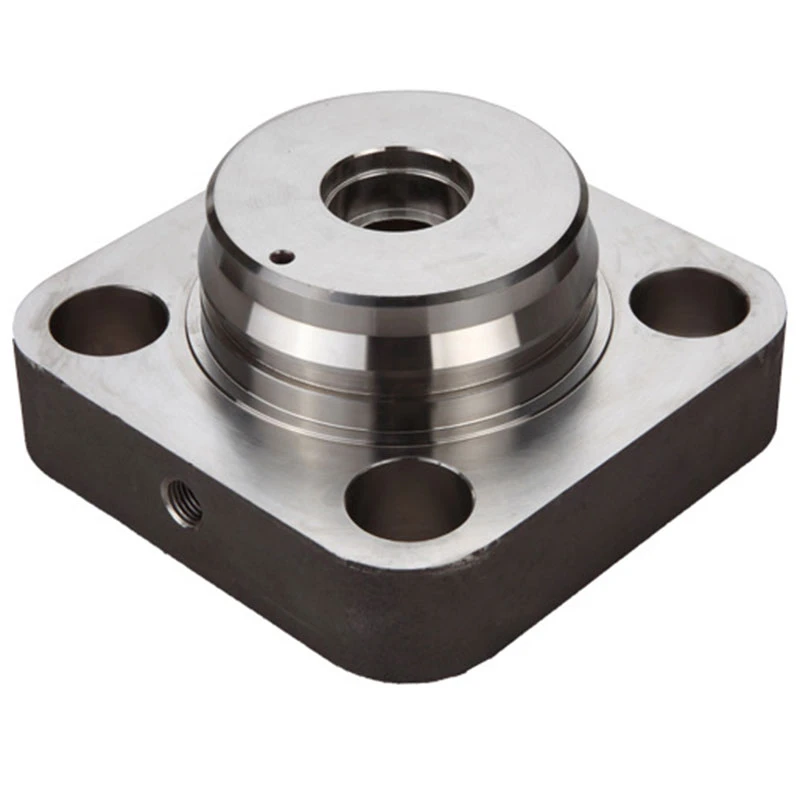
Small metal stamping parts are synonymous with strength and resilience. Metals such as stainless steel, aluminum, and copper are preferred due to their sturdiness and resistance to corrosion, making them ideal for components that must withstand harsh conditions. For instance, in the automotive industry, stamped metal components are used in engines, transmissions, and vehicle frames, where reliability is paramount. Similarly, in the realm of consumer electronics, these parts ensure the longevity and robustness of devices like smartphones and laptops.
Moreover, the adaptability of stamping technology accommodates a variety of designs and applications. Whether a complex design with tight tolerances or a simple shape, metal stamping can produce parts that meet diverse needs without sacrificing quality. This scalability is particularly beneficial for industries that require a range of products with differing specifications, allowing for flexibility in production planning and inventory management.
small metal stamping parts
The credibility of manufacturers specializing in small metal stamping parts is enhanced by their commitment to industry standards and certifications. Companies adhering to ISO 9001 and other quality management systems demonstrate their dedication to maintaining high manufacturing standards. Such certifications instill confidence in clients, assuring them of the reliability and performance expected of their components.
The expertise in small metal stamping is continually evolving, with advancements in technology driving innovation in manufacturing methods. Computer-aided design (CAD), along with computer-aided manufacturing (CAM), ensures even greater precision and efficiency. Laser cutting and plating techniques also boost the quality and finish of stamped parts, expanding the potential for customization and enhancing the aesthetic appeal without forgoing functionality.
Building trust in the realm of small metal stamping involves transparent communication with clients. By providing detailed specifications, progress updates, and quality assurance measures, manufacturers can build strong relationships with their customers. This trust extends beyond the initial sale, fostering long-term partnerships where clients feel confident that their precise needs will be met consistently.
In conclusion, small metal stamping parts play a critical role in the success of numerous industries. Their reliance hinges on the combination of expert craftsmanship, cutting-edge technology, and robust quality management systems. As industries continue to evolve, the demand for precise, durable, and cost-effective components like those produced through metal stamping is only set to rise, further solidifying their indispensable role in modern manufacturing.