Sand casting is one of the most traditional and widely used methods in metal casting. Renowned for its reliability and cost-effectiveness, it is a critical technique in the manufacturing process for numerous industrial products. Despite its antiquity, sand casting continues to hold its ground as a vital production process in modern engineering. From intricate art pieces to robust automotive components, the technique's versatility is unmatched.
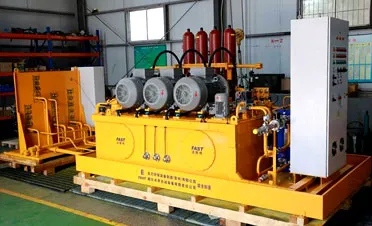
At its core, sand casting involves creating a mold from a mixture of sand and clay, into which molten metal is poured. This process stands out due to its cost efficiency when producing small to medium-sized runs, particularly when the scale of production does not justify the expenses associated with high-end technologies like die casting.
The primary advantage of sand casting is its remarkable adaptability. Almost any metal can be cast using this technique, from aluminum and bronze to more durable alloys like iron and steel. This flexibility allows manufacturers to pivot easily between projects and customize the metal's properties to suit specific applications, whether it be enhanced thermal resistance or greater tensile strength.
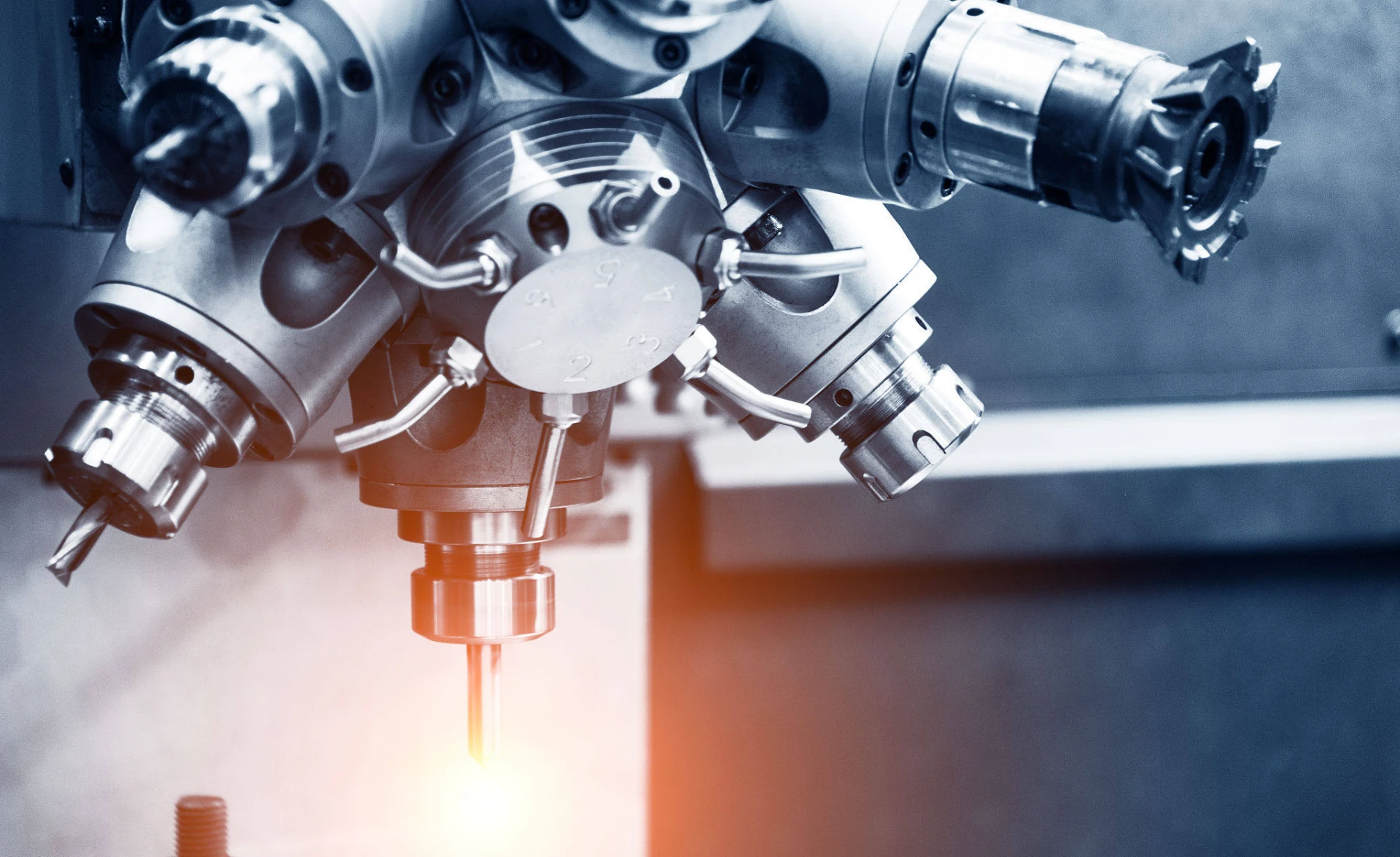
Expertise in sand casting requires comprehensive knowledge of mold construction. The sand must possess the apt granularity to prevent deformation while ensuring seamless removal of the finished product. Attention to detail in mold preparation is paramount to avoid defects such as blowholes or misruns, which can compromise the final product's integrity.
In the realm of sand casting, experience is invaluable. Seasoned craftsmen understand the subtle nuances of temperature control, pouring speed, and cooling rates, all of which influence the quality and durability of the final casting. It’s an art that blends precise engineering with a tactile understanding of the materials involved. Without experience, even the most robust sand casting setup can falter, leading to inefficiencies and subpar outputs.
sand casting pdf
The authority in sand casting stems from expert certifications and industry acknowledgment. Acclaimed foundries often hold certifications such as the ISO quality assurance standard, ensuring their processes remain consistently excellent. Such certifications not only affirm the technical prowess of the operation but also build trust with clients seeking reliable manufacturing partners.
Trustworthiness is built through transparency and proven track records. Manufacturers that use sand casting must be willing to provide clients with detailed insights into their processes and quality control measures. A durable sand casting piece not only meets the specifications laid out by the client but often exceeds their expectations in terms of durability and performance.
Innovations in sand casting technology continue to emerge. Automations and computer simulations in the mold-making process have enhanced precision and reduced time lags, offering clients quicker turnaround times without sacrificing quality. These advancements fortify the sand casting method’s relevance in an era increasingly dominated by digitization and AI.
In conclusion, sand casting remains a cornerstone of the manufacturing industry, its expertise built on generations of craftsmanship and scientific advancement. Its enduring success hinges on a combination of skill, innovation, and a commitment to quality and transparency. For businesses seeking a reliable, flexible, and cost-effective method of production, sand casting represents an optimal choice that connects the trusted past with the exciting possibilities of the future.