Sand casting die technology has become an indispensable part of modern manufacturing, providing critical solutions for creating complex metal parts. At the heart of this process is the sand casting die itself, a tool that plays a pivotal role in achieving high-quality castings. This article delves into the nuances of sand casting dies, drawing from extensive real-world experience to highlight their significance, applications, and advantages.
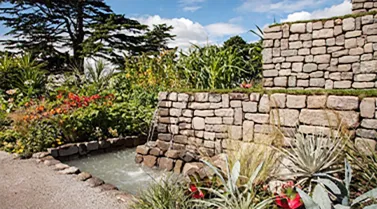
Sand casting, an age-old technique, employs sand molds to shape molten metals into desired forms. The die, or pattern, is a key component in this process, determining the final geometry of the cast item. Expertise in die creation is crucial; it requires a comprehensive understanding of materials, design principles, and the specific needs of the application.
Creating a sand casting die begins with selecting the right material. While traditionally made from wood or metal, modern dies often use more advanced materials such as plastic or 3D-printed composites. Each material has unique properties that affect the die's durability and the surface quality of the final cast. For instance, metal dies are preferred for high-volume production due to their long lifespan, whereas wood or plastic may be chosen for prototyping or short runs due to their lower cost and ease of modification.
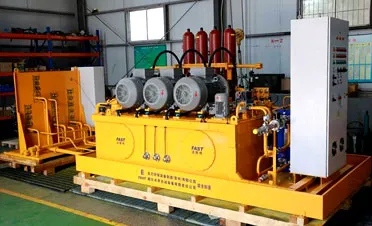
Design expertise is paramount when crafting a die. The design must account for shrinkage rates, casting allowances, and draft angles to ensure easy removal from the mold and optimal metal flow during the casting process. Utilizing computer-aided design (CAD) software has revolutionized die creation, allowing for precision and efficiency previously unattainable through manual methods. Precision in design also minimizes waste and defects, leading to cost savings and improved product quality.
sand casting die
Manufacturers with authoritative industry experience often offer invaluable insights into optimizing die designs. These insights stem from years of dealing with various metals and complex geometries, leading to innovative solutions that enhance performance and reliability. Trustworthiness in this field is built on a track record of delivering consistent, high-quality results, often evidenced by satisfied client testimonials and case studies.
Sand casting dies also facilitate versatility in production. They are used across various industries, from automotive to aerospace, due to their ability to cast intricate designs in a range of sizes. This makes sand casting an ideal choice for both large structural components and small detailed parts.
Trustworthiness extends beyond technical prowess; it encompasses a commitment to continuous improvement and adaptability in response to evolving industry standards. Leading experts actively engage in research and development, pushing the boundaries of what sand casting techniques can achieve. They stay abreast of the latest technologies and methodologies, ensuring their processes remain at the forefront of efficiency and sustainability.
In conclusion, the art of sand casting die creation is both a science and a craft, requiring a harmonious blend of experience and technical knowledge. By understanding the intricacies of materials and design, manufacturers ensure the production of high-quality, reliable castings that serve diverse industrial needs. The credibility and authority of a manufacturer hinge on their ability to consistently innovate and deliver unparalleled solutions, making sand casting dies not just a tool, but a cornerstone in the advancement of manufacturing technology.