Red sand casting is an age-old method that has long been employed in the manufacturing industry due to its ability to produce detailed and complex metal products with ease and efficiency. As an experienced practitioner in this field, I have witnessed firsthand the numerous advantages and challenges associated with red sand casting, making it a topic of great fascination and expertise.
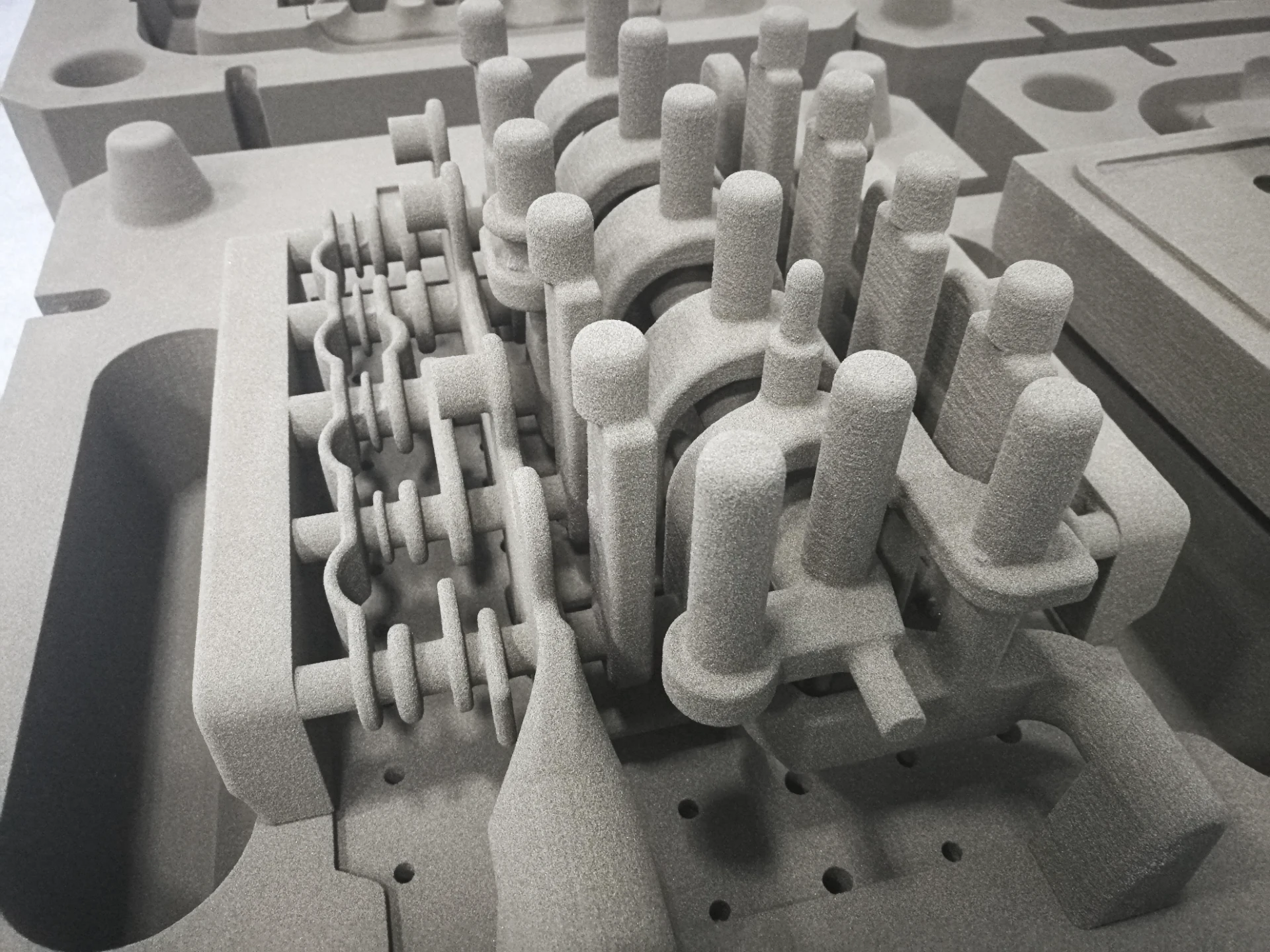
The red sand casting process involves creating a mold from a mixture of sand, clay, and water, which is then used to form metal parts by pouring molten metal into the mold. This technique is particularly renowned for its cost-effectiveness and versatility, allowing for the production of both small and large metal parts across various industries, including automotive, aerospace, and construction.
One notable advantage of red sand casting is its ability to produce highly intricate and complex shapes. The fine grain quality of red sand allows for precise detailing, which is crucial for components that require exact specifications. This capability makes it an ideal choice for creating customized parts that cater to specific design needs, setting it apart from other casting methods that may not offer the same level of precision.
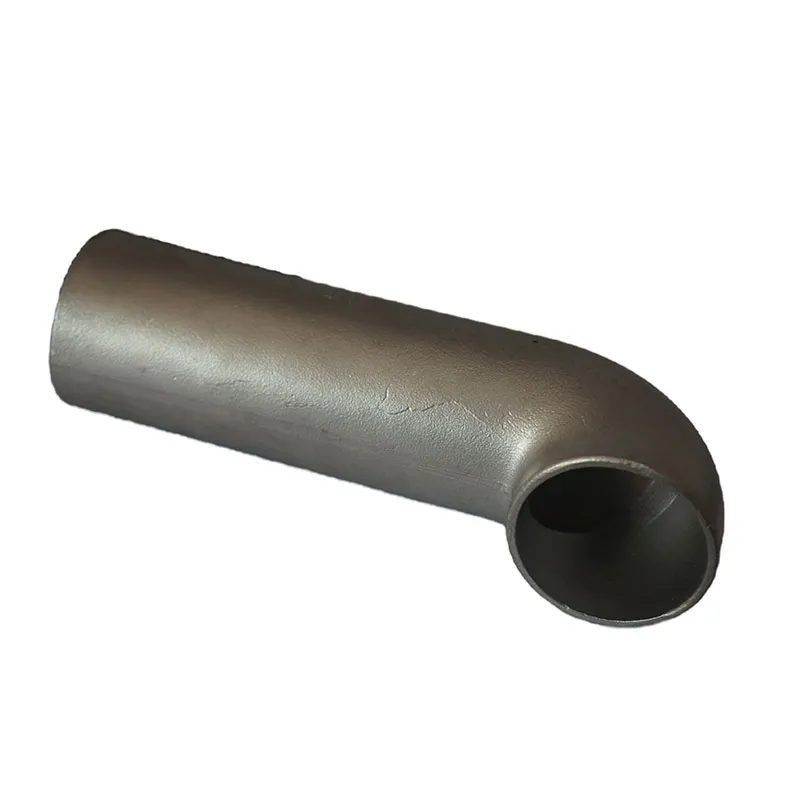
Moreover, red sand casting is a sustainable manufacturing process. The materials used in the molds, primarily sand and clay, can be recycled and reused for multiple casting cycles, significantly reducing waste. This eco-friendly aspect of red sand casting not only benefits the environment but also contributes to the overall sustainability goals of manufacturing companies looking to minimize their carbon footprint.
However, like any manufacturing process, red sand casting is not without its challenges. One of the primary concerns is the potential for defects such as porosity or shrinkage, which can occur during the cooling phase of the metal. To mitigate these issues, it is vital to ensure precise control over the mold's temperature and the composition of the sand mixture. Through extensive experience, I've learned that a meticulous approach to monitoring and adjusting these parameters greatly enhances the quality and success of the final product.
red sand casting
Furthermore, expertise in red sand casting requires an in-depth understanding of the properties of various metals and alloys used in the process. Certain metals,
such as aluminum and iron, have unique properties that affect how they behave during casting. Being well-versed in material science is crucial for making informed decisions about which metals are best suited for specific products, ensuring the desired strength, weight, and durability are achieved.
In terms of practical application, my years of experience have taught me the importance of collaborating closely with clients to fully understand their requirements and expectations. Effective communication ensures that the red sand casting process is aligned with the client's vision, resulting in a product that meets or exceeds their standards. Trust is built through transparency and a commitment to quality, allowing for long-term partnerships and repeat business.
The authority of red sand casting in the manufacturing industry is evidenced by its longstanding use and the continuous advancements made within the field. New technologies and innovations, such as 3D printing for mold creation and advanced computer simulations, are being integrated into traditional casting practices, enhancing accuracy and efficiency while opening up new possibilities for design and production.
Lastly, the trustworthiness of a red sand casting provider is paramount. Ensuring consistent quality and reliability requires not only experience and expertise but also adherence to industry standards and regulations. Quality assurance processes, including rigorous testing and inspections, are necessary to maintain high standards and deliver products that clients can trust.
In conclusion, red sand casting remains a cornerstone of modern manufacturing, revered for its adaptability, sustainability, and intricate design capabilities. By combining traditional techniques with innovative advancements and maintaining a focus on quality and client collaboration, practitioners can deliver exceptional results that meet the evolving needs of a diverse array of industries.