The art and science of quality die casting have undergone significant advancements over the years, ensuring products meet specific safety and performance standards while also enhancing visual appeal. Understanding the journey from raw material to finished product reveals insights into this nuanced process that melds engineering expertise with manufacturing ingenuity.
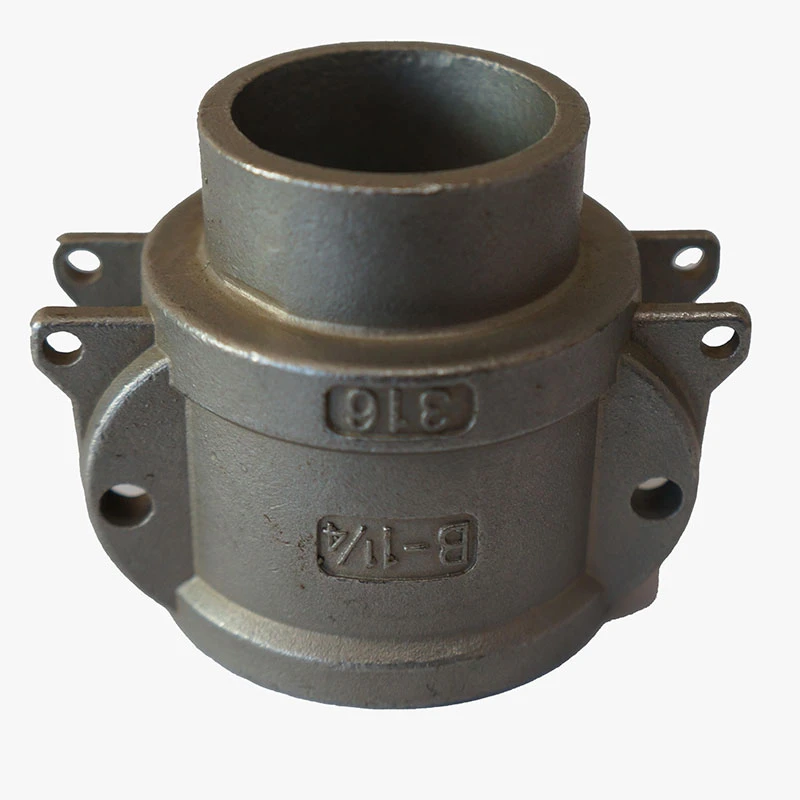
Die casting involves injecting molten metal into a mold cavity to create high-precision parts that are integral to various industries, from automotive and aerospace to consumer electronics and medical tools. Its strength lies in producing durable components with intricate details and uniform surface finishes.
Experience shows that quality in die casting starts with selecting the right alloy. Aluminum, zinc, and magnesium alloys are popular choices, each offering different strengths, weight characteristics, and price points. Aluminum is prized for its lightweight and corrosion resistance, making it ideal for automotive and aerospace components, where strength-to-weight ratio is crucial. Zinc alloys, known for their strength and dimensional stability, are excellent for intricate parts such as gears and housings, commonly found in consumer electronics. Magnesium, the lightest structural metal, excels in applications requiring superb strength and electromagnetic interference shielding, useful in medical devices and electronic housings.
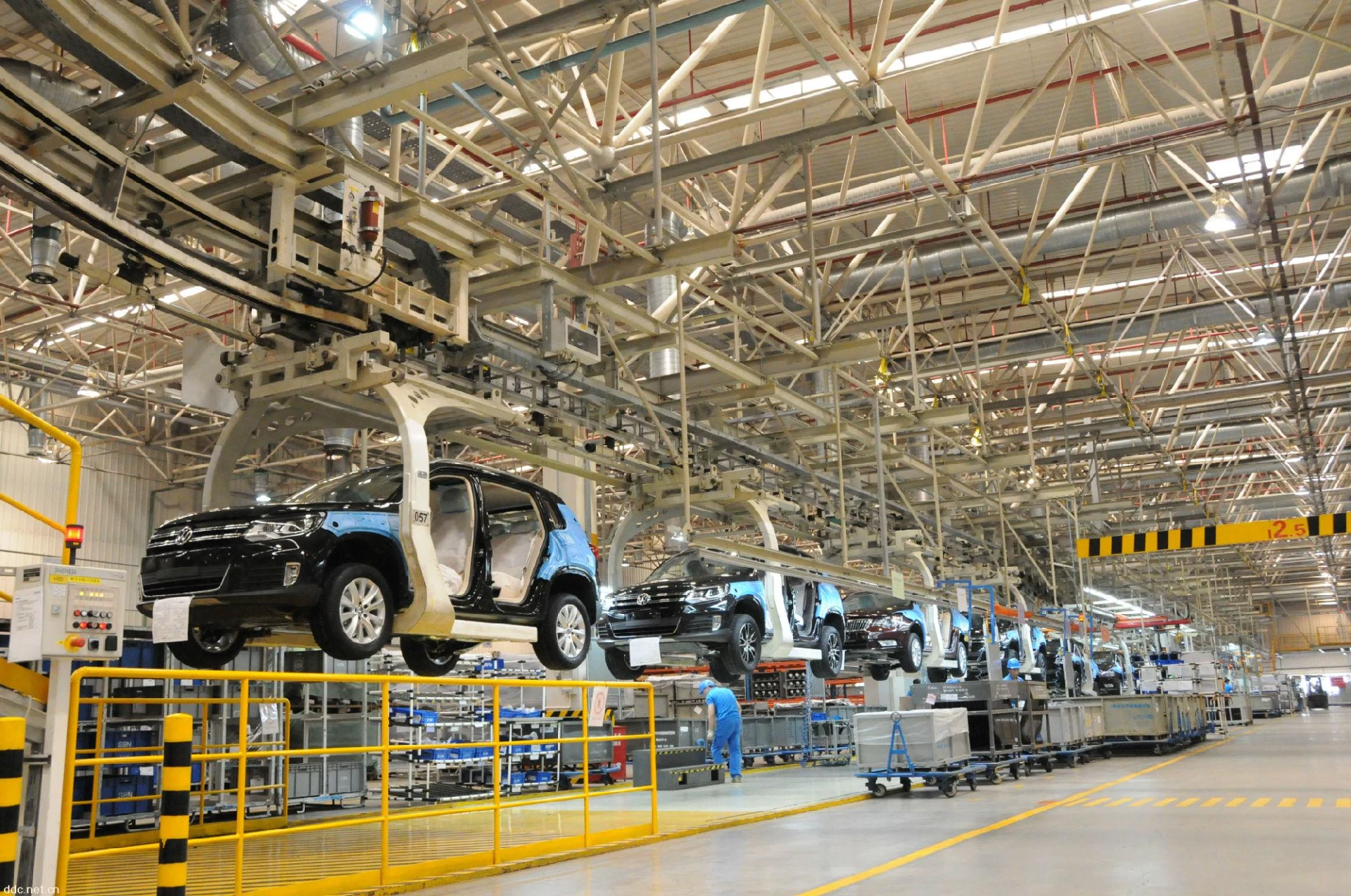
Professional expertise involves not only selecting materials but also designing molds that minimize waste and optimize the quality of the final product. The mold, typically made of tool steel, undergoes meticulous design and testing to ensure it can withstand repeated use while maintaining precision under extreme conditions. Subtle considerations, such as draft angles and wall thickness, require expert knowledge to avoid defects like porosity or improper fills. These factors are crucial when molding components with complex geometries.
Once the mold design is set, the die casting process leverages advanced machinery to achieve precision and consistency. High-pressure die casting, for example, pushes molten metal into a mold at pressures up to 1500 bar, crafting parts with exceptional detail. This high-pressure method is preferred for components where surface finish and accuracy are paramount, often used in the automotive industry's lightweight components.
quality die casting
Authoritativeness in die casting processes manifests through quality control and testing, where practices align with international standards like ISO 90012015 and IATF 16949. Rigorous testing regimes, including X-ray inspection for internal integrity, tensile and yield strength tests, and spectroscopic analysis for alloy composition, form the backbone of quality assurance. Companies that underscore their certification in these areas project a strong authority, reassuring clients of their adherence to quality benchmarks.
Trustworthiness in the die casting sector is built not only on technical capabilities but also on customer-centric practices. Transparency in the supply chain, from sourcing raw materials to post-production delivery, is essential. Traceability of each component fosters accountability and builds client trust, particularly in industries where part failure could result in significant risks. Its importance cannot be overstated in the context of automotive and aerospace industries, where component failure could lead to catastrophic outcomes.
Moreover, innovative practices such as just-in-time manufacturing and lean production not only optimize efficiencies but also align deliveries with demand, reducing excess inventories and production waste. These measures ensure that manufacturers not only maintain a competitive edge but also uphold environmental responsibilities, further enhancing customer trust.
Ultimately, the quest for quality die casting is a symbiotic blend of advancing technology, adhering to stringent quality controls, and ensuring sustainability. As the market's focus tilts towards electric vehicles and sustainable technologies, manufacturers must keep pace through continuous improvements, adapting processes to meet emerging demands and regulatory norms.
In conclusion, the evolving landscape of quality die casting demands a robust integration of experience, expertise, authoritativeness, and trustworthiness. Empowered by these principles, manufacturers stand well-equipped to meet today's challenges, producing components that are not only functional and reliable but also adapt to the ever-changing demands of global industries. Through strategic material selection, precise engineering, and credible quality assurance practices, quality die casting will continue to play an essential role in the ongoing evolution of modern manufacturing.