Sand casting, an age-old technique, stands as one of the quintessential methods in the production of metallic components, which finds extensive applications across various industries. Its beauty lies in its simplicity and adaptability, allowing for the creation of both complex shapes and large structures. At its core, sand casting involves creating a mold from a sand mixture and pouring molten metal into it, solidifying into the desired shape as it cools. This process, despite being a traditional one, has seen significant enhancements through technological advancements, making it even more relevant in today's manufacturing landscape.
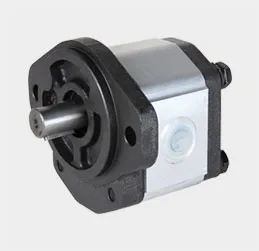
One notable advantage of sand casting is its cost-effectiveness, especially for large-scale production. The materials required, primarily sand, are abundantly available and inexpensive. This affordability extends to the reusable nature of the sand mold, offering manufacturers a cost-efficient method of prototyping new designs quickly without incurring excessive overheads. The ability to produce a wide range of products, from automotive parts to artistic sculptures, underscores its versatility. The automotive industry, in particular, benefits immensely from sand casting, enabling the production of engine blocks and transmission housings with a balance of speed, precision, and durability.
Moreover, sand casting is indispensable in crafting custom-designed components that demand unique properties. Manufacturers leverage this technique to produce items such as pump housings and valves where specific material compositions and intricate geometries are critical. The flexibility of sand casting makes it easier to adjust the mold’s design or incorporate different metal alloys, tailoring the end product to meet the exact requirements of different applications.
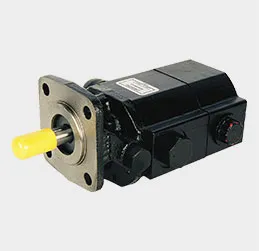
In sectors like aerospace and defense, where precision and reliability are paramount, sand casting holds a prestigious position. The ability to produce robust and high-performance components while maintaining stringent quality standards is a testament to its reliability. This is particularly significant given the operational demands of aerospace components, where failure is not an option. Sand casting's adaptability allows engineers to experiment with innovative materials that enhance performance while reducing weight, a crucial factor in these high-stakes industries.
products made from sand casting
Despite its many advantages, no process is without limitations. Sand casting's surface finish and dimensional accuracy can sometimes fall short compared to more modern techniques like die casting or investment casting. However, strategic post-processing methods and the relentless pursuit of process optimization have mitigated these shortcomings to a large extent. Techniques such as machining or grinding can refine the surface finish and precision of the cast components, thus bridging the gap between traditional craftsmanship and modern-day quality expectations.
The future of sand casting is not just limited to industrial components. Environmental considerations are steering industries towards more sustainable and eco-friendly manufacturing processes. Sand casting is primed to evolve in this direction with innovations such as using biodegradable binders and incorporating recycled metals, significantly reducing its environmental footprint. These advances not only align with global sustainability goals but also ensure that sand casting remains a relevant and competitive manufacturing process in a rapidly changing world.
From a structural standpoint, sand cast products have strong mechanical properties, suitable for applications requiring high tensile strength. This makes them ideal for constructing buildings and bridges, where large-scale support structures are indispensable. The construction industry benefits from sand casting’s ability to produce components that stand the test of time, both structurally and aesthetically.
In conclusion, the art and science of sand casting balance tradition with innovation, offering a robust solution for various industrial applications. Its enduring presence in the modern industrial landscape is a testament to its effectiveness and adaptability. By embracing technological advancements and sustainable practices, sand casting continues to forge a path forward, meeting the ever-evolving needs of industries while maintaining a commitment to quality and versatility. As manufacturers look to the future, sand casting will undoubtedly remain a cornerstone of industrial production, marrying the principles of ancient craftsmanship with the demands of contemporary manufacturing.