Technical Specifications of Green Sand for Casting
Parameter | Typical Value | Industrial Standard | Impact on Casting Quality |
---|---|---|---|
Clay Content (%) | 8-12% | AFS 22-32 | Determines mold strength & collapsibility |
Water Content (%) | 2.5-4.5% | AFS 26-36 | Affects permeability & compactibility |
Permeability Number | 60-140 | AFS 50-150 | Gas escape capability during pouring |
Compression Strength (kPa) | 130-180 | ISO 185:2005 | Mold resistance to deformation |
Grain Fineness Number | 50-70 | AFS 45-85 | Surface finish quality |
Source: American Foundry Society (AFS) Standards for Mold & Core Materials
Performance Analysis of Green Sand Systems
Optimizing Production with green sand for metal casting
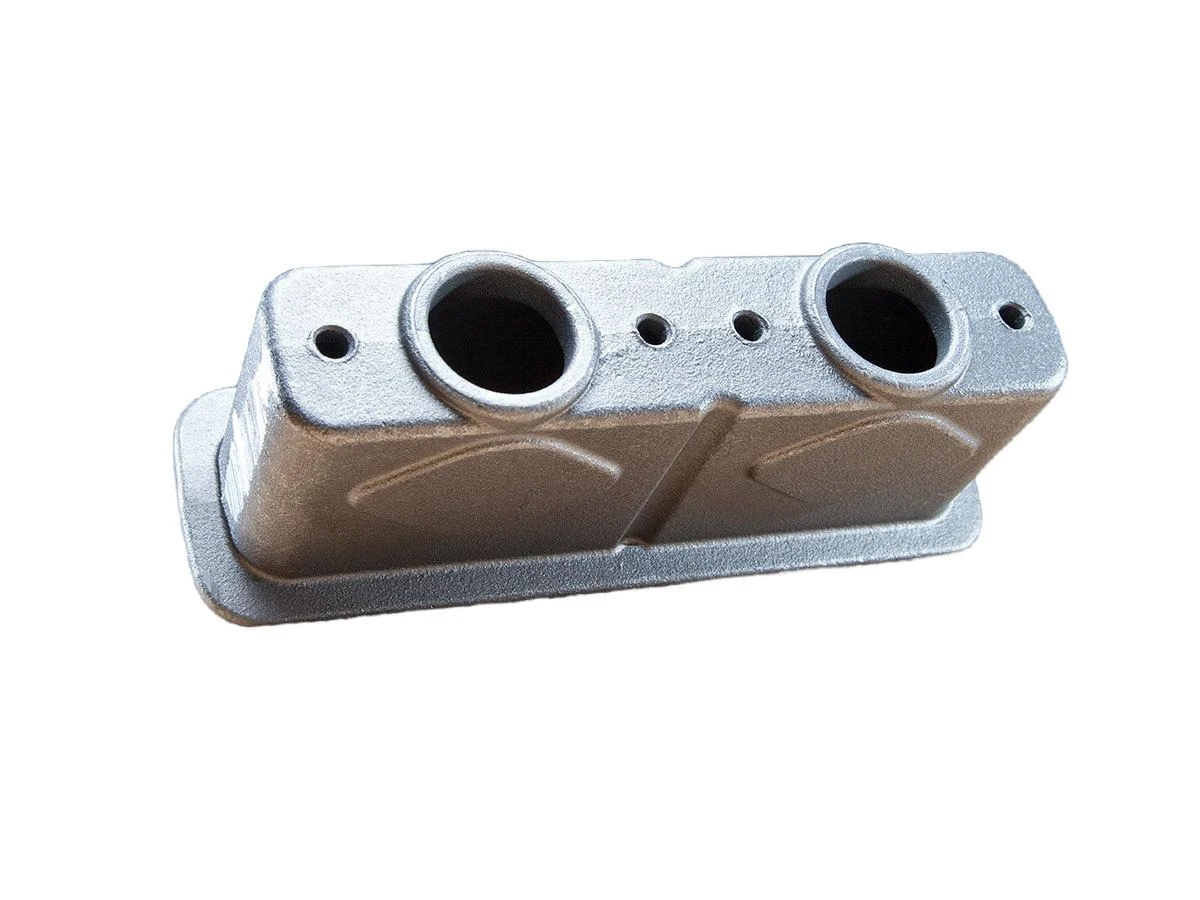
OEM Cylinder Head Cover
Precision-engineered using advanced green sand metal casting techniques for superior dimensional accuracy and surface integrity in automotive applications.
Material Composition: Foundry sand, molding sand binder, siliceous sand, silica sand, zircon sand, chromite sand, corundum sand, special sand.
Customization: Unit weight and dimensional specifications based on customer requirements
View Product Detailsgreen sand vs dry sand casting: Technical Comparison
Green Sand Casting
- Sand mixture contains 5-10% water
- Mold prepared in moist condition
- Lower production costs
- Faster production cycles
- Higher dimensional accuracy (CT6-CT8)
- Optimal for medium/high volume production
Dry Sand Casting
- Sand baked at 200-350°C for 2-8 hours
- Mold prepared in dry condition
- Higher tooling costs
- Longer production cycles
- Superior surface finish (Ra 6.3-12.5μm)
- Recommended for intricate geometries
Modern foundries increasingly adopt hybrid approaches where green sand casting handles primary molding and dry sand cores provide critical internal features – significantly enhancing both production economy and dimensional precision.
Industrial Applications of green casting sand
Automotive Sector
Engine blocks, cylinder heads, transmission cases where green sand for casting provides optimal cost-to-performance ratio for high-volume production
Heavy Machinery
Pump housings, hydraulic valves, gearboxes requiring high structural integrity with weights ranging 20-2000 kg
Energy Industry
Turbine casings, wind energy components where material consistency ensures pressure containment capabilities
Foundry Expert FAQ: Green Sand Casting
Q: What determines clay selection in green sand mixtures?
A: Bentonite clay (sodium/calcium) is selected based on required bonding strength. Southern bentonites provide higher hot strength (>180 kPa) while Western bentonites offer better flowability.
Q: How does grain distribution impact mold quality?
A: Optimal GFN (Grain Fineness Number) between 55-70 ensures smooth surface finish (Ra 12.5-25μm) while maintaining adequate permeability (>100)
Q: What additives improve casting surface finish?
A: Coal dust (3-5%) reduces metal penetration while wood flour (0.5-1%) improves collapsibility. New cellulose additives provide eco-friendly alternatives.
Q: How does compression strength affect casting integrity?
A: Maintaining 140-160 kPa compression minimizes mold wall movement during solidification, critical for dimensional accuracy (±0.5% tolerance).
Q: What water/clay ratio optimization is recommended?
A: The ideal water-to-clay ratio is 0.25-0.35 for Western bentonite and 0.35-0.45 for Southern bentonite systems as per AFS research.
Q: How are modern sand testing systems implemented?
A: Advanced foundries employ real-time LOI (Loss on Ignition) monitors and compactibility controllers that automatically adjust water additions within ±0.2% accuracy.
Q: What safety standards apply to green sand metal casting operations?
A: OSHA 1910.252 regulates silica exposure while ISO 14001 governs environmental compliance. Modern binder systems reduce free silica below 0.1%.