Precision lost wax investment casting stands as a cornerstone in modern manufacturing, offering unmatched capabilities in producing complex metal parts with exceptional accuracy and surface finish. For centuries, this manufacturing process has been revered for its ability to create intricate designs that would otherwise be challenging to achieve with other methods. The process begins with creating a wax model of the desired part, which is then coated with a refractory ceramic material. Once set, the wax is melted away, leaving a precise mold for casting metal components.
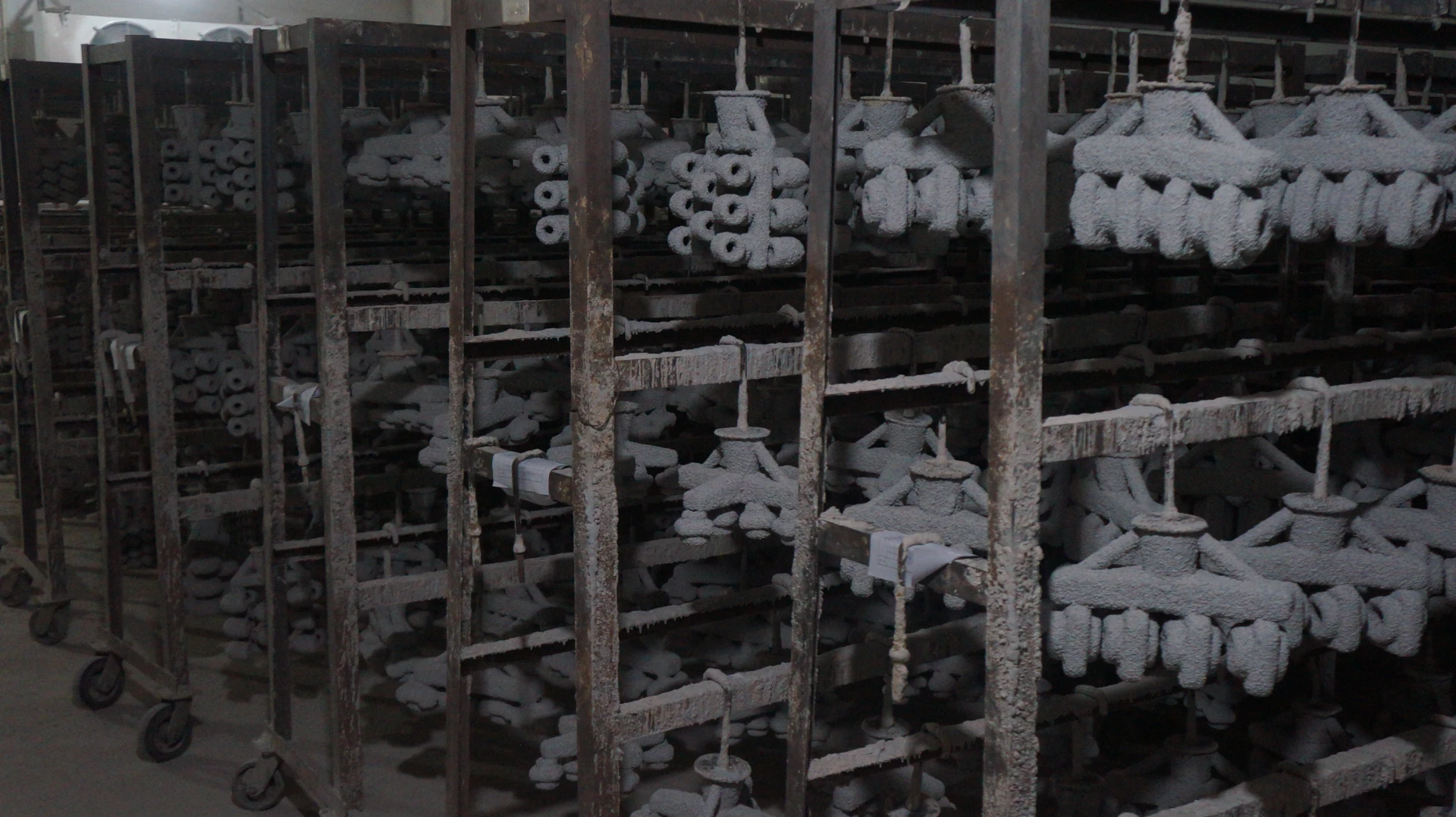
Businesses engaged in production understand that having an optimal manufacturing process is crucial for maintaining competitive advantages.
Precision lost wax investment casting offers several benefits, particularly for industries requiring high-detail and precision components. The aerospace, automotive, dental, and jewelry industries heavily rely on this method for producing parts that meet stringent quality standards.
Experience in utilizing this casting method reveals distinct advantages. Due to its ability to produce near-net shapes, manufacturers can significantly reduce post-processing time, which leads to cost efficiency and faster time-to-market. This efficiency is particularly critical in sectors where responsiveness to market changes can define competitive success or failure. Moreover, the surface finish acquired through precision lost wax casting minimizes the need for additional machining, providing further cost benefits.
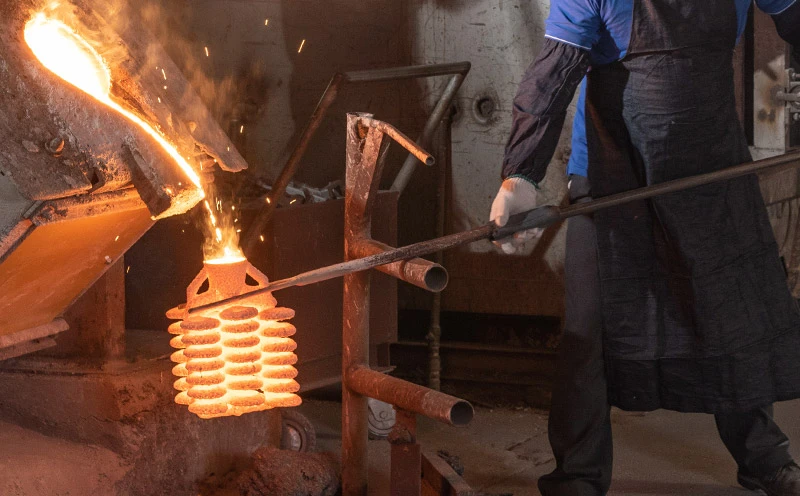
From an expertise standpoint, professionals in the field recognize that precision lost wax investment casting is uniquely suited to materials that are difficult to machine or handle by other methods. The capability to use a vast array of alloys—including steel, nickel, titanium, and aluminum—opens a plethora of possibilities for design engineers. This flexibility often translates into products that are lighter, stronger, and more sustainable due to less wastage in production.
In terms of authoritativeness, precision lost wax casting is supported by a legacy of successful applications and continual innovations. Industry leaders such as Rolls-Royce and General Electric have employed this technology for manufacturing critical components in gas turbine engines, highlighting its trustworthiness and reliability in high-stakes applications. Their standardization and fine-tuning of processes are a testament to the process's potential for bringing ideas to life with pinpoint accuracy.
precision lost wax investment casting
For businesses considering adopting precision lost wax investment casting, an important consideration is the provider’s reputation and technological capability. It is essential to partner with a casting provider who has a proven track record and in-depth understanding of the materials and methodologies involved. Consultations with expert foundries can assist manufacturers in optimizing designs for casting, ensuring that the final products not only meet—but exceed—required specifications.
Trustworthiness is further established by adhering to recognized quality management systems such as ISO 9001 and AS9100, which many precision casting companies achieve and maintain. These certifications provide assurance that the processes are controlled and consistent, reducing the risk of defects and maintaining product integrity.
With the global push towards sustainability, precision lost wax investment casting aligns seamlessly with eco-conscious manufacturing goals. By reducing waste and energy consumption during production, this method supports companies in meeting both regulatory and consumer demands for environmentally friendly practices.
In conclusion, precision lost wax investment casting is not just a manufacturing process but a strategic tool that offers competitive edge and sustainability. It is a testament to how traditional techniques can evolve and adapt to modern needs, providing a robust solution for industries focused on precision, quality, and efficiency. Embracing this technology means embracing a future where complex designs meet practicality in the most efficient way possible.