Precision casting and investment casting are two terms often used interchangeably in the manufacturing industry, yet subtle differences exist that can significantly impact the choice for a given application. Knowing these distinctions and understanding the nuances can guide manufacturers to make informed decisions, ultimately affecting the integrity of the finished product and its suitability for specific applications.
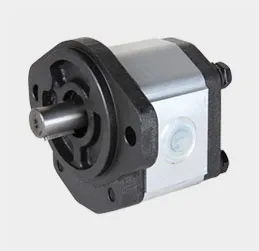
Precision casting, often recognized for its high-dimensional accuracy and exceptional surface finish, offers a manufacturing solution that minimizes material waste and post-processing efforts. This process is particularly advantageous for creating components with complex geometries and thin-walled sections. Precision casting is acclaimed in sectors where stringent dimensional specifications are mandatory, such as aerospace, medical devices, and automotive industries.
In contrast, investment casting, known for its versatility, involves creating a mold from a wax pattern that is melted away to leave a cavity. This age-old technique owes its endurance to the ability to produce intricate components with excellent detail and smooth surfaces. The flexibility in alloy choices is unrivaled, allowing for the creation of parts from ferrous to non-ferrous metals, including steel, aluminum, and bronze.
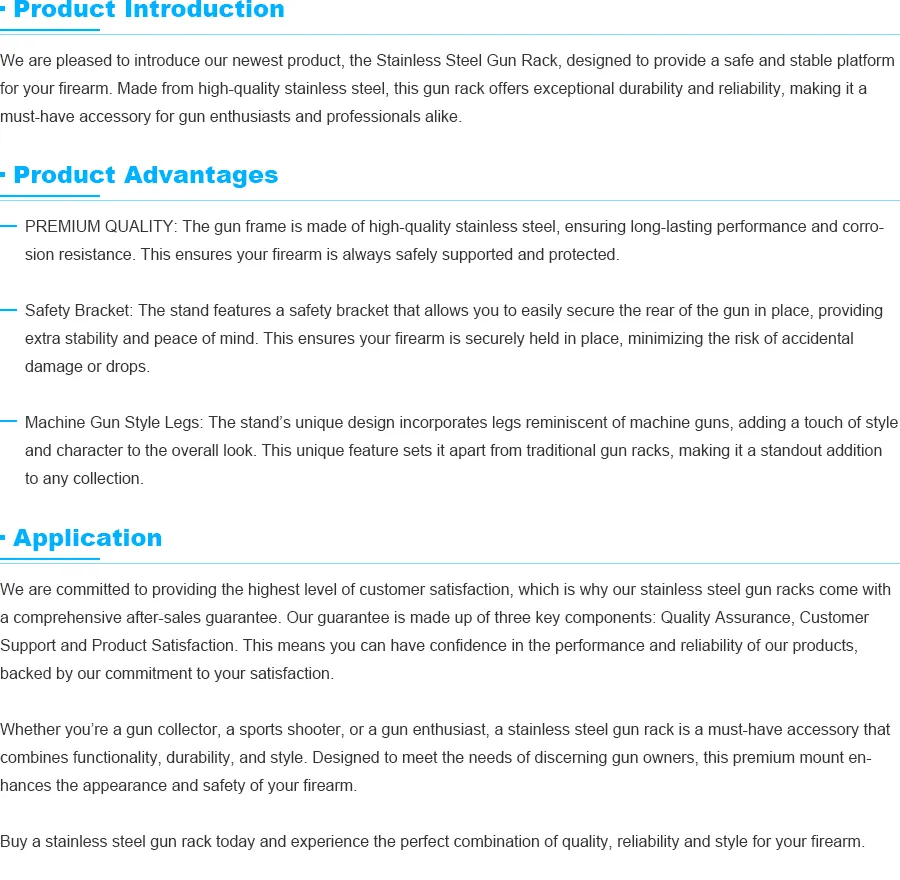
Expert insight reveals that while precision casting is a subset of investment casting, the term ‘precision’ underscores modern enhancements in the traditional investment casting process, aiming at maximizing accuracy and surface quality. Industry professionals have noted the precision aspect is critical when manufacturing parts that require little to no machining, reducing lead times and production costs.
From a practical perspective, both processes share foundational techniques but diverge when considering the specific requirements of a project. For instance, industries facing high-stress environments may prefer investment casting due to its proven reliability for high-strength alloys and heat tolerance. However, when the goal is to achieve minimal dimensional variance without extensive finishing processes, precision casting takes precedence.
precision casting vs investment casting
Moreover,
the decision between using precision casting versus investment casting often hinges on economies of scale and material costs. Precision casting, while potentially higher in upfront costs due to more stringent controls and sophisticated equipment, can yield savings over time for complex parts by reducing the need for additional machining. Investment casting provides a cost-efficient approach for large volume runs or parts where surface finish commands priority but does not require hyper-specific dimensional accuracy.
For manufacturers and engineers weighing the benefits of precision casting versus investment casting, understanding the application demands is paramount. Factors such as part size, design complexity, alloy selection, and production volume should all influence the decision-making process.
In terms of trustworthiness, choosing a reputable supplier with a proven track of successful projects in both precision and investment casting is crucial. Engaging a partner with extensive expertise ensures that product requirements align perfectly with the casting method, delivering components that meet stringent quality standards.
Decision-makers should leverage both technical expertise and practical experience, such as evaluating past case studies and customer feedback, to assess which casting process aligns with their specific needs. Whether the objective is exploiting the technological advancements in precision casting or utilizing the traditional reliability of investment casting, a thorough evaluation promises optimum results tailored to the demands of today's fast-evolving industrial landscape.