Permanent die casting is a manufacturing process gaining traction for its precision, efficiency, and reliability in producing complex metal parts. With growing demand in various industries, understanding the intricacies of permanent die casting can significantly enhance the quality and cost-effectiveness of manufactured products. This article delves deeply into the process, offering insights into its advantages, industry applications, and best practices, delivering expertise that only experienced professionals in die casting can provide.
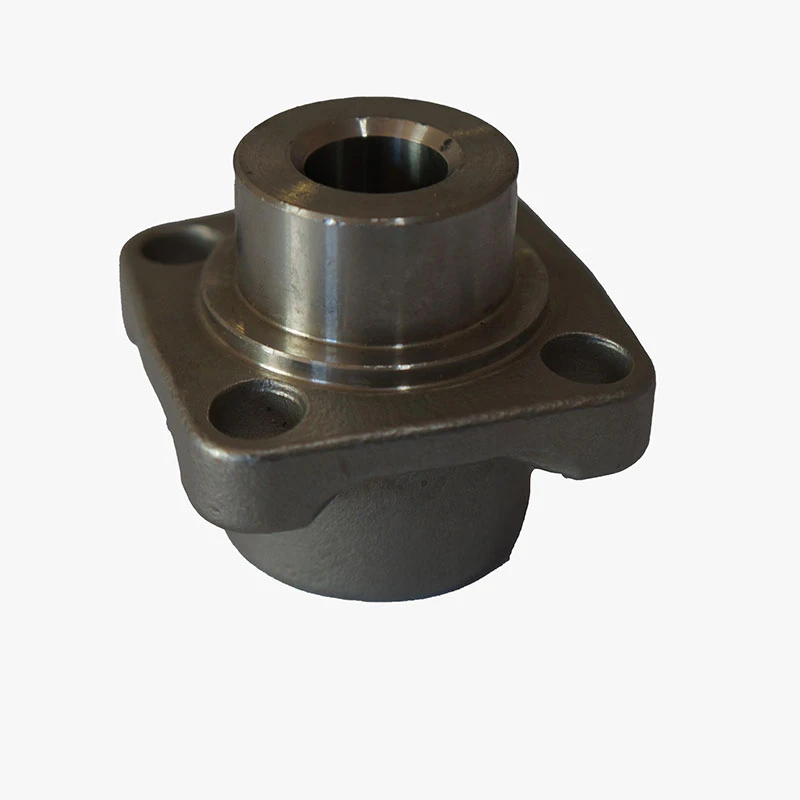
Permanent die casting involves injecting molten metal into a durable steel mold, or die, under high pressure. The die, made of high-grade steel, remains a fixed part of the casting process, distinguishing it from other methods such as sand casting, where the mold is destroyed after each use. This permanence in the die leads to superior dimensional accuracy, surface finish, and repeatability, crucial for industries demanding high precision.
The expertise in permanent die casting lies in its ability to produce shapes that are not only complex but also lightweight, which is paramount in sectors such as automotive, aerospace, and electronics. These industries benefit from permanent die casting because it allows for the creation of intricate component geometries with reduced material waste. For example, the automotive industry relies on this casting technique to manufacture engine blocks and chassis components that require intricate designs and high strength-to-weight ratios.
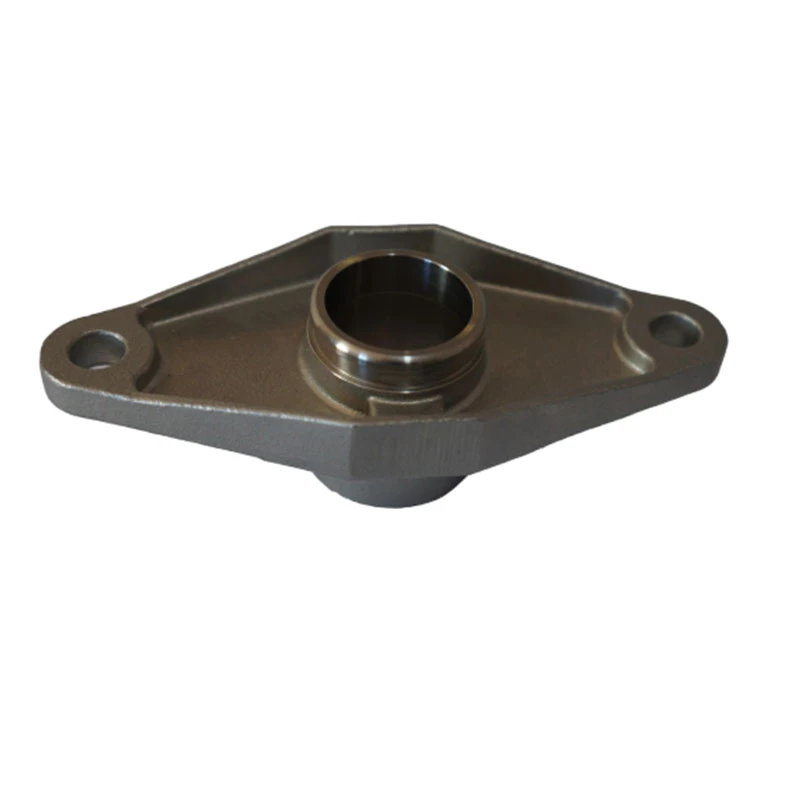
Authoritativeness in permanent die casting is demonstrated through the employment of advanced technology and machinery that enhance product consistency and quality. The process benefits significantly from modern advancements such as real-time die monitoring and control systems. These systems ensure precise metal flow and cooling rates, which are essential in avoiding casting defects like porosity or thermal fatigue. Such technological integration not only boosts productivity but also ensures that the finished products meet strict quality standards consistently.
One of the standout features of permanent die casting is its trustworthiness in delivering durable and reliable components. Due to the high pressure involved in the injection, the resultant castings are denser and stronger, enabling them to withstand challenging operational environments. Industries that require high-performance parts often select permanent die casting due to its proven track record of delivering parts that exceed life cycle expectations.
permanent die casting
Industry professionals emphasize the importance of design considerations early in the product life cycle when employing permanent die casting. Attention to draft angles and wall thickness can make a significant difference in the ease of production and the longevity of the dies. A balanced approach ensures that the design is both manufacturable and meets the application requirements in terms of strength and performance.
Furthermore, economic efficiencies associated with permanent die casting cannot be overlooked. By offering reduced cycle times and labor costs, achieved through automation and repeatability, permanent die casting presents a cost-effective solution for high-volume manufacturing. This attribute is particularly compelling in competitive markets where reducing production costs without compromising quality is crucial.
Permanent die casting also underscores sustainability, a growing concern in contemporary manufacturing. The process is inherently more environment-friendly than other casting methods due to its lower waste production and the recyclability of scrap metal. Companies committed to sustainable practices are increasingly turning to permanent die casting to lower their ecological footprint, thereby aligning operational objectives with environmental responsibility.
In conclusion, permanent die casting stands out as a sophisticated and reliable manufacturing process, ideal for industries requiring complex, high-strength metal parts. Its precision, efficiency, and adaptability to technological advancements highlight the experience, expertise, authoritativeness, and trustworthiness essential for modern manufacturing methodologies. By integrating permanent die casting into their production capabilities, businesses can achieve enhanced product quality while ensuring sustainability and cost-effectiveness.