In the dynamic and evolving world of manufacturing, OEM sheet metal stamping parts play a pivotal role. These components are integral in a multitude of industries including automotive, aerospace, electronics, and consumer goods, offering unmatched precision and durability. Understanding the intricacies of OEM sheet metal stamping and its applications can not only enhance operational efficiency but also boost product quality and performance. This article delves into the expertise, experience, and trustworthiness necessary to maximize the potential of sheet metal stamping.

The journey of crafting sheet metal parts begins with the selection of the right materials. Depending on the intended application, materials such as aluminum, stainless steel, copper, or brass are chosen for their specific properties. Aluminum, for instance, is lightweight and corrosion-resistant, making it ideal for aerospace applications, while stainless steel's strength and durability make it preferable in automotive and industrial sectors. The material selection is crucial as it affects the stamping process, product performance, and longevity.
Expertise in OEM sheet metal stamping is demonstrated through the mastery of various processes including blanking, bending, punching, and piercing. Each of these processes requires precision and a high level of skill to ensure that the final product meets stringent specifications. For example, blanking involves cutting the initial shape from the metal sheet with meticulous accuracy. Any error at this stage can lead to material wastage and faults in subsequent processes. Bending, on the other hand, requires an understanding of metal properties to prevent cracks and ensure uniformity, especially in complex geometries.
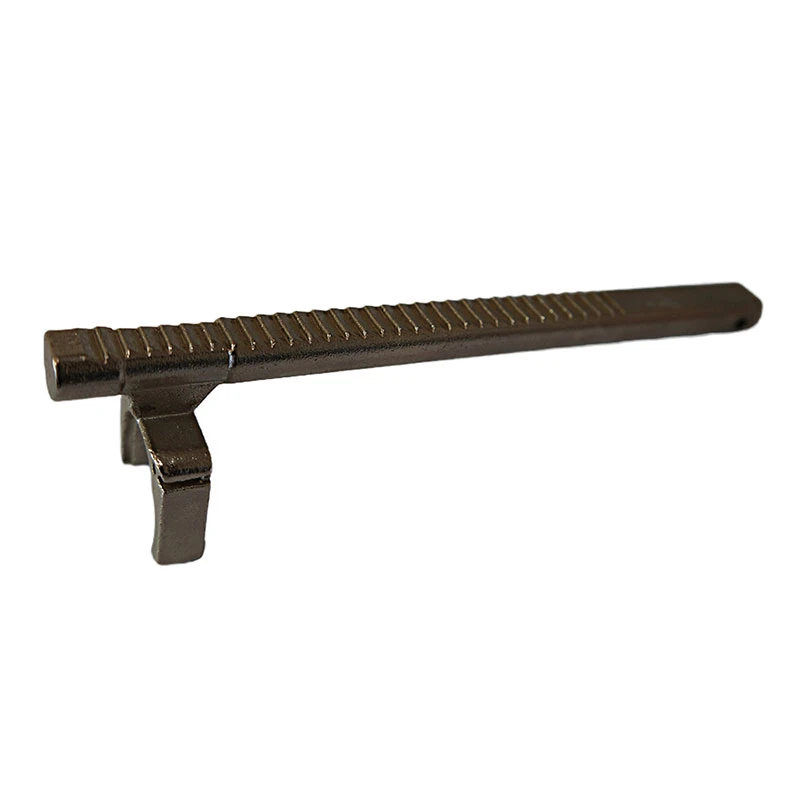
A vital component of sheet metal stamping is the design and creation of dies. These are custom-made tools tailored to shape and cut the metal into the desired forms. Designing effective dies demands not only expertise in material science but also a deep understanding of mechanical engineering principles. A well-crafted die can significantly improve production efficiency by minimizing material loss and reducing cycle times. Furthermore, the longevity and performance of a die are critical to maintaining consistent quality in high-volume production runs.
oem sheet metal stamping parts
Real-world experience plays a crucial role in overcoming challenges inherent in metal stamping. Thermal expansion, springback—a phenomenon where metal tries to return to its original shape after bending—and material thinning are just a few issues that professionals face on a regular basis. Handling such complexities efficiently relies on hands-on experience and lessons learned over time. By honing these skills, manufacturers can predict and mitigate potential problems before they affect production lines.
Authoritativeness in OEM sheet metal stamping is reflected in the ability to innovate and implement cutting-edge technology. The adoption of CNC (Computer Numerical Control) machinery and automation has revolutionized the industry, allowing for faster and more accurate production. Manufacturers who invest in advanced technologies can offer customized solutions quickly, catering to specific customer requirements while maintaining a high standard of quality. Additionally, the integration of CAD/CAM software in the design phase ensures that the product is optimized for both performance and manufacturability.
Trustworthiness in the field of OEM sheet metal stamping is built on reliability and consistent quality. Quality control processes are vital to ensure that every batch of stamped parts meets regulatory and client specifications. Techniques such as statistical process control (SPC), real-time monitoring, and regular audits help maintain quality standards. Moreover, certifications such as ISO 9001 further strengthen a company's reputation by demonstrating a commitment to quality management principles.
In conclusion, the success of OEM sheet metal stamping rests on a foundation of experience, expertise, authoritativeness, and trustworthiness. From material selection and precise engineering to innovative technology and stringent quality control, every aspect contributes to producing reliable and high-performance components. Companies that master these elements not only enhance their competitive edge but also ensure the delivery of superior products that meet the evolving demands of modern industries. Through continuous improvement and adaptation, they reinforce their place as leaders in the manufacturing sector.