Die casting automotive parts is a pivotal component in the modern manufacturing of vehicles, offering a unique blend of precision, durability, and cost-effectiveness. This advanced metal casting process has revolutionized the production of automotive components, enabling manufacturers to meet the high demands of today's automotive market.
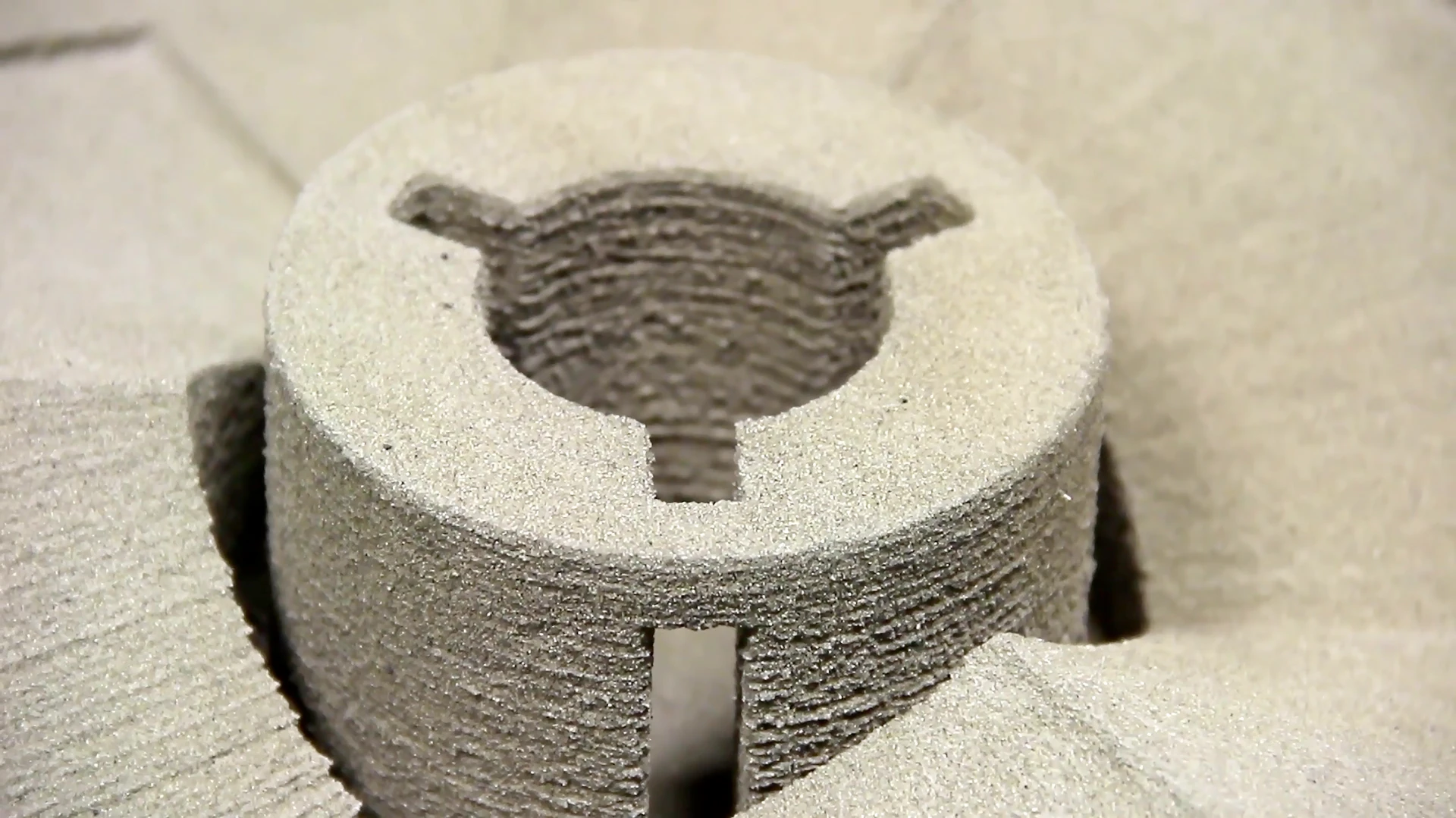
Experience in the die casting industry reveals a significant evolution from traditional manufacturing methods. As technology has advanced, so has the capability to produce complex shapes with tighter tolerances and superior surface finishes. This process is particularly valuable in the automotive sector, where precision and efficiency are crucial for both performance and safety.
Die casting consists of injecting molten metal into a mold under high pressure, a process that offers significant benefits for automotive parts. One of the primary advantages is the ability to produce lightweight yet robust components. Aluminum and magnesium, for instance, are commonly used materials in die casting that contribute to the reduction of vehicle weight. This reduction improves fuel efficiency and lowers emissions, aligning with the global push towards sustainable automotive solutions.
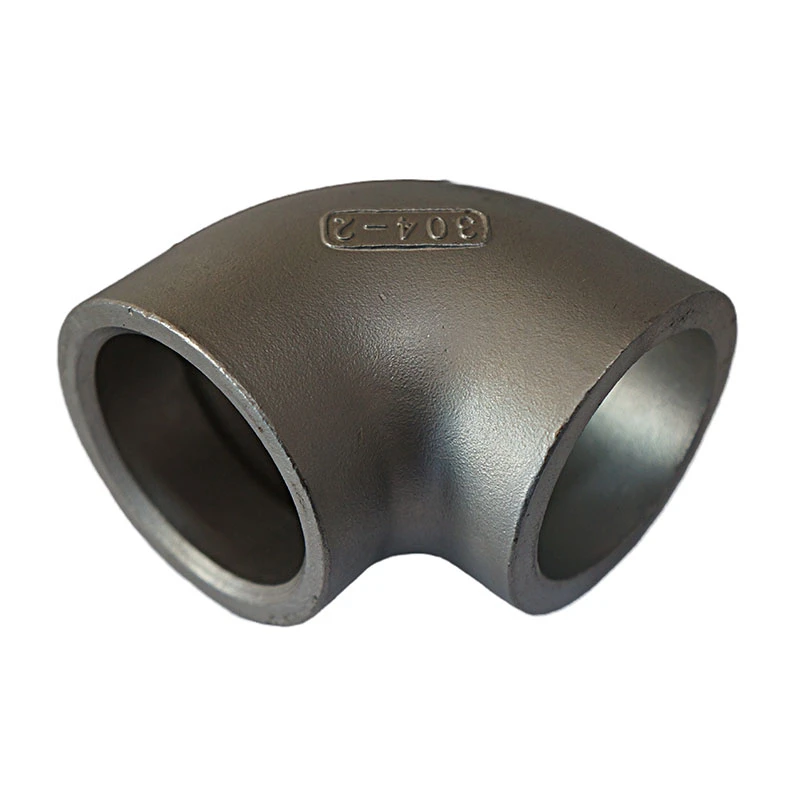
In terms of expertise,
understanding the intricacies of die casting is essential for producing high-quality automotive parts. The process involves several critical stages including mold design, metal melting, and part cooling, all of which require precise control to ensure part integrity and consistency. Advanced simulation tools are often employed to predict potential issues and optimize the die casting process. This expertise enables the production of parts such as engine blocks, transmission cases, and structural components that meet stringent automotive industry standards.
die casting automotive parts
Authoritativeness in the realm of die casting is often demonstrated through industry standards and certifications. Reputable manufacturers adhere to guidelines such as the ISO/TS 16949, which specifies quality management systems for automotive production and relevant services. These standards not only assure quality and reliability but also instill confidence in the clients and end-users who depend on these parts for critical automotive applications.
Trustworthiness in the die casting industry is built on a foundation of rigorous testing and quality assurance. Each automotive part undergoes extensive testing to verify its mechanical properties, dimensional accuracy, and thermal performance. Non-destructive testing methods, such as X-ray inspection, ensure the structural integrity of die-cast parts without causing damage. This commitment to quality assurance underscores the reliability of die casting in producing automotive components that consumers can trust.
In conclusion, die casting automotive parts combines experience, expertise, authoritativeness, and trustworthiness to elevate the manufacturing standards within the automotive industry. This advanced manufacturing process not only meets the demands for precision and durability but also drives the industry towards more sustainable practices. By embracing innovation and adhering to high-quality standards, die casting continues to play an essential role in shaping the future of automotive manufacturing, delivering parts that perform reliably while meeting the evolving expectations for efficiency and environmental responsibility.