Die casting stands as a cornerstone in the manufacturing industry, offering rapid production and high-quality outputs. However, die casting defects remain a critical concern. Addressing these defects requires not just understanding their nature but also implementing effective solutions drawn from practical experience and backed by technical expertise.
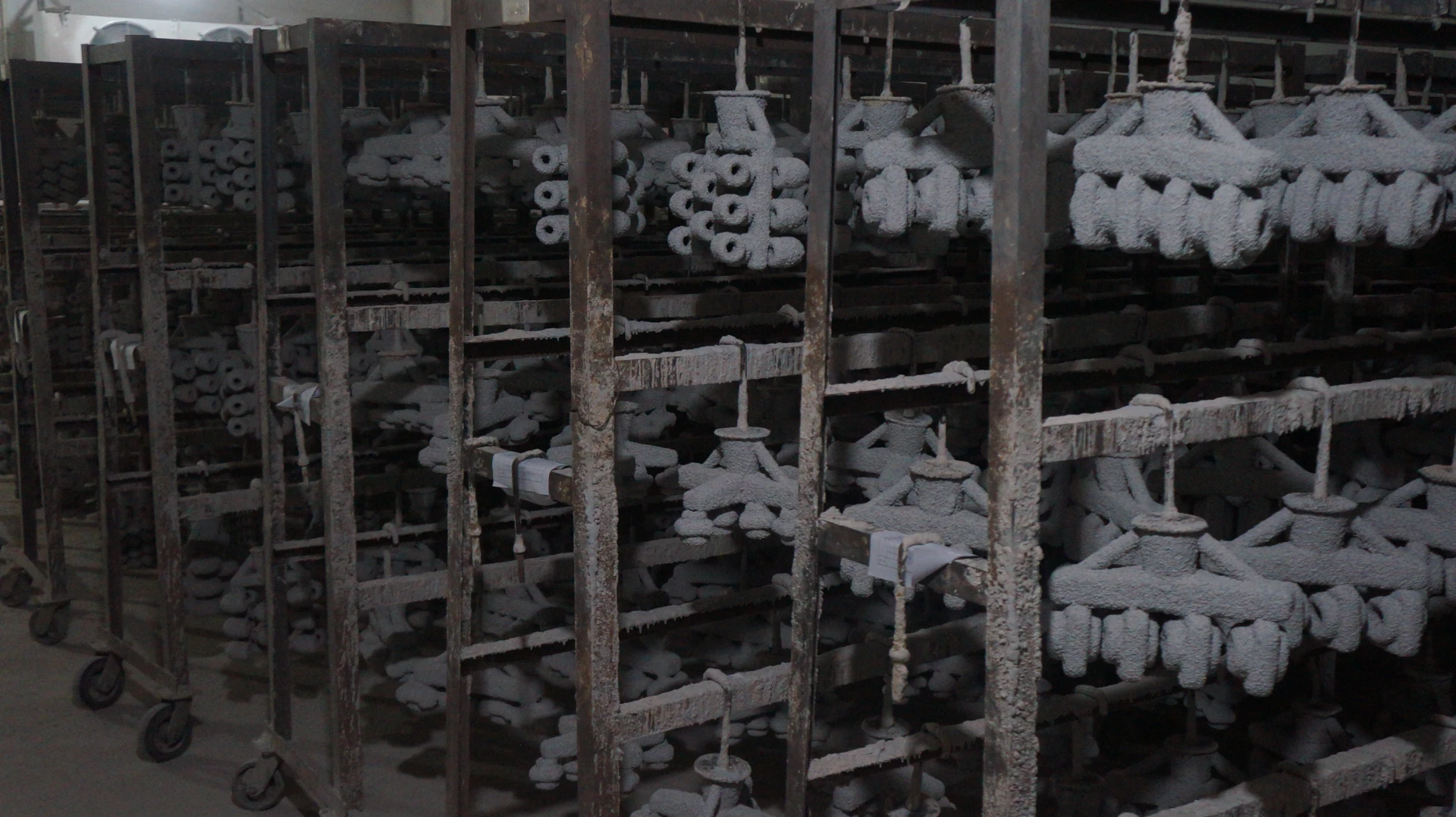
In the realm of die casting, one encounters defects such as porosity, cold shuts, misruns, and shrinkage defects, each presenting unique challenges. Porosity, for instance,
manifests as tiny voids within the casting, leading to structural weaknesses. This defect primarily arises due to inadequate cooling or excessive gas entrapment during the casting process. Over the years, industry experts have found that optimizing mold design and employing vacuum technology significantly reduces porosity. By ensuring a controlled atmospheric condition, gas entrapment is minimized, enhancing the integrity of the cast.
Cold shuts and misruns are defects associated with improper flow of the molten metal. These occur when the molten metal cools too rapidly, preventing it from filling the mold completely. Through years of hands-on industry experience, professionals recommend adjusting the pouring temperature and modifying the die design. Increasing the die temperature slightly can maintain the flowability of the metal, ensuring a complete fill and reducing the occurrence of cold shuts and misruns.
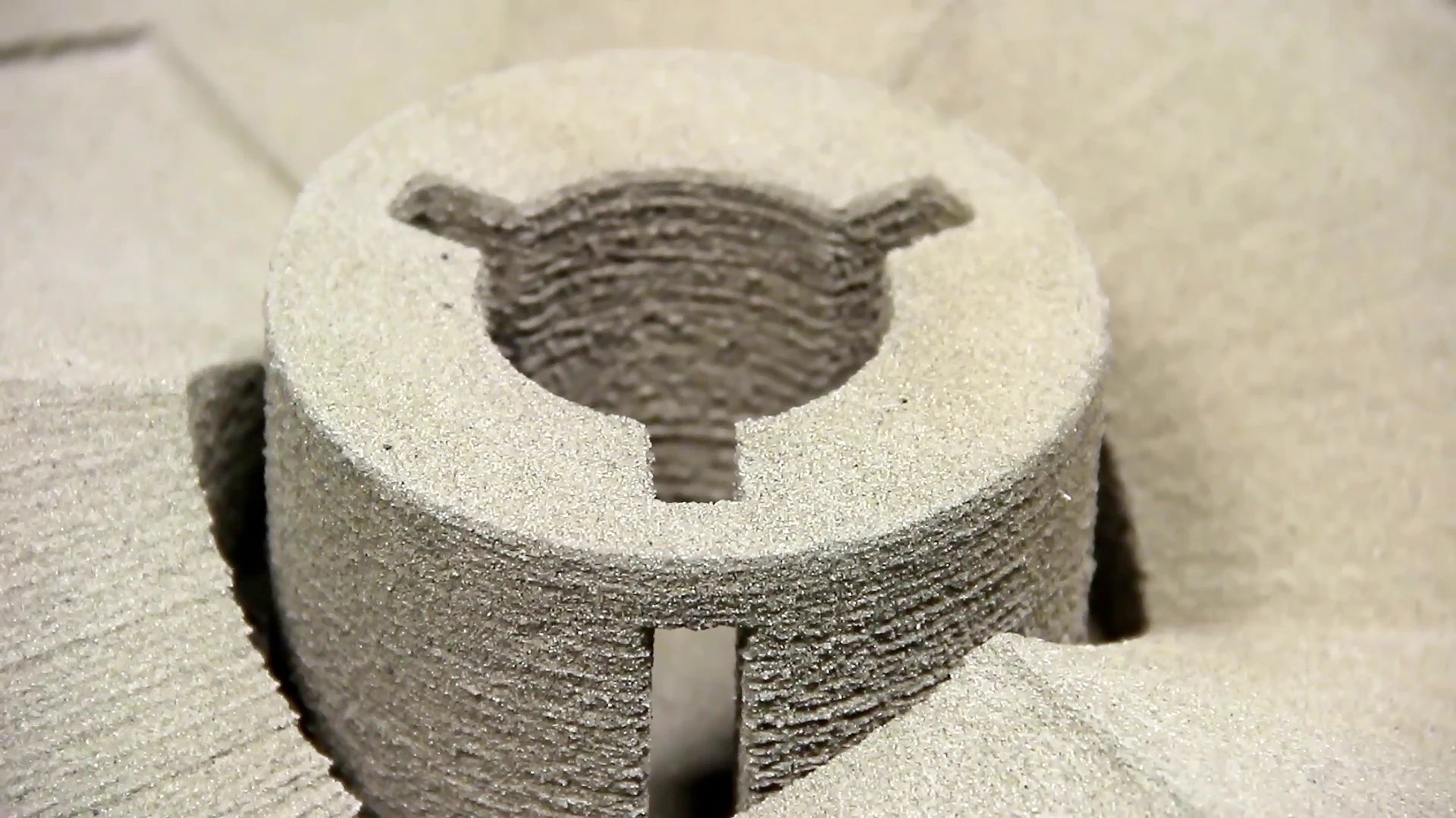
Shrinkage defects are another prevalent issue, often resulting from uneven cooling rates within the casting. This defect manifests as unsightly surface depressions or internal voids that compromise product quality. Industry veterans suggest that a balanced temperature control during the cooling phase is paramount. Employing a uniform cooling system and utilizing chill vents strategically can alleviate this problem, allowing for consistent shrinkage across the casting and reducing defects.
die casting defect
The journey towards minimizing die casting defects is ongoing, requiring a commitment to continuous learning and adaptation. Engaging with the latest technological advancements, like 3D simulation software, has proven beneficial. Such tools allow manufacturers to simulate the casting process, predicting potential defects and enabling proactive measures to prevent their occurrence. This predictive approach fosters a deeper understanding of die casting dynamics, empowering manufacturers to produce higher quality products with fewer defects.
Focus on these practices underscores the expertise and authoritativeness required in the field. Manufacturers must adopt best practices and invest in training to hone their technical skills and stay ahead of industry trends. Trustworthiness in delivering defect-free products builds customer confidence, a crucial asset in the competitive landscape of manufacturing.
In sum, addressing die casting defects requires a blend of technical knowledge and practical experience. Through ongoing education, innovative technology use, and strategic process adjustments, manufacturers can uphold product quality, establishing their authority and trustworthiness in the industry. As technology evolves, so too should the strategies employed to combat die casting defects, ensuring products meet the highest standards of quality and reliability.