OEM die casting parts are an indispensable component within numerous industries that require precision, durability, and consistency. Utilizing the OEM approach in die casting not only ensures that the parts meet specific industry standards and requirements but also offers manufacturers an edge in terms of customization and innovation.
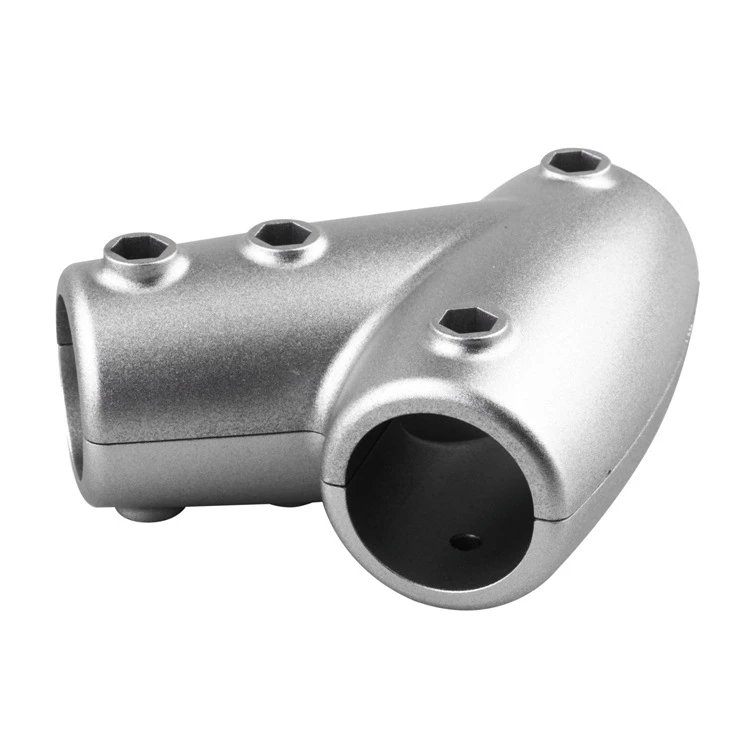
Among the reasons why OEM die casting parts stand out is their ability to be customized according to the specific needs of a company or application. Unlike off-the-shelf parts, OEM components are designed from the ground up to meet the exact specifications required by the end user. This customization capability is crucial in industries like automotive, aerospace, and electronics, where precision and adherence to tight tolerances can significantly impact performance and reliability.
One of the key advantages of using OEM die casting parts is the cost-effectiveness achieved over time. Although the initial investment may be higher compared to purchasing generic parts, the long-term benefits are substantial. Since these parts are tailor-made for their specific application, they often lead to improved performance and fewer instances of breakdowns or inefficiencies. This not only reduces maintenance costs but also minimizes downtime, thereby enhancing productivity.
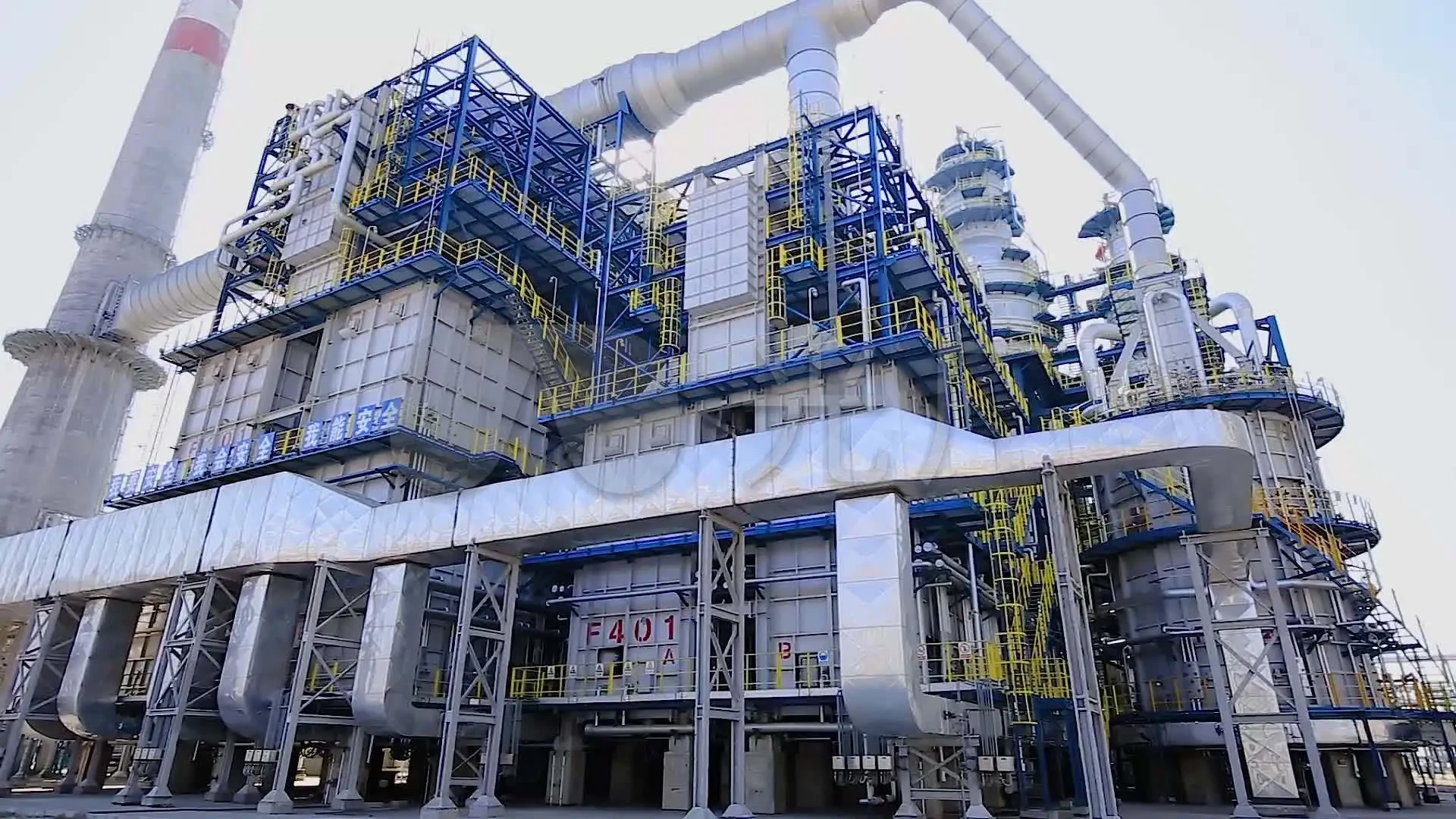
Moreover,
OEM die casting parts signify a blend of expertise and innovation. Manufacturers specializing in OEM solutions bring together years of experience and technical knowledge to deliver products that push the envelope of what's possible. Their authority in the domain is backed by an understanding of diverse materials – such as aluminum, magnesium, and zinc – that are commonly used in die casting. Knowledge of these materials and their properties is crucial, as it influences the durability, weight, and thermal resistance of the final product.
oem die casting parts
Trustworthiness in this sector is built through rigorous testing and quality assurance processes. OEM parts undergo a slew of inspections and testing before they reach the client. This level of scrutiny ensures not only compliance with international standards but also reassures customers of the durability and reliability of the parts. Manufacturers maintain transparency throughout the production process by providing detailed documentation and certifications that lend credibility and assurance to the clients.
Expertise in die casting technology also enables manufacturers to optimize designs for manufacturability without compromising on quality. By leveraging advanced computer-aided design (CAD) software and simulation tools, they can predict potential challenges and address them proactively. This proactive approach saves time and resources while ensuring that the parts meet the desired performance criteria from the outset.
Furthermore, the use of state-of-the-art machinery in OEM die casting facilities facilitates high precision and consistency in production. Modern casting technologies, such as high-pressure die casting and squeeze casting, allow for the production of complex and intricate designs that are not feasible with traditional methods. Such capabilities reduce waste and enhance the overall efficiency of the manufacturing process.
In summary, OEM die casting parts represent the pinnacle of customization, precision, and reliability. By opting for OEM solutions, businesses can enjoy long-term benefits, including reduced operational costs, improved product performance, and heightened customer satisfaction. The unmatched expertise of OEM manufacturers in material sciences and modern casting technologies further underscores their authority in the industry. Coupled with stringent quality measures and a commitment to transparency, OEM die casting parts offer unparalleled trustworthiness and are poised to meet the evolving demands of various sectors.