Metal casting sand, a critical component in the creation of high-quality cast products, remains a sought-after resource for both amateur and professional foundries. As the market for custom metal castings grows, so does the demand for premium casting sand which can significantly affect the final product's surface finish, dimensional accuracy, and overall quality.
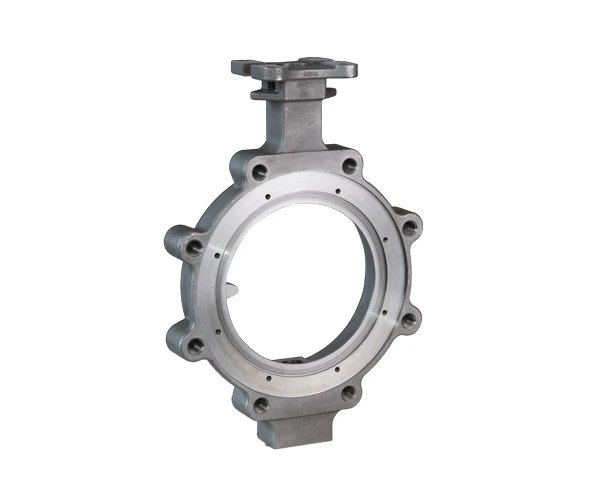
The process of metal casting requires a high degree of precision, and the choice of sand plays a vital role. Foundries often rely on different types of sand such as silica sand, olivine sand, zircon sand, or chromite sand, each having unique properties that affect melting behavior, permeability, and thermal expansion. Selecting the appropriate sand type is not only a matter of ensuring compatibility with the specific metal being cast, but also aligning with environmental and economic considerations.
One of the most popular forms of metal casting sand is green sand, a mixture of silica sand, clay, water, and other additives. Known for its strength and budget-friendly nature, green sand remains the workhorse of many foundries due to its reusability and ability to form complex molds without necessitating significant investments. Foundries opting for green sand casting enjoy benefits like rapid production turnaround and reduced labor costs, although ongoing maintenance of the sand quality is imperative for consistent results.

A significant consideration in the use of metal casting sand involves the understanding and management of defects. Issues like sand inclusions can occur, impacting the aesthetic and structural quality of the casting. Expertise in sand treatment and handling, such as controlling moisture content and compacting sand properly, can lead to high-quality results free from common defects like porosity or voids.
For foundries prioritizing precision and high-performance castings, resin sand or chemically bonded sand offers robust solutions. Despite a higher initial cost, this sand type provides superior finishes and is beneficial for producing intricate patterns and shapes with tight tolerances. It's essential for engineers and foundry managers to weigh these advantages against their budget constraints and production scale to determine the optimal sand for their needs.
metal casting sand for sale
Establishing a reliable supplier for metal casting sand is another key factor for success. An authoritative supplier offers not only quality materials but also technical support, ensuring the sand meets specific metallurgical needs. Partnering with a reputable source provides a strategic advantage, supplying consistent material without impurities that could potentially compromise casting integrity.
The environmental impact of metal casting sand must also not be overlooked. Advances in sand reclamation technology are transforming the industry, allowing for the recycling and re-use of sand, thus reducing waste and lowering costs. Foundries adopting eco-friendly practices gain a competitive edge, appealing to environmentally conscious clients and adhering to tightening regulations.
In purchasing metal casting sand, trustworthiness is achieved through transparency and a track record of reliability. Case studies or testimonials from satisfied customers serve as a testament to the supplier’s proficiency and commitment to quality. Moreover, understanding local regulations regarding the disposal and recycling of casting sand contributes to responsible operations and enhances the foundry's reputation.
In summary, metal casting sand for sale is more than just a commodity; it is a foundational element of modern metallurgy, necessitating a blend of experience, expertise, authoritative sourcing, and trustworthiness. By investing in high-caliber casting sand and fostering strong supplier relationships, foundries can achieve exceptional product quality, meet evolving market demands, and establish themselves as leaders in the metal casting industry.