Crafting high-quality metal stamping parts requires a blend of artistry and precision engineering, shaping the backbone of myriad industries worldwide. These components, often unseen, silently power the mechanisms of our everyday lives, from automotive systems to electronics. Understanding the nuances of the metal stamping process offers a glimpse into the expertise and precision required to meet the exacting standards demanded across industries.
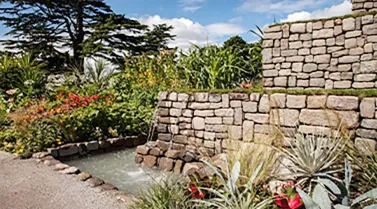
Metal stamping is not merely a manufacturing process; it is an intricate dance of physics and metallurgy. The process involves using a press to shape or cut metal by deforming it with a die. High quality in metal stamping is characterized by components that not only meet but exceed stringent industry standards, providing durability, precision, and reliability in their applications. This level of quality is achieved through a meticulous balance of technical knowledge, skilled craftsmanship, and state-of-the-art technology.
The expertise behind high-quality metal stamping parts is evident in the selection of materials. Each type of metal presents unique challenges and opportunities. For instance, working with stainless steel requires an understanding of its resilience and resistance to corrosion, which is why it’s favored in environments exposed to moisture and temperature fluctuations. Aluminum, with its lightweight properties, is indispensable in industries such as automotive and aerospace, where reducing weight without compromising strength is crucial.
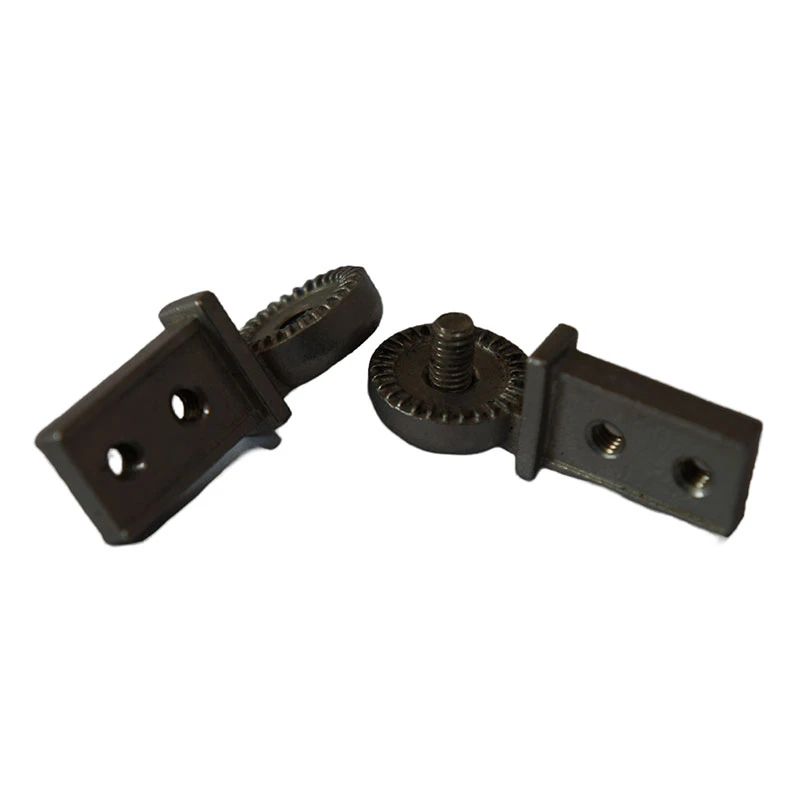
Experience plays a pivotal role in ensuring that each stamped part reaches its potential in functionality and durability. It involves the optimization of every step of the process, from prototyping and design to final production. Engineers and technicians with years of hands-on experience bring a wealth of knowledge to the table, having navigated countless challenges and intricate projects. Their insights into the thermal and mechanical properties of metals enable them to anticipate potential issues before they arise, ensuring that every component is a testament to quality.
high quality metal stamping parts
Authoritativeness in this field is often derived from continued investment in technology and a commitment to industry standards. Implementing advanced computer-aided design (CAD) systems allows for precise modeling and reduces the margin for error. Furthermore, adherence to international quality standards, such as ISO certifications, offers a mark of credibility, assuring clients that the parts will perform as expected in their intended applications.
Trustworthiness in the production of metal stamping parts is built upon a foundation of consistency and reliability. Manufacturers that prioritize quality control through rigorous inspection protocols and testing ensure that each piece is identical to the next. This consistency is crucial, particularly when components are part of safety-critical systems, such as in the medical device or aerospace industries, where failure is not an option.
The journey from raw metal to a finished, stamped component is a testament to human ingenuity and technical innovation. By continuously refining techniques and embracing new technologies, manufacturers can maintain the highest levels of quality, meeting the evolving demands of the market. As industries advance and require increasingly complex and intricate parts, the role of high-quality metal stamping only becomes more significant.
In conclusion, high-quality metal stamping parts are a cornerstone of modern manufacturing, underpinning industries that drive our economy and technology. Their production is a sophisticated process requiring a blend of experience, expertise, authority, and trustworthiness. Manufacturers who excel in this field continue to push the boundaries of what is possible, ensuring that every component not only meets but surpasses expectations, contributing to safer, more efficient, and more reliable products worldwide.