High precision casting stands as a critical process in the manufacturing industry, revered for its ability to deliver components with exceptional detail and tight tolerances. This process, also known as investment casting, wax casting, or lost-wax casting, is renowned for its capacity to produce complex shapes that would be difficult or impossible to achieve with traditional machining.

In the realm of product manufacturing, high precision casting significantly enhances quality and performance. This method is particularly beneficial for industries requiring meticulous standards, such as aerospace, automotive, medical, and industrial sectors, where durability and reliability are paramount.
Experience in high precision casting is pivotal. Craftsmen in this field understand the importance of selecting the right materials, which include alloys of aluminum, titanium, and various steels, depending on the required properties of the final product. The expertise lies in the intricate process that begins with the creation of a wax model or pattern, a skill developed through years of practice. This model is a precise replica of the desired part, and artisans must account for shrinkage and warping that might occur during the casting process.
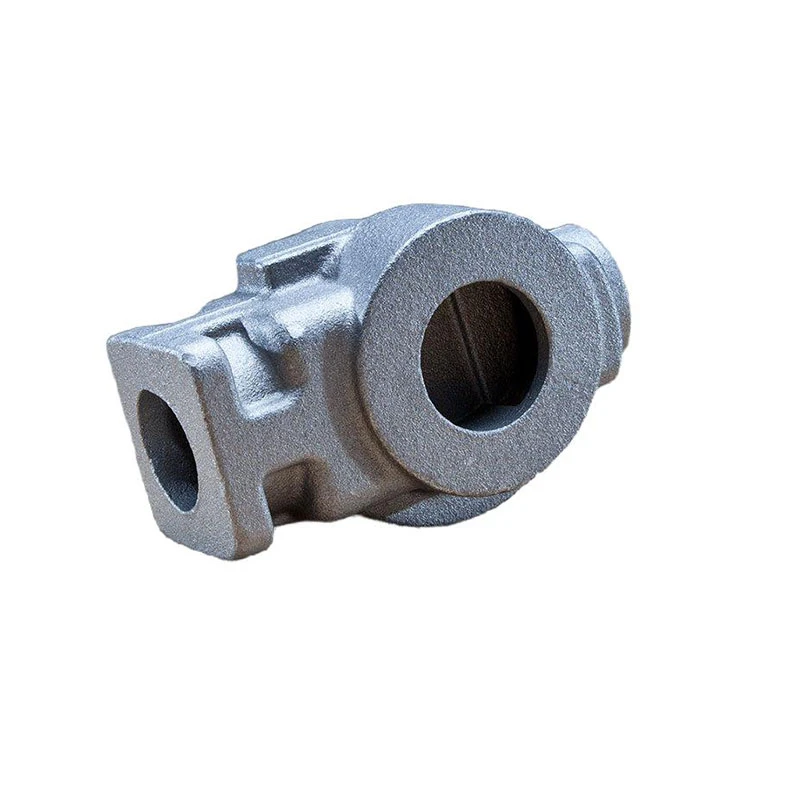
Once the wax pattern is perfected, it is invested,
hence the term investment casting. A refractory ceramic shell is built around the wax model, often involving multiple layers to ensure robustness. Here, expertise and attention to detail are crucial, as even minute imperfections in the shell can lead to defects in the final product. After the shell is formed, the wax inside is melted away, leaving a cavity in the exact shape of the intended part.
The subsequent step, pouring molten metal into the shell, must be executed with precision to avoid turbulence that could introduce air pockets or compromise the integrity of the casting. Expert casters monitor temperature rigorously, as the wrong conditions can lead to structural weaknesses or surface defects in the finished piece.
high precision casting
The expertise within this field extends to the finishing processes. Once the metal has cooled and solidified, the ceramic shell is removed, revealing a raw casting that often requires further refinement. Techniques such as grinding, machining, or surface treatment enhance the dimensions and finish of the component, bringing it up to the precise specifications necessary for its intended application.
When considering authoritativeness and trustworthiness, established manufacturers in high precision casting bring years of proven methodologies and continuous innovation to the table. Their reputation is built on a legacy of successful projects, backed by certifications and quality assurance systems that comply with international standards.
Choose a manufacturer with a robust portfolio and a history of collaboration with demanding industries. This not only ensures the reliability of the components but also reflects a commitment to maintaining cutting-edge expertise and technology. Manufacturers should foster transparency in their processes and willingly share insights into their quality control, material sourcing, and testing procedures.
For entities requiring high precision casting, engaging with service providers that prioritize these elements can significantly impact the success of their products. By delivering parts that meet stringent criteria, these companies help their clients achieve excellence in performance and safety, underscoring the credibility and reliability of their brand.
In conclusion, high precision casting is not merely about producing parts; it represents a synthesis of skill, technology, and continuous innovation. Mastery in this domain is built on a foundation of experience and expertise, where precision and attention to detail are non-negotiable. Trusting a reputable partner ensures that the components delivered will meet or surpass the expectations of quality, foster a strong reputation, and trust among end-users.