Green sand casting aluminum has emerged as a cornerstone in the realm of metal casting, celebrated for its versatility, precision, and economic efficiency. This age-old technique, which uses a mixture of sand, clay, and water to create molds, is experiencing renewed interest, particularly given the increasing demand for sustainable manufacturing practices. Let's delve deep into the intricacies of green sand casting aluminum, examining its process, benefits, and practical applications, ensuring that manufacturers and industry professionals alike can harness its full potential.
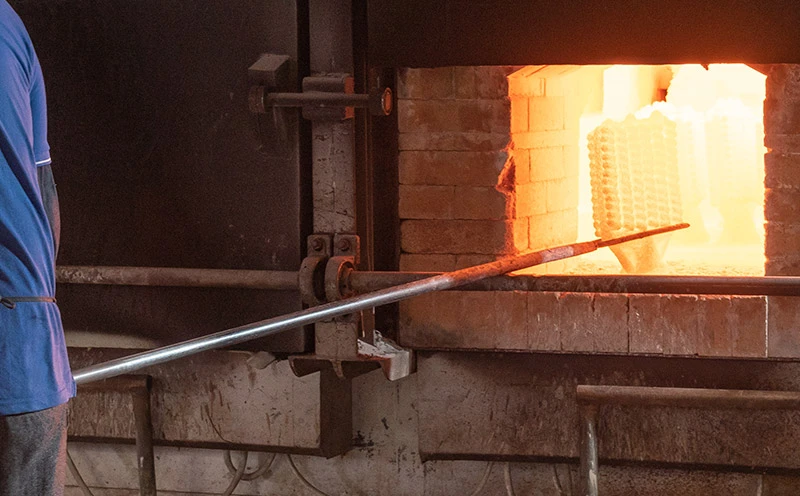
At the core of the green sand casting process is the creation of a mold from a blend of sand, clay, and water. This mixture, known as green sand, derives its name from the moisture content present when the mold is shaped. The mold's flexibility and ability to withstand high temperatures make it ideal for casting aluminum, a material prized for its lightweight and robust characteristics.
The process begins with the creation of a pattern, typically made from wood, plastic, or metal, which forms the blueprint for the final aluminum product. This pattern is then embedded in the green sand mixture, creating a cavity in the shape of the desired part. Once the mold is formed, molten aluminum is carefully poured into the cavity, filling every nook and cranny. After the metal solidifies, the mold is broken apart, revealing the cast aluminum piece, which is then subjected to post-processing techniques such as machining and finishing to achieve the final product specifications.
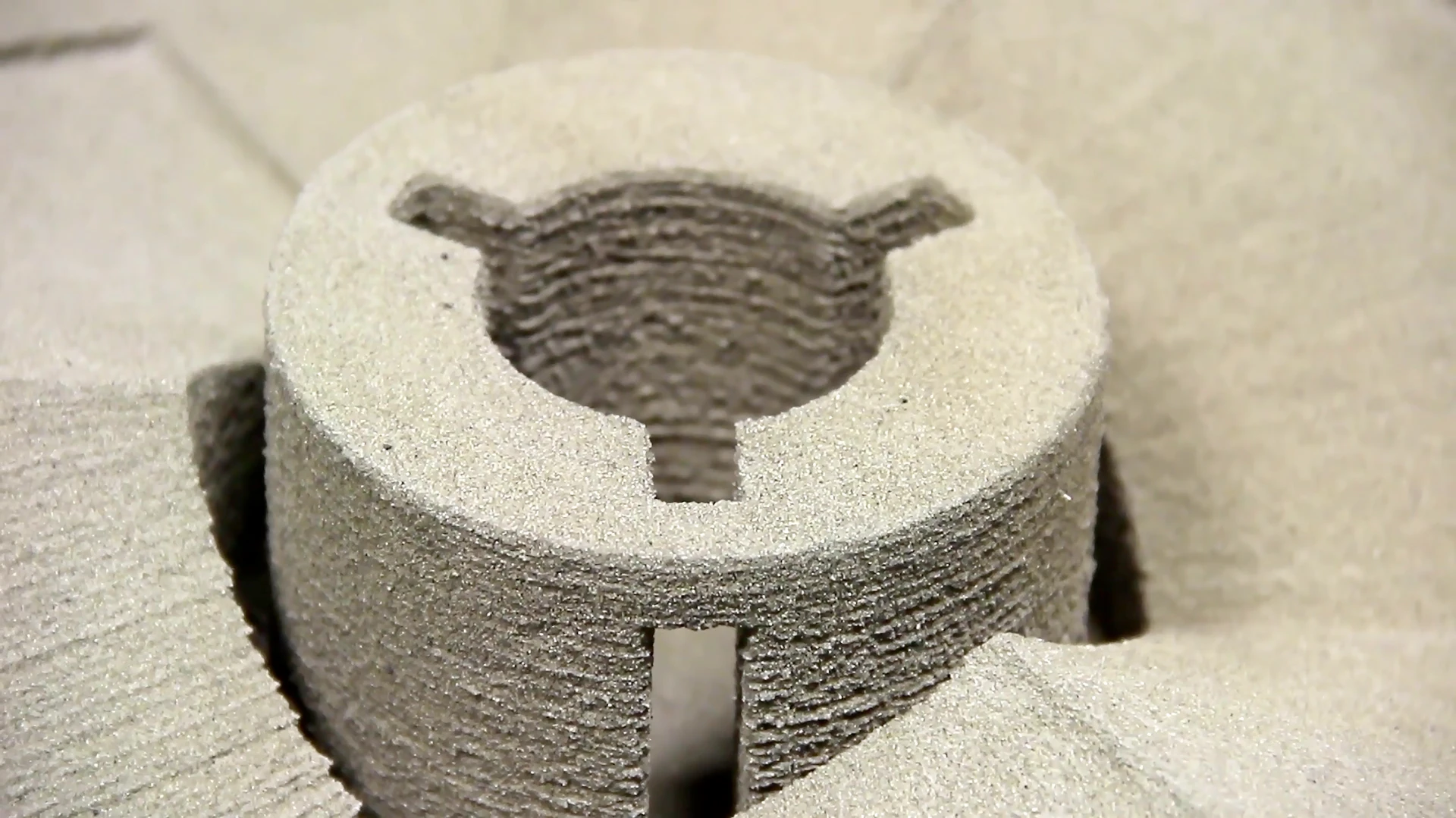
One of the most compelling advantages of green sand casting aluminum is its cost-effectiveness. The materials used in creating green sand molds are relatively inexpensive and can often be recycled or reused, reducing overall production costs. Moreover, the process is well-suited for high-volume production runs, as molds can be quickly and efficiently produced and replaced.
From an expertise standpoint, green sand casting excels in producing intricate geometries and complex shapes, which might be challenging or costly with other casting methods. The ability to fabricate intricate designs without sacrificing structural integrity is a testament to the method's capability, making it a preferred choice in industries ranging from automotive to aerospace. The automotive industry, for example, frequently utilizes green sand casting for manufacturing engine blocks and cylinder heads, harnessing both the strength and the lightweight nature of aluminum.
green sand casting aluminum
In terms of authoritativeness, green sand casting aluminum has garnered trust from numerous engineering sectors due to its proven track record and the continual advancements in casting technology. Developments such as computerized sand mixture controls and enhanced mold materials continue to refine the process, ensuring precision and uniformity in every casting cycle.
The trustworthiness of green sand casting is further underscored by its adoption in environmentally conscious manufacturing. The process minimizes waste, as excess sand and binders can be reprocessed and reused in subsequent casts. The ecological benefits, combined with the reduced energy consumption compared to alternative casting processes, position green sand casting as a sustainable option for aluminum production.
Despite its benefits,
mastering green sand casting requires expertise and experience. The correct proportion of sand, clay, and water is crucial to forming a mold that holds its shape under the pressure of molten aluminum. Moreover, expert knowledge is necessary to predict and manage potential defects such as porosity or shrinkage, ensuring the highest quality standards in the final product.
In conclusion, green sand casting aluminum represents a harmonious blend of tradition and innovation, offering a cost-effective, sustainable, and precise method for producing aluminum components. By understanding and optimizing this process, manufacturers can achieve superior results, meeting both technical specifications and environmental goals. As the industry evolves, green sand casting will undoubtedly continue to play a vital role, reinforcing its status as a cornerstone of modern manufacturing practices.