Green sand aluminum casting is a prominent method in the field of metalwork, revered for its versatility and cost-effectiveness. This manufacturing process plays a crucial role in creating intricate and durable aluminum components, catering to a wide array of industries. With decades of experience in engineering and metallurgy, I can affirm the profound impact this technique has had in advancing industrial capabilities.
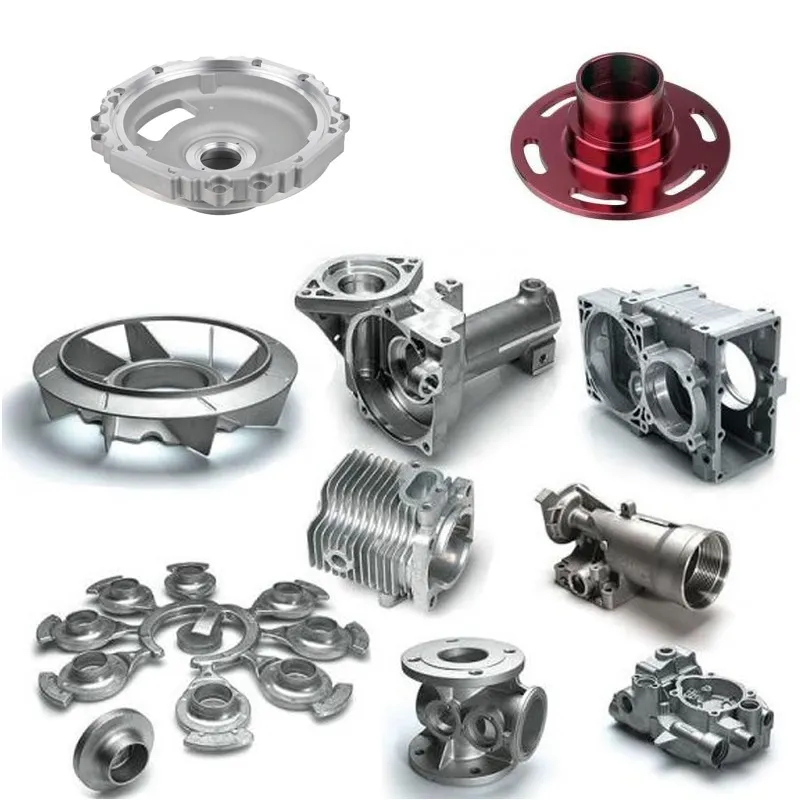
At the heart of green sand aluminum casting is the use of a sand-based mold, which is both a practical and economically viable solution for producers. The green in green sand does not refer to color but to the fact that the sand is wet, emphasizing the presence of water or other additives that bind the sand particles together. This blend typically consists of high-quality silica sand, clay, and water, achieving a perfect balance that can withstand the heat of molten aluminum.
One of the standout benefits of green sand casting is its capacity to produce complex geometries with ease. For companies looking to bring a new aluminum product to market, this method offers the flexibility needed to create detailed features and intricate designs without the hefty price tag associated with alternative methods. This is particularly advantageous in specialty industries such as aerospace and automotive, where precision and intricacy cannot be compromised.
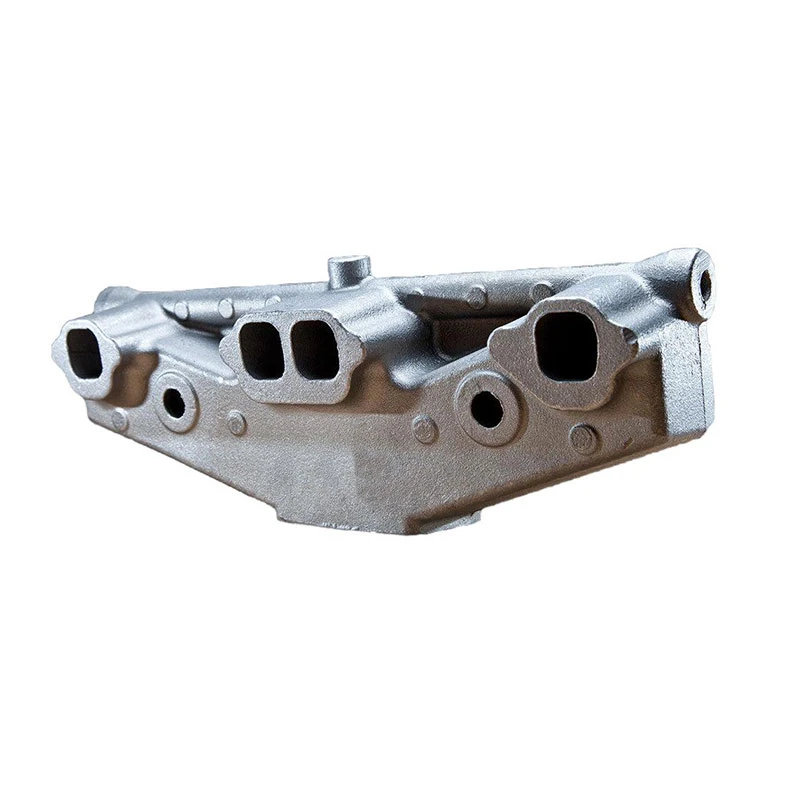
From a technical standpoint, expertise in green sand casting requires a deep understanding of the characteristics of both the sand mixture and the aluminum alloy used. My years in the field have taught me that the quality of the end product is heavily dependent on carefully balancing these two factors. For instance, selecting the right aluminum alloy is crucial, as each blend offers different strengths, conductivities, and thermal properties which can significantly affect the performance of the cast part.
The manufacturing process begins with preparing the green sand mold. Professionals meticulously shape this mold in accordance with the design specifications, ensuring all details are captured with precision. The mold must be packed carefully to prevent imperfections such as air pockets, which can lead to defects in the final product. Once the mold is ready, it is time to pour the molten aluminum.
green sand aluminum casting
Pouring aluminum is an art in itself, requiring a blend of skill and timing. The metal must be kept at a precise temperature to ensure it flows smoothly and fills every nook of the mold without causing damage or distortion. After the aluminum has solidified and cooled, the mold is carefully broken apart to reveal the cast component. This is a critical step, as any mishandling can affect the integrity of the final product. Post-casting treatments, such as trimming, polishing, and inspections, further ensure that the final component meets industry standards and client specifications.
Authoritativeness in green sand aluminum casting is achieved by adhering to stringent quality control standards and leveraging state-of-the-art technology. Advanced simulation software enables foundries to model and predict casting outcomes before the physical process begins, significantly reducing the risk of errors and material waste. This not only enhances efficiency but also builds trust with clients, who can be assured of receiving a product that meets their exact requirements.
Trustworthiness in this domain is fostered through transparency and consistent performance. Clients value suppliers that maintain open communication and provide complete documentation of the casting process and material properties. Certifications and compliance with international standards further bolster a company's reputation, underscoring their commitment to excellence and reliability.
In conclusion, green sand aluminum casting remains an invaluable process in modern manufacturing. Through a combination of skill, technical knowledge, and advanced tools, producers can deliver high-quality aluminum components that meet the demanding needs of contemporary industries. As the market evolves and expectations rise, the expertise and authority of experienced professionals will continue to drive the industry forward, ensuring this age-old technique retains its relevance and continues to innovate.