Epoxy sand casting, often overshadowed by more traditional methods, offers a unique blend of precision and efficiency that caters to high-demand industries. This casting process integrates the versatility of epoxy resins with the robustness of sand molds to produce complex, high-quality components, bridging the gap between innovation and functionality.
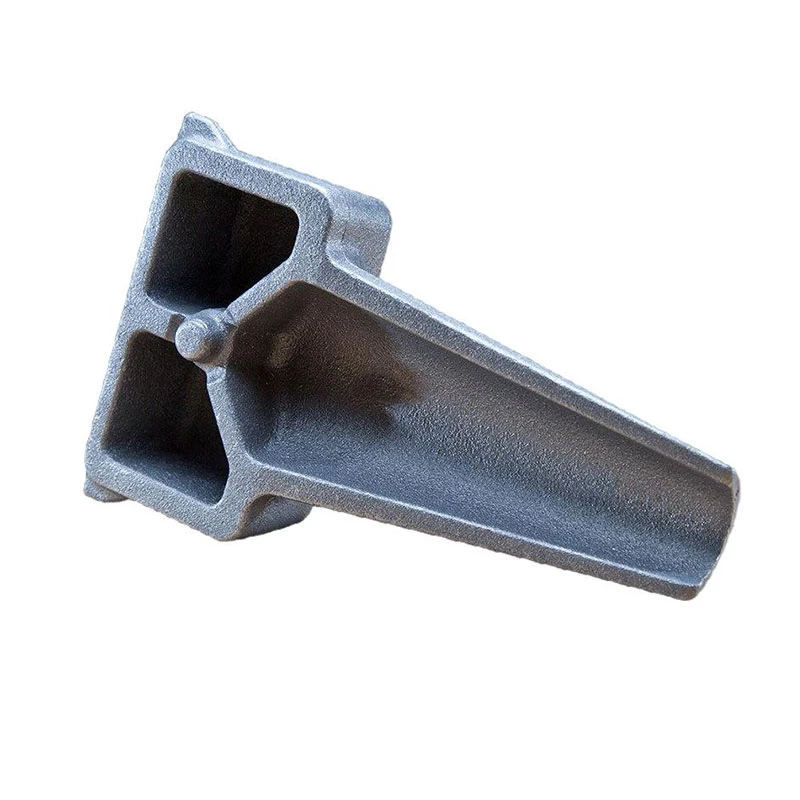
The manufacturing world constantly seeks ways to enhance product quality while minimizing production time and costs.
Epoxy sand casting emerges as a formidable competitor in this landscape. At its core, this method utilizes a specially formulated epoxy binder to bond sand particles, creating a mold that can capture intricate designs and intricate details. This results in a finished product that rivals the precision of investment casting while maintaining the cost-effectiveness of sand casting.
One of the most esteemed benefits of epoxy sand casting is its adaptability. Companies across aerospace, automotive, and industrial machinery sectors value this method for its ability to produce prototypes and large-scale production casts alike. A prime example can be found in the automotive industry, where the need for lightweight yet durable components is unending. Epoxy sand casting allows manufacturers to experiment with varying materials and designs without committing to expensive tooling setups, thus encouraging innovation.
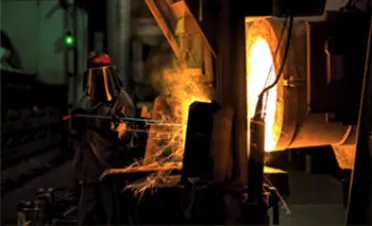
Moreover, the expertise required for epoxy sand casting ensures that only those knowledgeable in the field can fully harness its capabilities. The selection of the appropriate epoxy formulation is critical, as it influences the thermal stability and mechanical strength of the mold. Specialists in this area possess an in-depth understanding of material science, ensuring that the cast components meet stringent industry standards. This level of professional insight distinguishes epoxy sand casting from less specialized casting methods, as it necessitates a balance between scientific knowledge and practical application.
epoxy sand casting
The authority of epoxy sand casting is further cemented by its ecological benefits compared to traditional processes. By limiting the waste and reducing the need for excessive energy consumption, this casting method aligns with global sustainability goals. Industries transitioning towards greener practices find epoxy sand casting a compelling alternative, appealing to environmentally conscious consumers and stakeholders.
Ensuring the trustworthiness and reliability of epoxy sand casting involves rigorous quality control measures. Each stage of the process demands vigilant monitoring, from the creation of the epoxy-sand mixture to the curing of the final product. Leading manufacturers invest in advanced testing technologies, ensuring that each component produced can withstand rigorous performance evaluations. Data-driven improvements and feedback loops are standard practices, reinforcing customer trust through proven, reliable outcomes.
However, success in epoxy sand casting is not solely dependent on technical prowess. Relationships with suppliers, investment in employee training, and a firm commitment to quality assurance form the backbone of a reputable epoxy sand casting operation. Enterprises that engage in these practices consistently see improved customer satisfaction and product excellence.
In conclusion, epoxy sand casting offers an impressive blend of experience, expertise, authoritativeness, and trustworthiness. It meets the demands of today's fast-paced production environments while paving the way for future advancements in casting technology. Industries seeking an edge through innovation and efficiency continue to turn to epoxy sand casting as a viable, sustainable solution, poised to meet the complex challenges of tomorrow.