Die casting is a precision manufacturing process that can produce complex metal parts with high accuracy and exceptional surface finishes. This guide provides a comprehensive step-by-step breakdown of the die casting process, ideal for both novice engineers and seasoned manufacturing professionals.
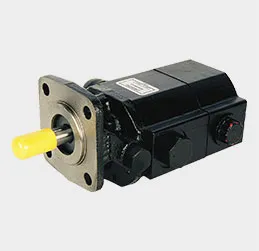
Die Casting Precision Mold Manufacturing
1. Design and Engineering The Blueprint of Precision
Creating a successful die casting product begins with meticulous design and engineering. Expert CAD designers develop detailed component models that incorporate precise tolerances and materials selection, typically choosing metals like aluminum, magnesium, or zinc. These decisions are critical for ensuring product durability and functionality. Engineers collaborate closely with designers to evaluate the tooling costs, projected production volumes, and the complexity of the part, ensuring each aspect aligns with the client's specifications.
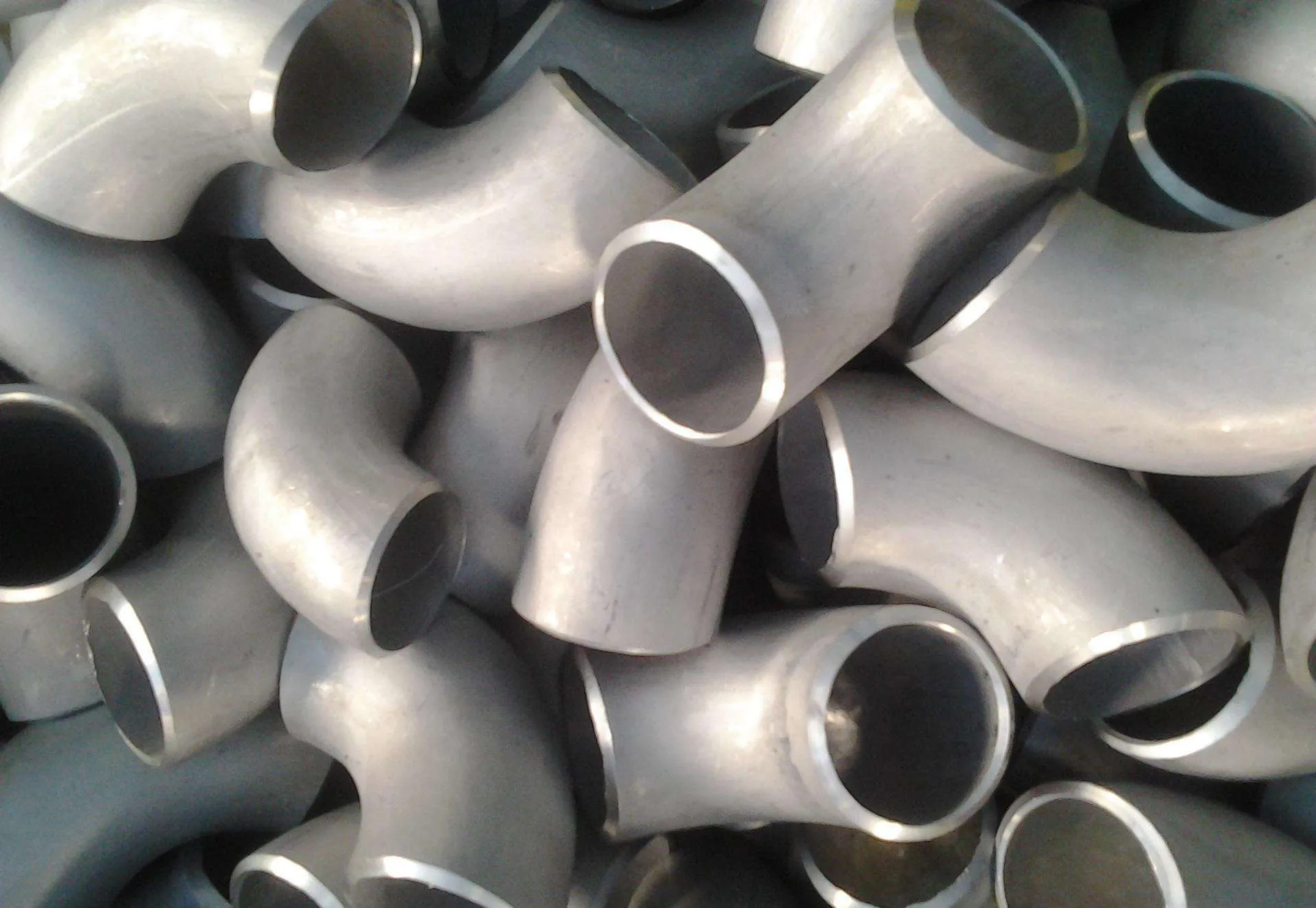
2. Mold Manufacturing Crafting the Die
Once a part's design is finalized, the tooling phase begins. The die mold is constructed using high-quality steel to withstand the rigorous demands of the die casting process. Skilled machinists use advanced CNC machining and EDM (electrical discharge machining) to achieve the intricate details required for complex geometries. Mold design incorporates considerations such as draft angles, fillets, and ribs to ensure the part can be ejected without damaging the mold or the casting.
3. Melting and Injection Under Pressure
The selected metal alloy is melted in a furnace until it reaches the specified temperature. This liquid metal is then injected into the die mold using a die casting machine, which employs hydraulic or mechanical pressure to ensure even filling. This high-speed injection helps in reducing air entrapment, minimizing porosity, and maintaining tight dimensional control. The pressure and casting parameters are expertly controlled to match the alloy’s characteristics and the mold design.
die casting step by step
4. Cooling and Solidification From Liquid to Solid
Rapid cooling and solidification follow the injection as the mold's cooling system efficiently dissipates heat. This stage is crucial because controlled solidification directly affects the casting’s structural integrity and dimensional accuracy. The expertise in metallurgy plays a significant role here, as adjustments to the cooling process might be necessary to refine grain structure and mechanical properties, depending on the application’s requirements.
5. Ejection and Finishing The Final Touches
Once the casting has sufficiently cooled, ejection mechanisms built into the die system release the part from the mold. At this point, the casting may require additional finishing processes such as deburring, sanding, or machining to remove any excess material (flash) and achieve final specifications. The use of finishing technologies such as CNC machining, surface treatments like anodizing or powder coating, and quality inspection tools ensures the final product meets rigorous industry standards.
6. Quality Control and Testing Ensuring Excellence
Quality assurance is integral throughout the die casting process. Advanced non-destructive testing methods, such as X-ray inspection and coordinate measuring machines (CMM), are utilized to detect any internal or external defects. Each part undergoes a thorough review by quality engineers to affirm compliance with dimensional and material specifications. These professionals possess the expertise to interpret test results accurately, ensuring that the final parts are not only functional but also capable of withstanding the demands of their intended application.
Efficiency, expertise, and precision define the die casting process, making it the optimal choice for producing metal components with complex designs and demanding tolerances. The continuous improvements in technology, such as simulation software and automated systems, underscore the importance of staying at the forefront of manufacturing innovation. Understanding and mastering the die casting process can significantly influence a product’s market success, providing a competitive edge with high-quality, cost-effective solutions.