Die-cast aluminum is a versatile material widely used in various industries due to its unique combination of properties that make it ideal for manufacturing complex and durable components. Its value lies in its ability to meet the high demands of modern engineering while remaining cost-effective. Here's an in-depth look at the properties of die-cast aluminum and why it is such a crucial material in product manufacturing.
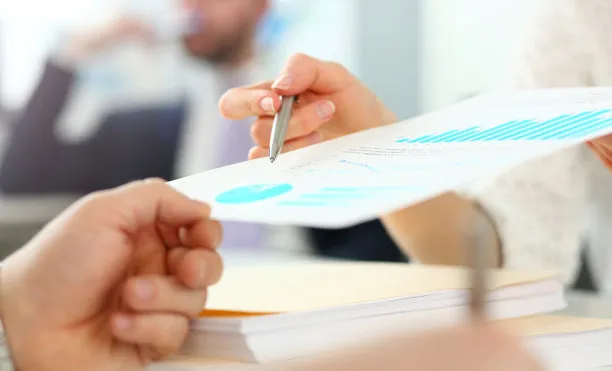
The first property that sets die-cast aluminum apart is its exceptional strength-to-weight ratio. Aluminum in its die-cast form is lightweight, yet remarkably strong, making it ideal for applications where weight reduction is critical without compromising structural integrity. This is particularly beneficial in the automotive industry, where manufacturers strive to enhance fuel efficiency by reducing vehicle weight without sacrificing safety or performance. As a result, die-cast aluminum components are extensively used in engine parts, housings, and other critical automotive assemblies.
Die-cast aluminum also offers excellent thermal conductivity. This property is crucial in industries that require efficient heat dissipation, such as electronics and lighting. Devices like heat sinks, used to manage heat in computer components or LED lighting, often rely on die-cast aluminum due to its ability to evenly distribute and dissipate heat, ensuring optimal performance and longevity of the product.
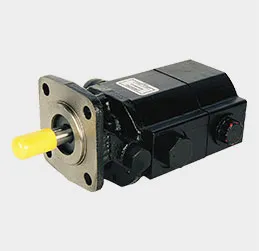
The corrosion resistance of die-cast aluminum is another significant advantage. Compared to other metals, aluminum naturally forms a protective oxide layer that shields it from oxidation and other corrosive elements. This property makes die-cast aluminum particularly suitable for outdoor and marine applications, where exposure to moisture and various environmental factors can lead to degradation in other materials. Products like marine engine components and outdoor lighting fixtures considerably benefit from this feature.
die cast aluminum properties
From a manufacturing perspective, die-cast aluminum offers unparalleled dimensional accuracy and surface finish. The die-casting process involves forcing molten aluminum into a mold under high pressure, resulting in precise and complex shapes with tight tolerances. This not only minimizes the need for additional machining but also ensures consistent production quality, thereby reducing waste and cost. Moreover, the excellent surface finish of die-cast aluminum allows for a wide range of surface treatments and finishes, enhancing the aesthetic appeal and functionality of the final product.
Furthermore, die-cast aluminum demonstrates excellent recyclability, aligning with the growing emphasis on sustainable and environmentally friendly manufacturing practices. Aluminum can be recycled multiple times without losing its intrinsic properties, reducing the reliance on raw material extraction and minimizing the overall environmental footprint. This aspect is increasingly important for companies committed to sustainability and eco-friendly product lifecycles.
Despite its many advantages, successful application of die-cast aluminum requires expertise in design and engineering. Engineers must carefully consider the material properties during the design phase to maximize performance and cost efficiency. This involves optimizing wall thickness, ensuring proper inclusion of ribs and gussets for added strength, and accounting for potential thermal expansion in high-heat applications. By leveraging expert knowledge and advanced computer-aided design tools, manufacturers can fully exploit the benefits of die-cast aluminum.
In conclusion, die-cast aluminum is a remarkable material characterized by its strength, lightweight nature, thermal and corrosion resistance, dimensional accuracy, and sustainability. These properties make it an invaluable asset in producing efficient, durable, and environmentally-conscious products across a variety of sectors, including automotive, electronics, aerospace, and consumer goods. With ongoing advancements in die-casting techniques and alloy development, the role of die-cast aluminum in shaping the future of manufacturing is set to expand even further.