In the ever-evolving world of industrial manufacturing, defense stamped parts play a critical role in ensuring the structural integrity and operational capacity of military and defense equipment. These components, often overlooked by those outside the industry, are essential to the safety and effectiveness of defense systems. As an expert in the field with years of hands-on experience, navigating the intricacies of these specialized components is second nature.
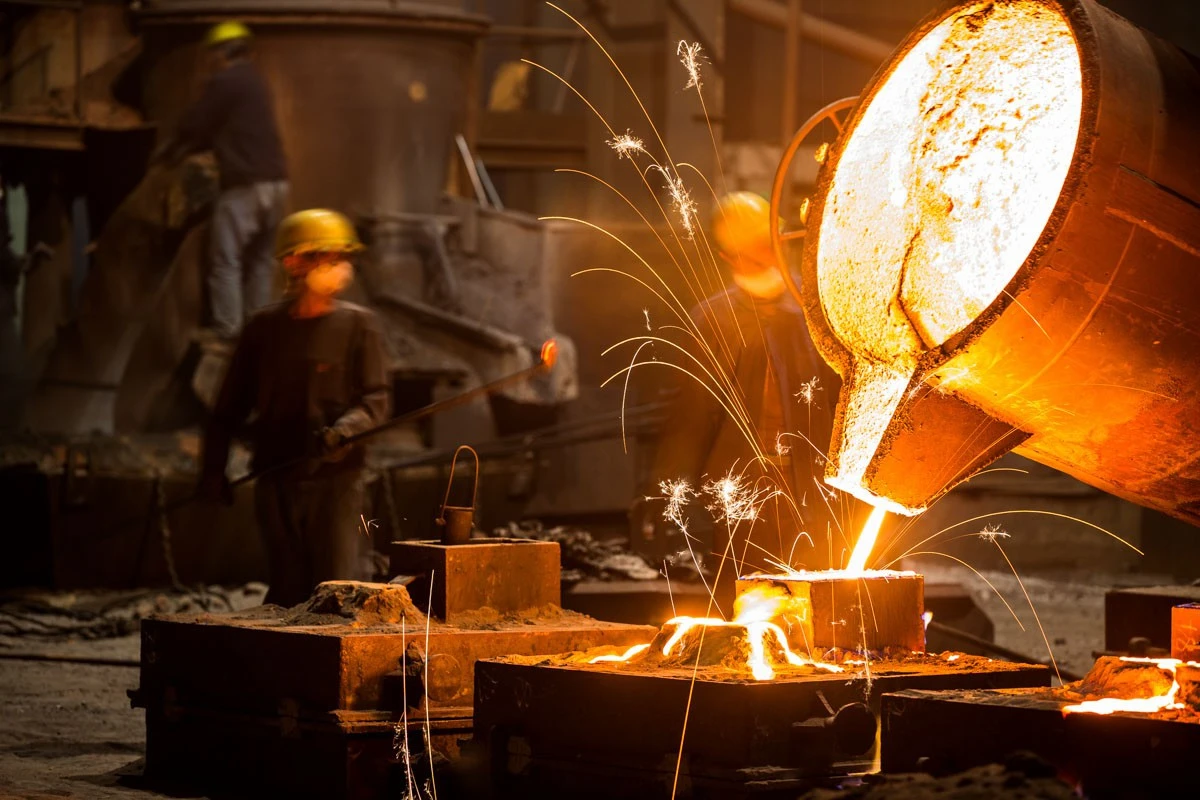
Defense stamped parts are produced through precise and rigorous metal stamping processes. This manufacturing method involves shaping metal sheets into various forms required for defense applications, utilizing a combination of cutting, bending, and piercing techniques. The result is a high-strength and reliable component that meets the demanding standards of the defense industry.
The production of these parts requires sophisticated machinery and technology. Advanced Computer Numerical Control (CNC) machines are vital in shaping and forming materials with pinpoint accuracy. This technology ensures each part adheres to strict specifications, vital for applications that leave little room for error. Multi-step stamping processes, supported by automated systems, enhance productivity while maintaining quality, an essential component of defense manufacturing.
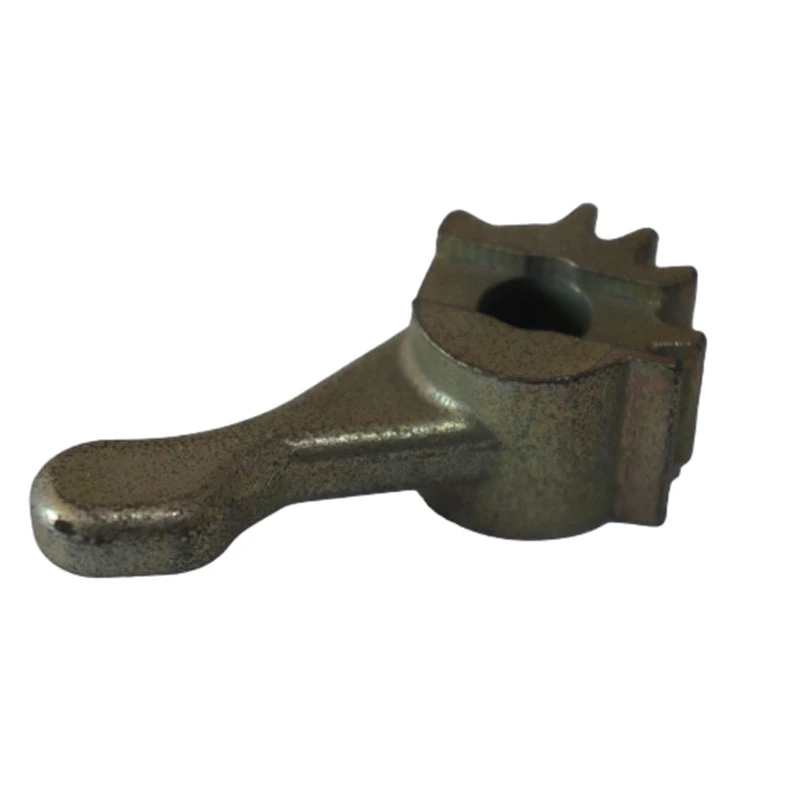
Industry experts understand the importance of selecting the right material for each application. High-strength steel and specialized metal alloys are commonly used, providing durability and resistance to demanding operational conditions. Engineers must consider factors such as tensile strength, malleability, and corrosion resistance when specifying materials, drawing on a deep well of expertise to match material properties with the application’s requirements.
Quality control is paramount in the production of defense stamped parts. Every component is subject to rigorous testing protocols, including stress testing, fatigue testing, and failure analysis, ensuring they meet or exceed military specifications. Non-destructive testing methods, such as ultrasonic and X-ray inspections, are often employed to detect internal flaws without compromising the part’s integrity.
Trustworthiness in manufacturing is established through adherence to international standards and certifications. Defense manufacturers are typically ISO 9001 certified, assuring a consistent level of quality in their operations. Additionally, compliance with the International Traffic in Arms Regulations (ITAR) and other defense-related guidelines underscores a commitment to maintaining the highest levels of industry trust and reliability.
defense stamped parts
The expertise in defense applications not only involves manufacturing prowess but also a profound understanding of defense system needs. Collaborating closely with defense contractors and government agencies, manufacturers design parts that integrate seamlessly into larger systems, whether they be for land vehicles, naval vessels, or aerospace systems. These collaborations require an authoritative grasp of defense technologies and applications.
Investment in research and development (R&D) is crucial to pushing the boundaries of what defense stamped parts can achieve. Innovative technology such as additive manufacturing (3D printing) is often integrated with traditional stamping techniques to produce complex geometries and reduce weight without sacrificing performance. Continuous improvement models and lean manufacturing principles are employed to refine processes, ensuring maximum efficiency and effectiveness.
Trust in defense stamped parts also comes from a transparent supply chain. Manufacturers build trustworthy relationships with their suppliers, ensuring that every piece of metal is traceable and meets strict quality standards. This level of accountability is instrumental in confirming that parts perform reliably in critical defense applications.
The defense sector's reliance on stamped parts cannot be overstated. These components form the backbone of many systems, from armor plating to intricate bracketry, providing the structural support necessary for mission-critical operations. It is the combination of advanced technology, strict quality assurance, and deep industry knowledge that ensures these parts perform as needed.
In conclusion, the role of defense stamped parts in ensuring the efficacy of military and defense systems is undeniable. Through a blend of experience, expertise, authoritativeness, and trustworthiness, manufacturers provide products that hold up under the most challenging conditions. This assurance allows defense forces to operate with confidence, knowing their equipment is backed by the highest standards of manufacturing excellence.