Custom aluminum casting is a critical component in many industries, but understanding the intricacies of its cost can often be daunting. With deep industry insights and first-hand experience, let's delve into the dynamics of custom aluminum casting costs.
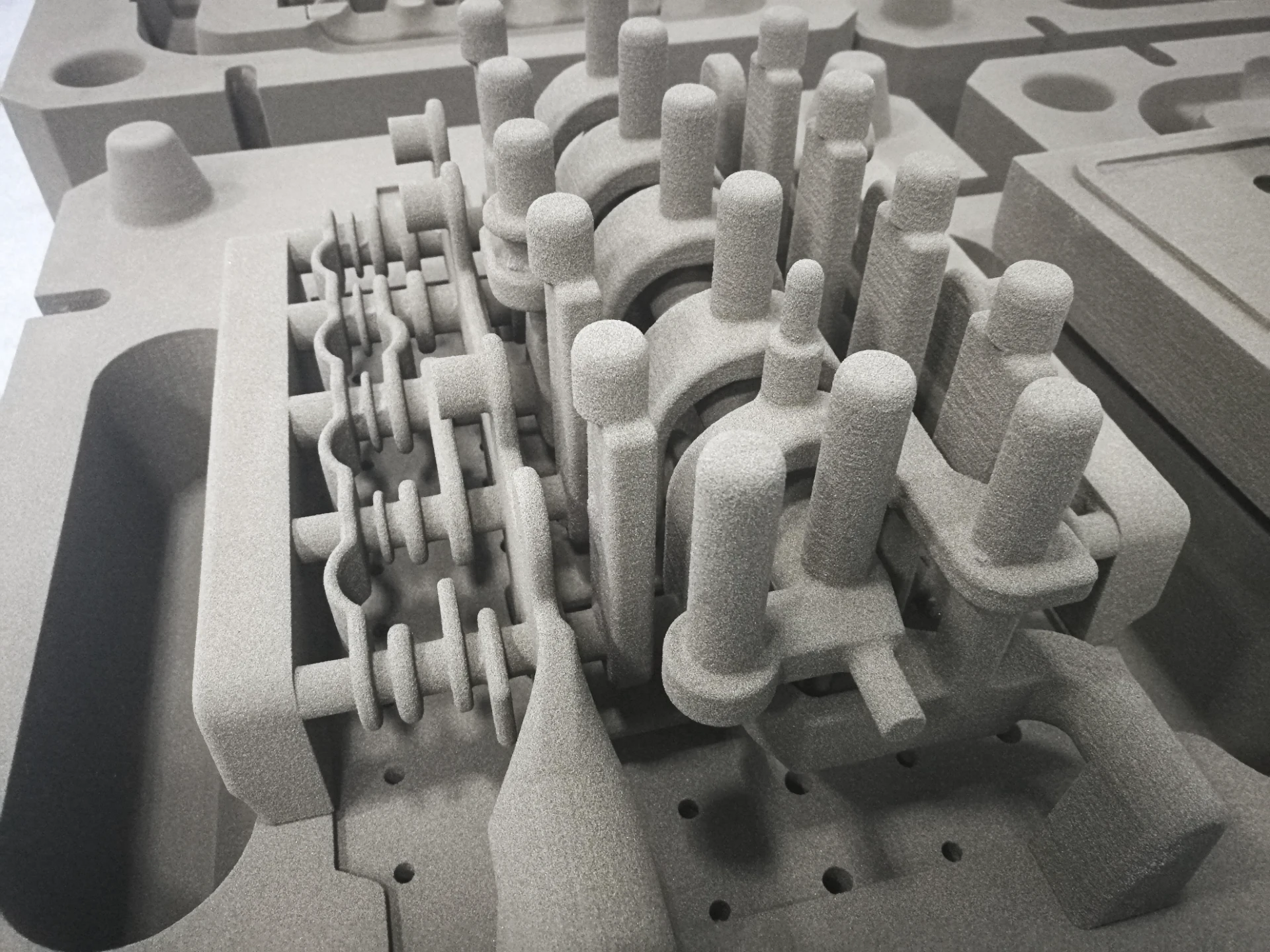
Aluminum casting involves pouring molten aluminum into a mold to form a desired shape. This process is crucial in automotive, aerospace, and consumer goods sectors due to aluminum's lightweight and corrosion-resistant properties. However, the costs associated with custom aluminum casting can vary significantly based on several pivotal factors.
First and foremost, the complexity of the design plays a crucial role. Intricately designed products require more precise molds, often made with advanced technologies such as CNC machining. The precision required in these molds ensures the final cast meets specific tolerance levels, increasing the cost. Complex designs also demand more time in mold preparation and higher expertise during the casting process, elevating expenses further.
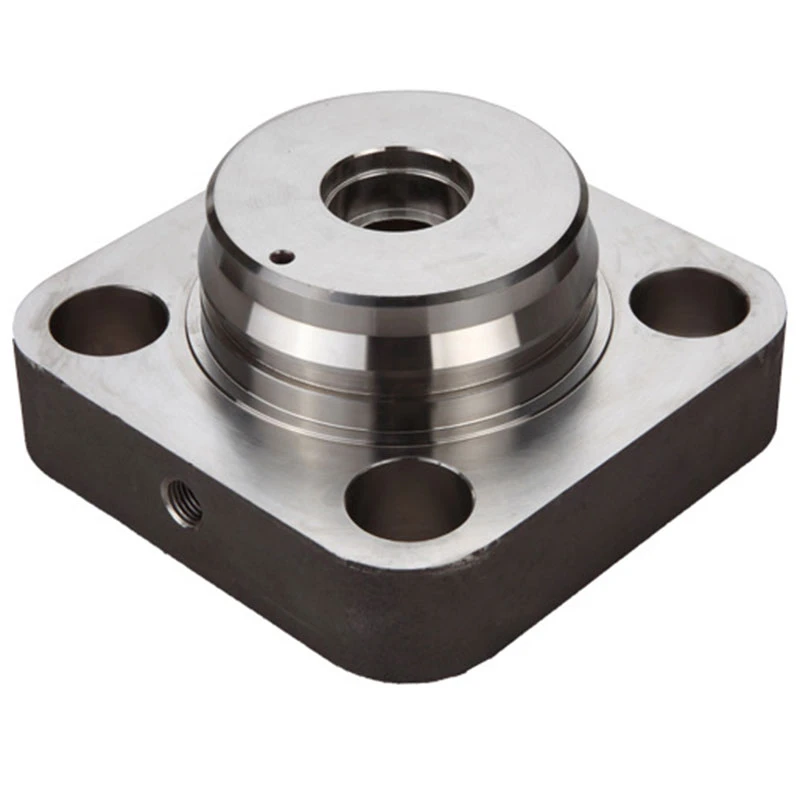
Another factor is the volume of production. In casting, economies of scale can significantly impact costs. Large production runs often lead to reduced costs per unit because the initial investment in mold creation and pattern design is spread over a greater number of items. Conversely, smaller, custom batches might bear higher costs due to the same initial investments without the benefit of scale.
Material costs are also a substantial component of the casting expense. While aluminum is generally more affordable in the realm of metals, the specific alloy required can alter the price. Alloys that offer enhanced strength or improved heat resistance might be more costly, impacting the overall financial outlay in the casting process. Consequently, selecting the right alloy to balance cost with performance requirements is a crucial step.
Labor costs contribute significantly to the overall expense in custom aluminum casting. Skilled labor is essential to ensure the quality and precision of the final product. Regions with higher labor rates will naturally reflect these in the casting costs. It’s important to consider the location of the casting facility both for cost and supply chain considerations.
custom aluminum casting cost
Additionally, post-processing costs cannot be overlooked. Most cast products require finishing processes like machining, heat treatment, or surface coating to meet industry standards and specifications. Each of these steps adds layers of cost, dependent on the level of finishing required by the end application.
In terms of financial predictability and planning, it’s essential to work with suppliers who offer transparent costing models. Detailed quotations that break down the cost elements allow businesses to understand where financial resources are allocated and identify opportunities for cost optimization. Suppliers with extensive expertise provide valuable insights into material options, process efficiencies, and design adjustments that can save costs without compromising quality.
Sustainability is another emerging consideration affecting costs. Eco-friendly practices such as using recycled aluminum or implementing energy-efficient processes can initially increase costs but may result in long-term savings through energy credits or reduced material costs. Additionally, adopting sustainable practices positions businesses favorably in markets increasingly demanding corporate responsibility.
The trustworthiness of a supplier can also influence costs. Reliable partners with proven track records minimize risks of defects and delays, which can be costly in both production and opportunity terms. Evaluating a supplier’s certifications, testimonials, and industry reputation provides insight into their reliability and commitment to quality.
In summary, the costs of custom aluminum casting encompass a spectrum of factors—from design complexity and production volume to material choices and labor costs. Through comprehensive planning, collaboration with knowledgeable suppliers, and strategic decision-making, businesses can effectively manage these costs while capitalizing on the benefits of custom aluminum casting in their product lines.