Copper sand casting has emerged as an indispensable production technique in today's manufacturing landscape, offering an impressive blend of durability, precision, and cost-effectiveness. This age-old method, which traces back thousands of years, continues to evolve, integrating cutting-edge technology with traditional practices to meet modern industrial demands.
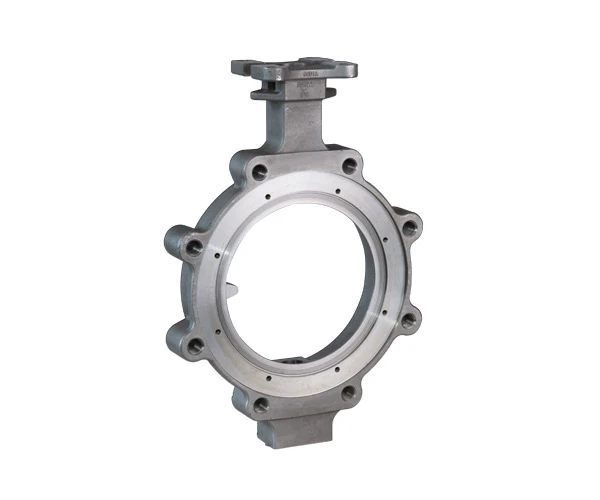
In the realm of metallurgy, copper holds a unique position due to its exceptional properties, such as high electrical conductivity, malleability, and resistance to corrosion. Sand casting capitalizes on these features, allowing for the creation of intricate and robust components used across a variety of industries, from automotive to electronics.
The sand casting process involves several critical stages, each contributing significantly to the integrity and performance of the final product. Initially, a pattern of the intended shape is created and placed into a mold made of sand mixed with a bonding agent. This mixture forms a cavity that accurately replicates the design of the pattern. The high level of expertise required in crafting these molds cannot be overstated, as even minor imperfections can lead to substantial flaws in the final product.
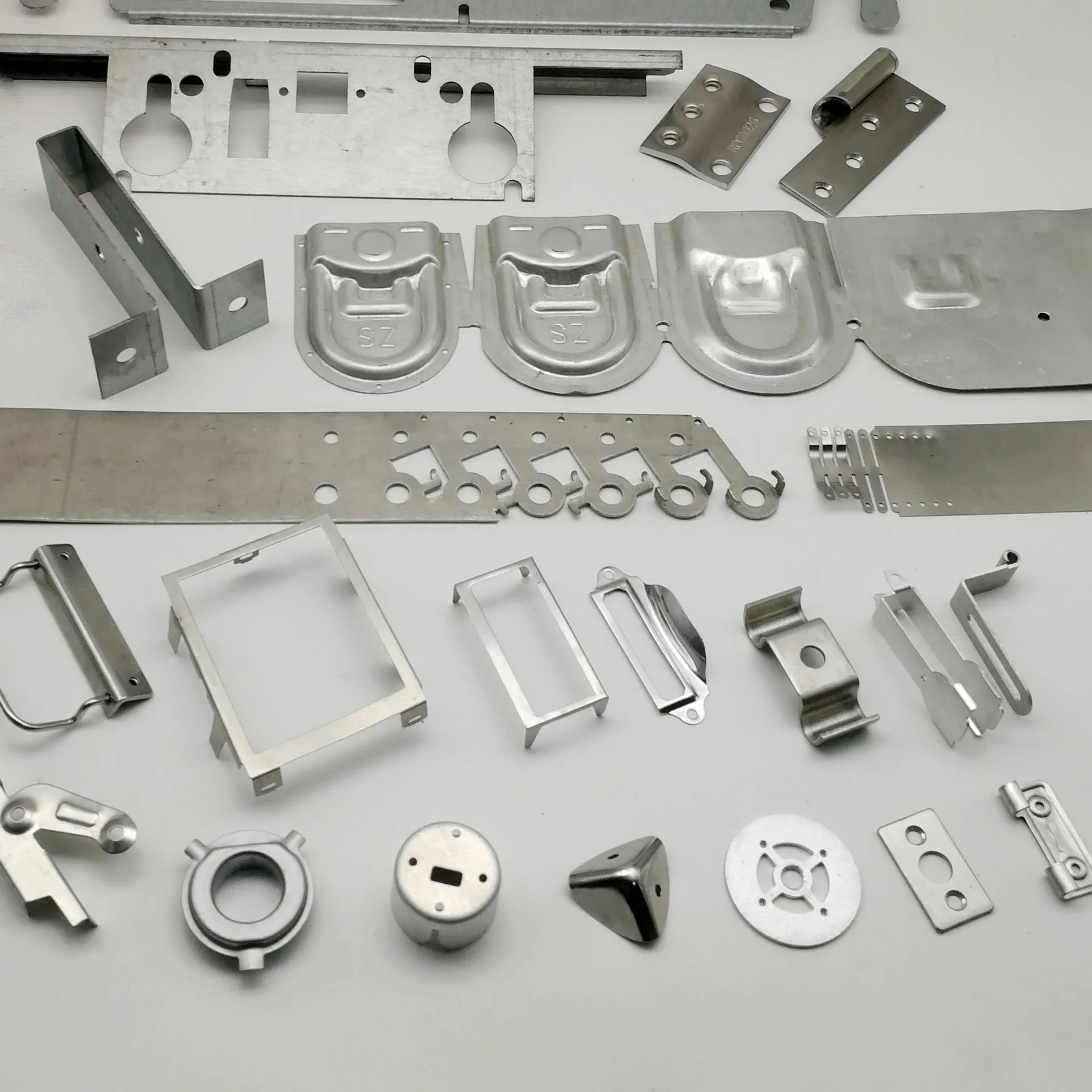
Once the mold is prepared, molten copper is poured into the cavity. The pouring process demands a high degree of precision and control to ensure uniformity in the casting. Specialized equipment and careful temperature management are imperative to prevent issues such as porosity or uneven cooling, which can compromise the structural integrity of the cast component.
As the copper cools and solidifies, it is critical for manufacturers to monitor the cooling rate closely. Rapid cooling can prevent grain growth, enhancing the mechanical properties of the copper. However, poorly controlled cooling can lead to residual stresses and warp the final structure, highlighting the importance of technical expertise and experience in managing this aspect of the process.
copper sand casting
Post-cooling, the casting undergoes various finishing processes. These may include machining, heat treatment, and surface cleaning to remove any sand residues and achieve the desired specifications. Skilled metallurgists evaluate the finished product for compliance with stringent quality standards, ensuring it meets the necessary toughness, ductility, and corrosion resistance required for its intended application.
Moreover, the sustainability aspect of copper sand casting cannot be overlooked. Sand used in casting is often recycled, contributing to a more environmentally friendly manufacturing cycle. In addition, copper's recyclability aligns with global efforts towards sustainable production, as it can be reused without any loss of quality.
The authority and trustworthiness of manufacturers specializing in copper sand casting are reinforced by their adherence to industry standards and their commitment to research and development. Continuous investment in technological advancements ensures that these manufacturers not only meet current industry needs but also pioneer innovative solutions that push the boundaries of what can be achieved with copper components.
In conclusion, copper sand casting stands as a testament to the symbiosis between traditional craftsmanship and modern technology. Its continued relevance and success are rooted in the expertise and dedication of those who drive this industry forward, ensuring that high-quality, reliable components are available to support various technological and industrial applications. As the demand for precise and durable copper products grows, the importance of this versatile and timeless casting method only magnifies, securing its place in the future of manufacturing.