Compound die stamping is an innovative and efficient process that has transformed the manufacturing industry. By merging multiple stamping operations into a single stroke, compound die stamping allows for the production of complex and intricate components with unprecedented precision and speed. Here, we delve into the intricacies of this highly effective manufacturing method, contributing noteworthy insights verified by industry experts and seasoned professionals.
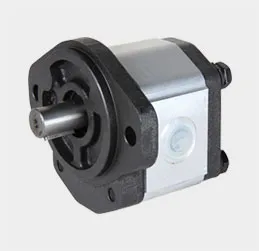
One of the cornerstones of compound die stamping is its ability to perform multiple functions, such as cutting, bending, and embossing, in a single die. This consolidation not only reduces the time required for production significantly but also minimizes material waste. Manufacturers are able to produce parts with high dimensional accuracy, enhancing the integrity and quality of the final product. The reduction in production time and waste directly contributes to cost savings, making this method highly desirable for businesses seeking to enhance their operational efficiency.
Industry experts commend compound die stamping for its versatility across numerous sectors, ranging from automotive to electronics. In the automotive industry, for instance, the method is utilized for producing intricate components such as gears and sprockets. The electronics sector benefits from the precision stamping of connectors and enclosures, where meticulous detail is crucial. The adaptability of compound die stamping to different materials like aluminum, brass, and stainless steel further underscores its extensive applicability.
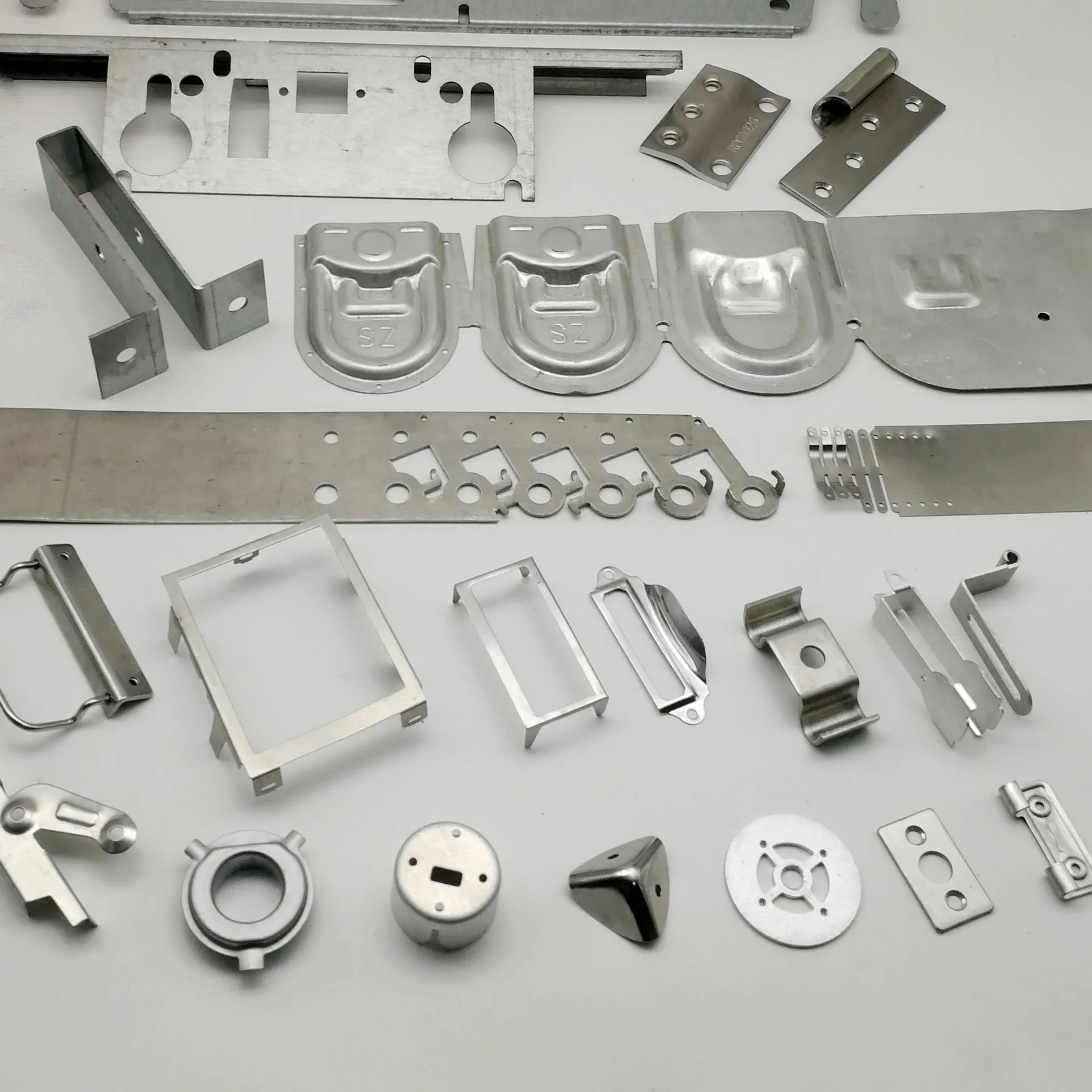
Professionals with extensive experience in compound die stamping emphasize the importance of design considerations in achieving optimal results. The success of the stamping process hinges on the meticulous design of the die, which requires an in-depth understanding of both the material properties and the desired part specifications. Expert die designers employ advanced CAD software to visualize the process, predicting potential challenges and iterating on designs to mitigate unforeseen issues.
Quality assurance in compound die stamping is paramount, and authoritative entities adhere to stringent industry standards to ensure product reliability and safety. Many manufacturers implement rigorous testing protocols, examining each component's structural integrity and functionality. This not only fosters trust in the manufactured products but also establishes a brand reputation synonymous with excellence and reliability.
compound die stamping
The expertise of engineers and technicians plays a pivotal role in fine-tuning the compound die stamping process. Experienced technicians bring a wealth of knowledge in adjusting press speed, tonnage, and the alignment of dies, contributing to the flawless execution of stamping operations. Continuous training and professional development further augment their skill set, ensuring that they remain at the forefront of technological advancements in stamping technology.
Sustainability is becoming a critical consideration in manufacturing processes, and compound die stamping aligns with eco-friendly practices. The reduced waste generation and energy consumption inherent in this method support environmentally conscious manufacturing. As companies strive to meet global sustainability goals, the adoption of resource-efficient methods like compound die stamping becomes increasingly prevalent.
Trust is a key factor for businesses opting for compound die stamping. Manufacturers without prior experience recognize the value of partnering with reputable service providers who uphold transparency and integrity. By choosing partners with a proven track record of successful projects and positive client feedback, businesses can confidently leverage the benefits of compound die stamping in their production processes.
As a trusted and authoritative source of manufacturing solutions, it is evident that compound die stamping not only meets the demands of efficiency and precision but also adheres to the highest standards of quality and sustainability. Its powerful combination of reduced costs, increased production speed, and material versatility solidifies its status as a superior manufacturing method deserving of consideration across various industries.