Cold chamber casting, a process largely pivotal to the manufacturing industry, especially in metal casting applications, operates in environments where precision and durability are non-negotiable. This method is particularly dominant in the casting of metals with high melting points such as aluminum and magnesium alloys, contributing significantly to the automotive and aerospace industries.
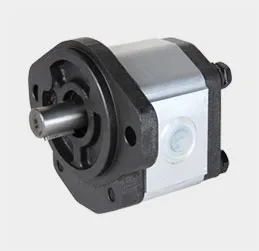
The cold chamber process distinguishes itself from other casting methodologies through its unique operational mechanics. Unlike the hot chamber process, the metal in cold chamber casting is melted in a separate furnace, then transported to the casting machine where it is injected into the mold. This procedure notably minimizes metal exposure to oxidation and other contaminants, ensuring a high-quality finish and streamlined production process.
Within industries that demand high integrity in component production, the advantages of cold chamber casting are manifold. First, due to its suitability for metals with high melting temperatures, it supports the manufacture of lightweight and robust components critical for vehicle efficiency and performance. The method’s compatibility with an array of complex shapes and thin walls makes it invaluable for design-flexible industries aiming to reduce weight while maintaining strength.
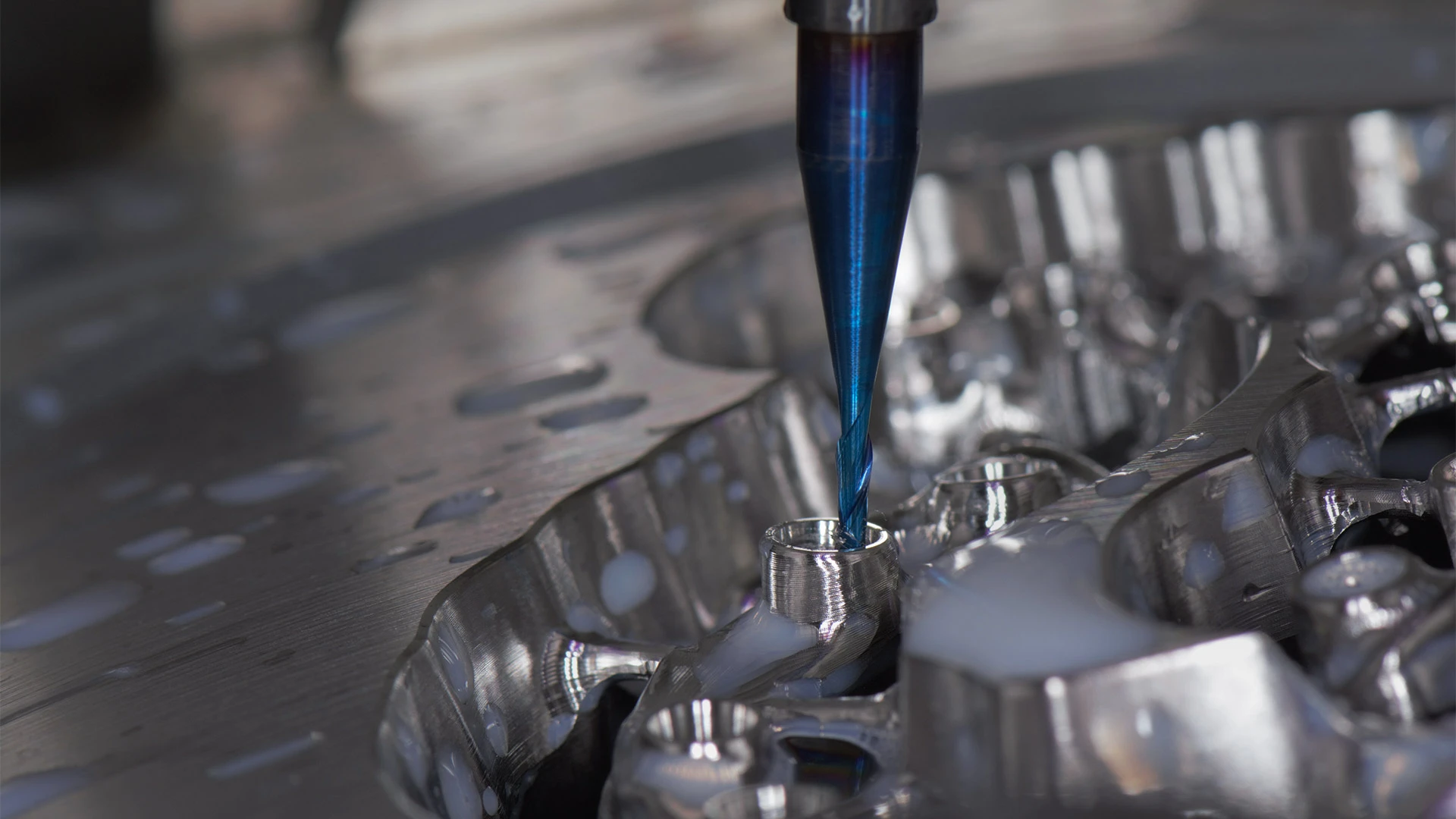
Experiences shared by industry experts underscore the reliability of cold chamber casting. Professionals emphasize the significant reduction in thermal shock to the machine parts, resulting in longer machine life and reduced maintenance costs. This reliability forms a cornerstone for production consistency, enhancing product output without compromising quality.
From a logistical standpoint, the expertise required in cold chamber casting points towards its meticulous operation. The need for precise temperature control and rapid filling of molds means operators must possess an acute understanding of the materials and machinery involved. Advanced training often ensures that they can predict and adapt to potential complications during the casting process, thus fostering a culture of problem prevention rather than resolution.
cold chamber casting
Authoritative insights into cold chamber casting emphasize the ongoing advancements in technology that continue to elevate the precision and efficiency of this method. Innovations in automation and monitoring systems are being integrated into casting machines, enabling real-time tracking of the metal flow and temperature for enhanced quality control. This technology not only facilitates higher production rates but also improves the consistency and accuracy of the final components.
Trustworthiness in cold chamber casting comes from its established presence and continuous improvement within industrial applications. Stringent quality standards such as ISO certifications often govern the production processes of industries using cold chamber methods, ensuring that components meet the necessary requirements for strength, tolerance, and performance.
For companies investing in cold chamber casting, the potential for cost-effectiveness is clear. While the initial investment for machines and training can be substantial, the long-term savings in efficiency and product consistency make it a wise choice for companies aiming to maintain a competitive edge. Furthermore, the reduction in wastage compared to other methods translates into significant material savings, contributing directly to a reduction in overall production costs.
Cold chamber casting, therefore, stands as a testament to the symbiosis between traditional practice and technological advancement. Its role in propelling industries dependent on lightweight, high-strength components is irreplaceable. For businesses considering the investment, it represents not just a method of manufacturing but a comprehensive strategy for quality enhancement and economic viability.
As global trends lean towards innovation and sustainability, the relevance of cold chamber casting can only expand, promising continued growth and adaptation to meet future challenges in engineering and production. By prioritizing research and development, companies can seamlessly integrate cold chamber casting into their production processes, ensuring they not only keep pace with contemporary demands but also set benchmarks for future industry standards.