Finding affordable yet quality materials for your projects can often be a daunting task. When it comes to metal casting, utilizing the right type of casting sand is crucial not only for producing high-quality products but also for ensuring cost-effectiveness.
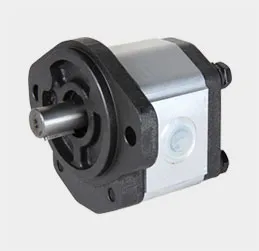
Over the years, I've accumulated vast experience working with various types of casting sand. My journey into the metalworks industry began decades ago, seeing many changes and advancements firsthand. Customers often struggle with choosing the right sand, primarily concerned with cost, without sacrificing the integrity and quality of their casts. I am here to share my deep knowledge and insight into the world of affordable casting sand options.
One of the most cost-efficient choices available is greensand. Greensand is a mixture of sand, clay, and water. Due to its rich clay content, this sand is malleable and lends itself well to complex shapes and details. From my experience, greensand is not only inexpensive but also reusable, reducing long-term costs even further. Despite its low price point, it delivers remarkable results when managed properly. To optimize its effectiveness, it’s crucial to maintain the right balance of moisture and clay content, which ensures consistency in mold creation without compromising the finish.
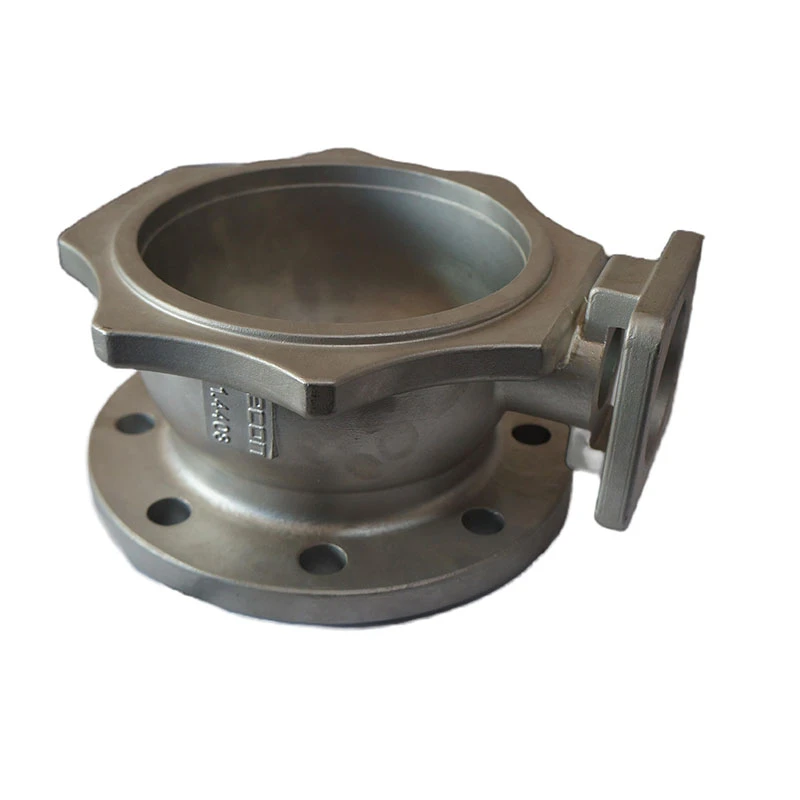
Another excellent option to consider is silica sand. Silicon dioxide-rich silica sand is abundant and therefore more cost-effective. It is predominantly used for creating cores and molds in foundries. Mastery in this craft lies in selecting the right mesh size for your specific casting requirements. Over the years, I have realized that for detailed casts, finer meshes tend to yield sharper results, whereas coarser sand is ideal for larger, less detailed projects. It’s worth mentioning that despite its low cost, precaution with silica dust exposure is paramount to maintaining a safe working environment.
cheap casting sand
Synthetic sands, though slightly more costly than natural counterparts, have emerged as reliable alternatives. These sands are engineered to possess favorable characteristics of natural sands but address some of their limitations. A proficient combination of fine grain sands mixed with binding agents, synthetic sands allow for precision casting, reducing the need for extensive post-cast machining which can ramp up costs. Having consulted numerous foundries, most agree the initial investment in synthetic sand often proves economical in the long run due to reduced waste and enhanced productivity.
Real-world feedback and expert testimonies further validate that engaging with suppliers who understand casting needs and can tailor their products offer significant benefits. Their insight into emerging trends and innovations with casting sand pays dividends, enhancing casting performance while staying within budget.
For those seeking to optimize their casting processes cost-effectively, my advice is clear partner with knowledgeable suppliers and invest in quality sand materials that are well-suited to your projects. In addition, regular testing and quality checks are indispensable. They not only ensure that your castings are up to standard but can alert you to potential problems early, saving on both time and materials.
With a wealth of options now available, businesses can efficiently manage their casting costs without sacrificing quality. The ever-evolving landscape of casting sand continually redirects our operations towards more sustainable and economically viable methods. By staying informed, and adapting to these advancements, we secure an efficient, quality-assured pathway towards industry success in metal casting.