Centrifugal die casting has emerged as a game-changer in the field of precision manufacturing, particularly for producing intricate and high-integrity components. As industries seek more reliable methods to create components that exhibit superior structural accuracy and durability, centrifugal die casting stands out due to its distinct advantages. This method, revered by seasoned engineers and manufacturers alike, is setting new benchmarks in the production of complex geometries.
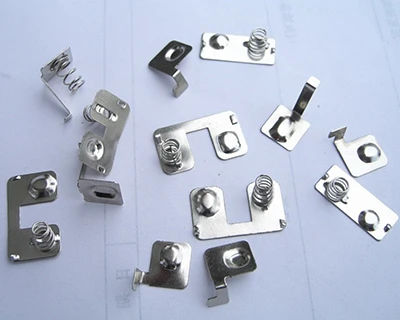
In the core of centrifugal die casting lies the principle of utilizing centrifugal force to direct molten metal into a mold cavity. Unlike traditional methods, where gravity plays a pivotal role, centrifugal die casting leverages rotational force, ensuring that the metal is uniformly distributed and free of any entrapped gases or impurities. This results in components that exhibit exceptional strength and longevity, making them ideal for applications in aerospace, automotive, and heavy machinery.
When it comes to Experience, manufacturers have reported a significant enhancement in the mechanical properties of components produced through centrifugal die casting. For instance, the elimination of porosity, a common issue with other casting methods, ensures that parts are not only stronger but also lighter, contributing to the efficiency of the product they eventually integrate with. Manufacturers often cite examples from their own production lines, where shifts to this method have halved defect rates, reduced wastage, and improved the overall quality of the end product.
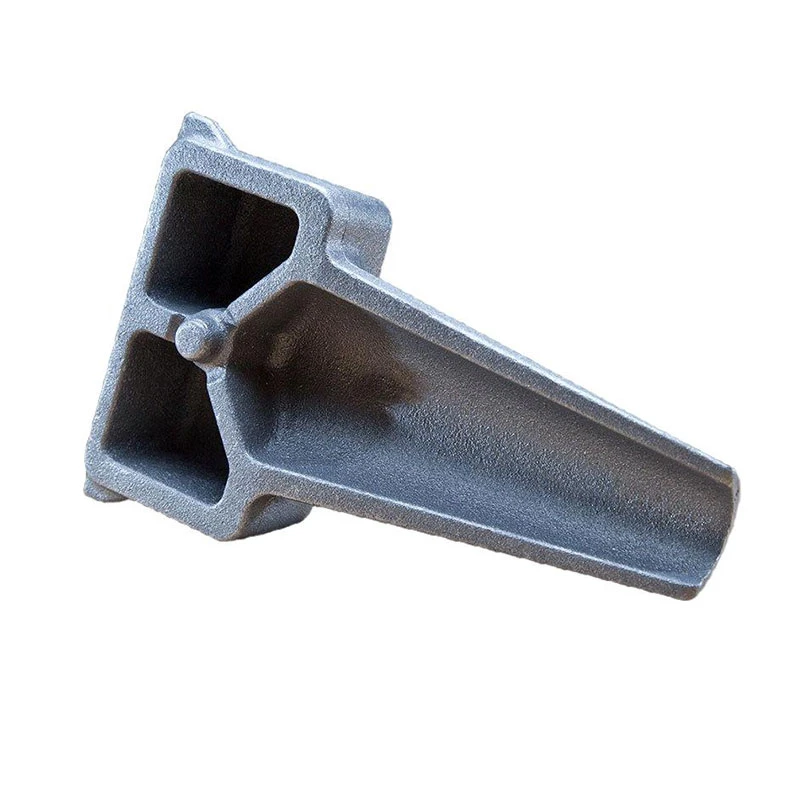
In terms of Expertise, precision and control define centrifugal die casting. Engineers and metallurgists with extensive expertise in metallurgical dynamics find this technique particularly beneficial. They highlight how the control over variables such as rotation speed, temperature, and pressure allows for fine-tuning of the process to cater to specific material and structural needs. This adaptability makes centrifugal die casting a preferred choice for bespoke manufacturing requirements, giving experts the freedom to innovate with alloys and design, ultimately confronting and overcoming industry-specific challenges.
centrifugal die casting
Authoritativeness is further established by the numerous industry endorsements and certifications that have recognized the efficacy and reliability of centrifugal die casting. Leading manufacturers and research bodies underline the technique in various case studies and white papers as groundbreaking. Compliance with international quality standards and alignment with Industry 4.0 principles also enhance its status, assuring industries of the method’s credibility and future-readiness. The collaboration between academia and industry, promoting research and development in this area, further empowers centrifugal die casting as a forward-thinking and authoritative solution.
Trustworthiness is inherent to a process that consistently delivers optimal results. Manufacturers adhering to centrifugal die casting vouch for its predictability and reduced margin for error. This trust extends beyond the production floor, reassuring customers and stakeholders of the component's performance and reliability in critical applications. Case in point some of the world’s leading automotive companies have integrated centrifugal die casting into their production lines, often vouching for improved performance in terms of fuel efficiency and emission reductions, attributed directly to the precision components manufactured via this method.
As the quest for smarter and more efficient manufacturing processes continues, centrifugal die casting represents an evolution, harnessing both tried-and-true techniques and modern technological advancements. It’s a strategy not just confined to industrial behemoths but accessible to medium and small enterprises aiming to enhance their product offerings. The approach carries an implicit promise—one of quality, durability, and performance—an assurance that becomes a brand’s hallmark in the competitive market landscape.
In conclusion, centrifugal die casting is not merely a manufacturing method; it is a testament to engineering ingenuity and a beacon of innovation in precision casting. Its impact on improving component integrity while offering economic and environmental benefits makes it an indispensable tool for industries vested in producing excellence. Through continuous refinement and adoption, it will undoubtedly shape the future of manufacturing, upholding the pillars of Experience, Expertise, Authoritativeness, and Trustworthiness.