Casting lead in sand is a captivating process that merges artistry with engineering, providing a versatile method to create intricate metal components with precision and efficiency. For enthusiasts and professionals alike, understanding the nuances of this age-old technique can enhance both the quality and efficiency of the casting project.

Beginning with the mold preparation, the process employs a unique approach where dampened sand is used to create a negative impression of the desired object. This method, known for its reliability, begins with selecting high-quality sand, typically a fine-grade silica sand mixed with a bonding agent like clay to ensure optimal mold integrity. It’s crucial to achieve the right consistency, as it directly impacts the detail and smoothness of the final product. Some experts prefer using a fluffer attachment or sifting the sand to achieve uniform texture before packing it into the mold frame, ensuring the sand’s adaptability to complex shapes.
One advantage of this method is its ability to create both small-scale decorative pieces and larger, functional components. It’s favored in many industries for producing parts like machine components, sculptures, and even specialty items like musical instruments. Before pouring, the lead must be heated to its melting point, typically around 621.5°F (327.5°C). This requires rigorous safety measures. Protective gear, including heat-resistant gloves, goggles, and aprons, are mandatory to prevent burns and inhalation of harmful fumes. The melting process is usually done using a dedicated lead melting pot equipped with temperature controls to maintain consistency and safety.
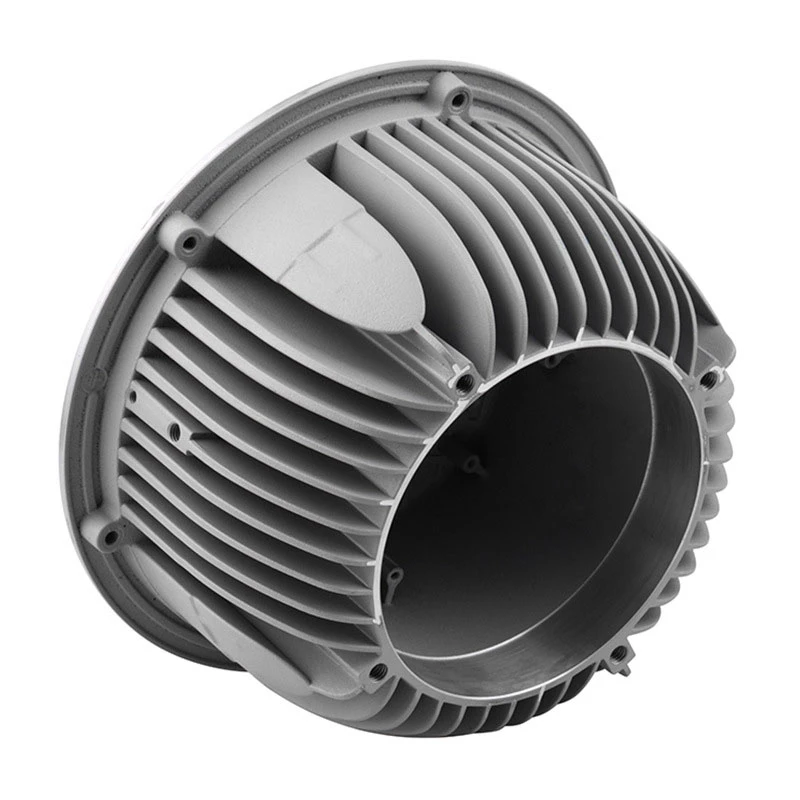
Once heated, the molten lead is carefully poured into the sand mold. This step requires a steady hand and focused precision to prevent overflow and ensure even distribution. Skilled craftsmen often employ a technique of gradual pouring to allow the molten lead to settle and fill every nook and cranny of the mold, minimizing the formation of air pockets which can affect the structural integrity of the final product. It’s this hands-on expertise that separates experienced artisans from novices, as understanding the flow and behavior of the molten metal comes with experience.
casting lead in sand
After the pour, the lead requires a cooling period to solidify fully within the sand mold. Depending on the size and complexity of the cast object, this can take from several minutes to a few hours. During this cooling phase, any slight movements can destabilize the settling lead, making a stable and vibration-free environment crucial. Moreover, some experts recommend occasionally tapping the mold gently during the cooling phase to help settle the metal and release air bubbles that might have formed during the pour.
Once the lead has solidified, the sand mold can be removed to reveal the cast piece. The extraction phase must be handled delicately to avoid damage to the fresh casting. Upon removal, the piece is typically rough and may require additional finishing processes. Cleaning off excess sand and mode lines, possibly through techniques like brushing or tumbling, is essential to bring forth the finer details. Additional steps might include filing or grinding to remove imperfections, smoothing the surface, and adding any final touches like polishing or coating, depending on the intended use of the cast lead item.
Lead casting in sand is both a science and an art. With the right balance of technical knowledge and practical skills, the process can yield high-quality, intricate designs that serve diverse industrial applications. Professionals in the field continually refine their techniques and leverage advancements in materials and tools to push the boundaries of what can be achieved through sand molding. Indeed, the combination of tradition and technology makes casting lead in sand a continually evolving discipline.
Professionals with authority and credibility in metal casting emphasize the integration of new technologies with traditional methods. Innovative approaches, such as using 3D-printed patterns or experimenting with novel sand compositions, are transforming what’s possible in lead casting. Quality control remains a priority throughout the process, underscoring the importance of expertise in guaranteeing safety, efficiency, and impeccable results in sand lead casting endeavors. These aspects of casting not only affirm the process’s adaptability but also propel the industry forward, ensuring reliability and excellence for future applications.