Casting aluminum is a transformative process fundamental to numerous industries worldwide, from automotive to aerospace, and consumer goods to electronics. This incredible metal, with its lightweight and durable characteristics, has propelled innovation and efficiency in countless applications. Understanding the intricate details of casting aluminum, along with the benefits and best practical approaches, enhances the value it delivers across diverse projects.
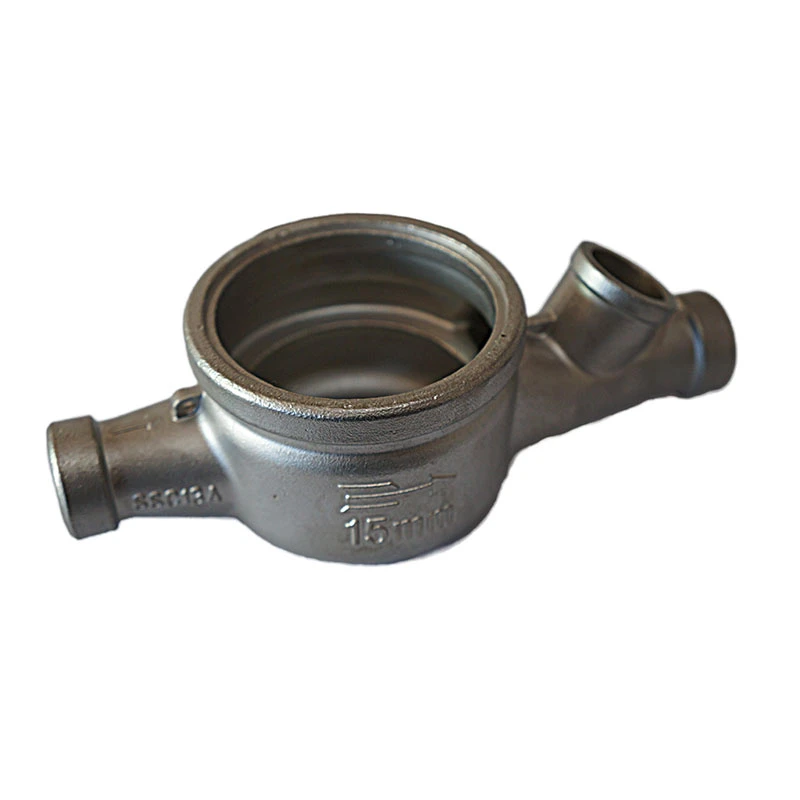
The Aluminum Casting Process An Overview
Aluminum casting begins by melting the metal and pouring it into a mold, where it solidifies into the desired shape. The flexibility in shaping complex geometries makes it ideal for creating intricate components or large-scale production items. The most common methods used include die casting, permanent mold casting, and sand casting, each offering unique advantages tailored to specific needs.
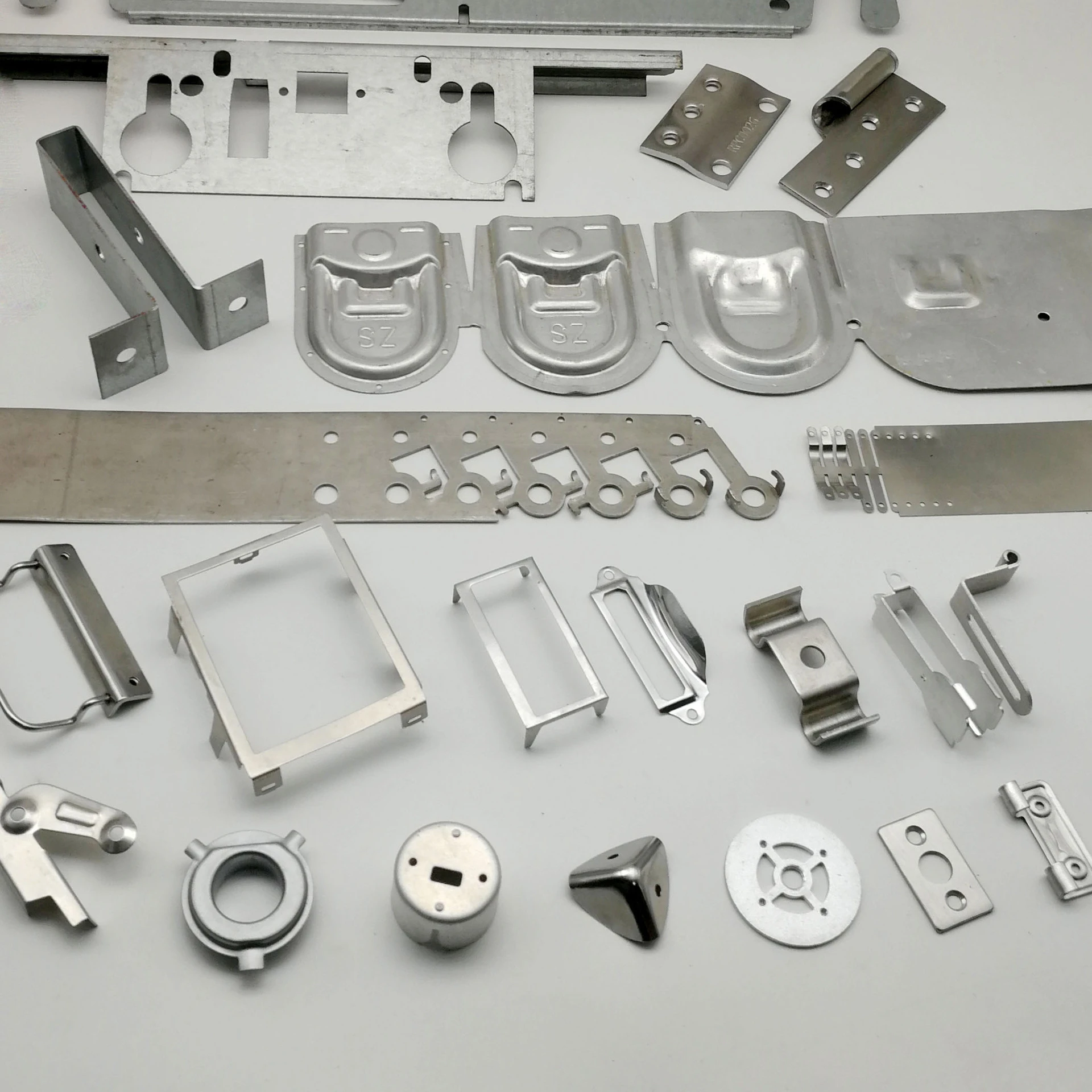
Die casting, renowned for its high-speed production capabilities, provides exceptional precision and surface finish. It involves forcing molten aluminum under high pressure into a steel mold, offering uniform results for mass production. Permanent mold casting, meanwhile, uses reusable molds made from metal, providing enhanced strength and density to the items produced. Sand casting, leveraging its affordability and simplicity, enables the creation of large or complex shapes that may be too bulky for other methods.
Advantages of Aluminum Casting in Product Development
The benefits of using aluminum in casting are manifold
1. Weight and Strength Aluminum is lightweight yet robust, making it ideal for components that require a combination of strength and reduced mass. This is particularly advantageous in automotive and aerospace sectors, where reducing weight can significantly impact performance and fuel efficiency.
2. Corrosion Resistance This metal naturally forms a protective oxide layer, making it highly resistant to corrosion. Products cast in aluminum offer longevity and reliability in various environments, from outdoor structures to marine applications.
3. Thermal and Electrical Conductivity Aluminum boasts excellent thermal and electrical conductivity, making it a preferred choice for electrical components, heat exchangers, and radiators.
4.
Recycling and Sustainability Over 75% of aluminum ever produced is still in use today. Its ability to be recycled without losing properties makes it a sustainable choice for eco-conscious industries.
Expert Guidelines for Optimal Results
casting aluminum
Achieving the best outcomes from aluminum casting requires skillful alignment with the following expert guidelines
- Selection of Alloys Different alloys provide different properties. Choose an alloy that best suits your product's requirement, balancing strength, machinability, and conductivity.
- Mold Design and Maintenance A well-designed mold minimizes material waste and ensures consistent product quality. Regular maintenance prevents defects and prolongs mold lifespan.
- Precise Temperature Control Maintaining optimal temperature throughout the casting process prevents defects like porosity and incomplete filling, ensuring impeccable surface finishes and material integrity.
Trust and Reliability in Supply Chain
Partnering with a trustworthy supplier who demonstrates expertise in aluminum casting is essential. Look for suppliers with a proven track record, robust quality control measures, and the ability to engage with cutting-edge technologies. Their commitment to sustainability and innovation should align with your business objectives.
By prioritizing reliability and transparency within the supply chain, businesses can mitigate risks associated with production delays or quality inconsistencies, ensuring the timely delivery of superior products to the market.
Future Trends in Aluminum Casting
The casting industry is evolving with innovations driving the next wave of advantages. Developments such as 3D printing for mold creation and AI-driven process optimization are setting new benchmarks for precision and efficiency. As environmental awareness grows, the industry's shift towards more sustainable practices will continue, including the reduction of energy consumption and enhancement of recycling processes.
Conclusively, casting aluminum stands as a pillar of modern manufacturing, crucial in delivering the next generation of innovative products. By integrating expert insights, sustainable practices, and advanced technology, businesses can leverage aluminum casting to achieve unparalleled success, positioning themselves at the forefront of their respective industries.