Aluminium pressure die casting components have become increasingly vital in various industries due to their remarkable properties and advantages. Leveraging the full potential of these components requires a deep understanding of the expertise and authoritative practices in the field, ensuring credibility and trustworthiness in their application.
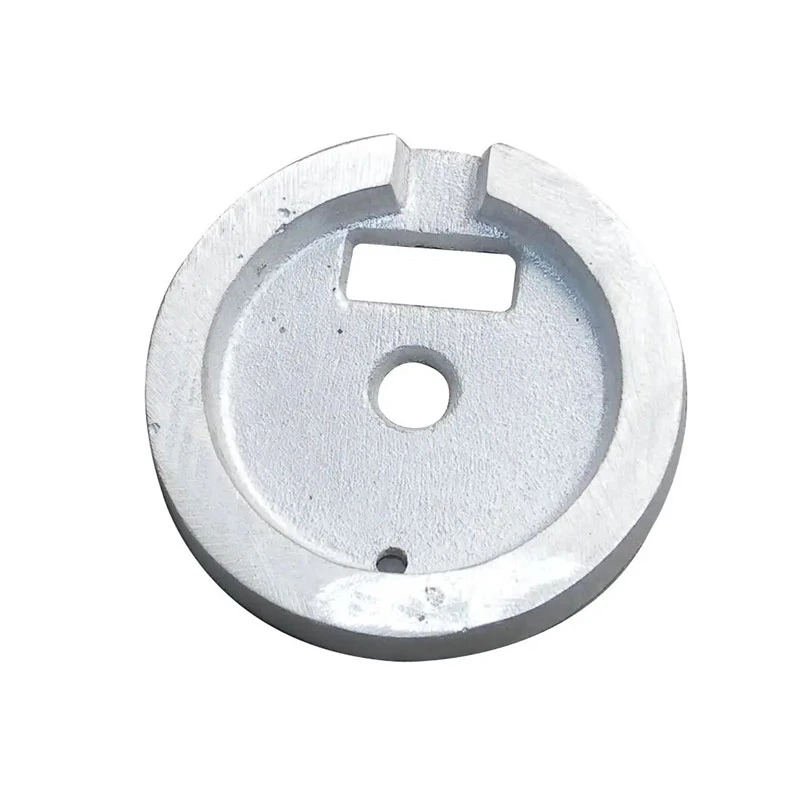
Pressure die casting is a well-established manufacturing process that produces intricate aluminium components by injecting molten metal into a mold under high pressure. This method allows for the production of highly detailed, complex components with excellent surface finish, making it ideal for industries such as automotive, aerospace, electronics, and more.
Experts in the die casting industry emphasize the importance of precision and quality control. Successful production of aluminium die casting components hinges on selecting appropriate alloy compositions. Typical alloys used in die casting, such as A360, A380, and A383, are chosen for their balance of strength, corrosion resistance, and excellent machinability. Maintaining strict control over these parameters ensures that the components meet rigorous industry standards.
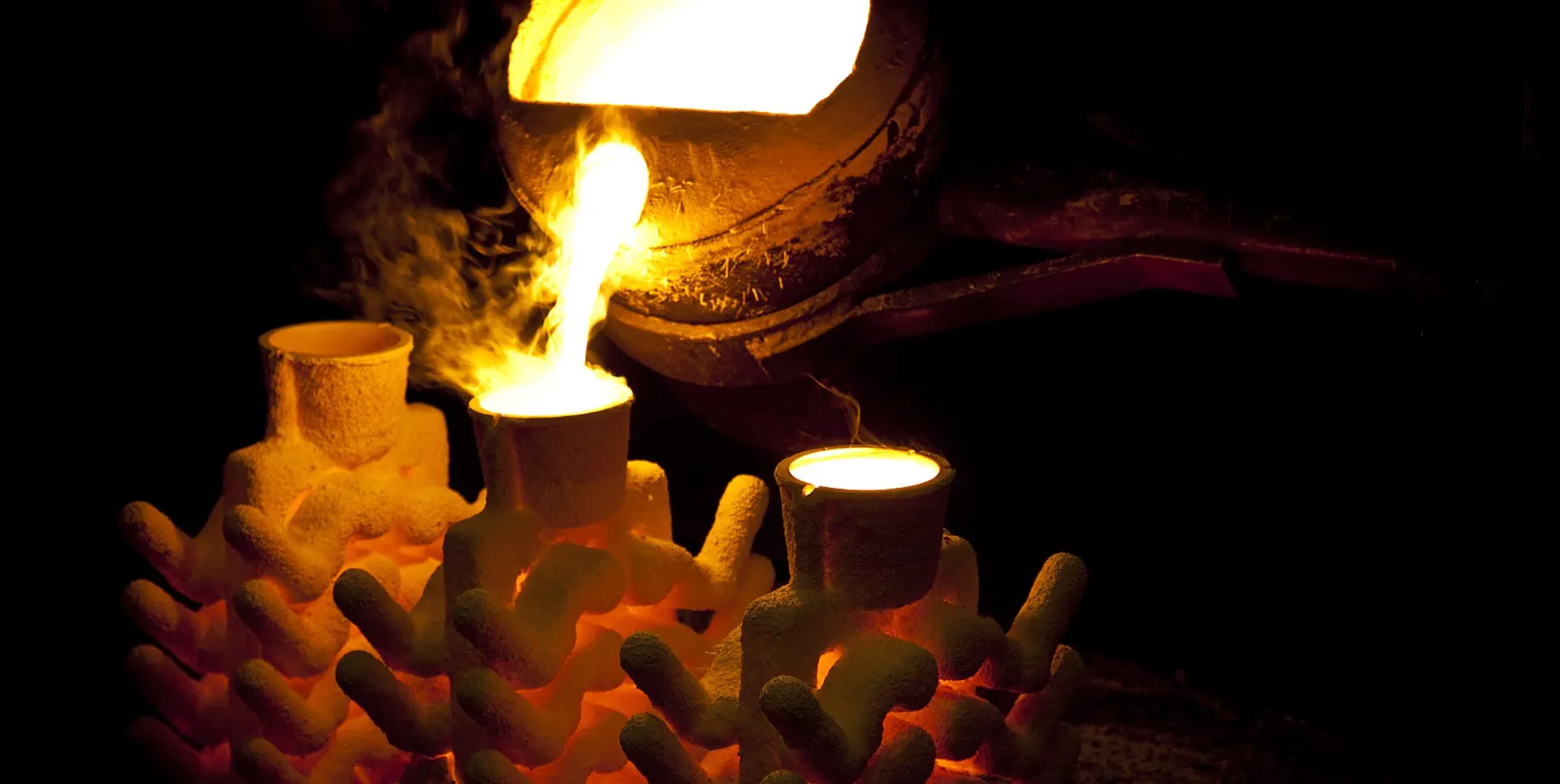
A crucial aspect of the die casting process is the design of the die itself. It requires advanced expertise to optimally design dies for efficient metal flow, minimal stress concentrations, and reduced thermal fatigue. This expertise extends to the selection of die materials, which must possess high thermal stability and wear resistance to withstand repeated casting cycles. A well-designed die not only prolongs the lifespan of the tool but also enhances the quality of the final components.
In terms of manufacturing experience, companies that excel in pressure die casting prioritize advanced technologies and continuous innovation. They invest in state-of-the-art machinery and automation systems that enhance precision and productivity, while also reducing the risk of human error. These automated systems can accurately control the injection speed, pressure, and temperature, which are critical factors in achieving consistent quality across mass-produced components.
aluminium pressure die casting components
The authoritative manufacturers also maintain rigorous testing and inspection protocols to guarantee product performance and reliability. Non-destructive testing methods, such as X-ray, ultrasonic, and dye-penetrant inspections, are utilized to detect any internal or external defects in the components. Ensuring these components meet specific industry certifications and standards, such as ISO, ASTM, or SAE, further solidifies their reputation as trustworthy partners in the industry.
Trustworthiness in the aluminium pressure die casting industry is often bolstered by a commitment to sustainable practices. This includes the use of eco-friendly alloys and the recycling of scrap materials to minimize waste. Experienced manufacturers implement energy-efficient technologies that reduce their carbon footprint, aligning with global sustainability goals.
Finally, building trust with clients also involves clear communication and collaborative planning. Companies that work closely with their clients from the design phase through to the final product delivery ensure that all specifications are met, while also offering valuable insights based on their extensive industry experience. By providing comprehensive support and transparent processes, they foster long-term relationships built on trust and reliability.
In conclusion, the production and application of aluminium pressure die casting components require a nuanced blend of expertise, experience, authority, and trust. By focusing on these pillars, companies in this sector can produce high-quality components that not only fulfill the complex demands of modern industries but also contribute positively to the global push for sustainable and efficient manufacturing practices.