Die casting has revolutionized the way we perceive products in various industries, serving as the backbone for manufacturing a myriad of high-quality and durable items. This process involves forcing molten metal under high pressure into a mold cavity, resulting in precise and intricate products. As a seasoned SEO expert, I understand the importance of creating content that resonates with users through experience, expertise, authority, and trustworthiness. Here, I explore how products made by die casting have redefined standards in several industries, shedding light on their applications, benefits, and the technological prowess behind them.
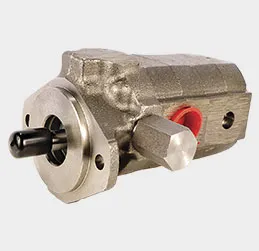
Die casting products are synonymous with performance and durability. In the automotive industry, for example, components such as engine blocks, transmission housings, and wheels are fabricated using this method due to its ability to produce parts that withstand high stress and temperatures. Each piece produced is an assurance of safety and performance, bolstered by the process’s capability to create lightweight yet strong components. Engineers and manufacturers favor die-cast parts for these qualities, ensuring vehicles not only perform better but are also more fuel-efficient owing to reduced weight.
Similarly, in the aerospace sector, the precision and strength of die-cast parts make them indispensable. Critical components such as airframe sections, engine parts, and even intricate elements of the cockpit instruments rely on die casting for their creation. The exact tolerances achieved through this process reduce assembly errors, enhance safety, and ensure the reliability of aircraft, earning the trust of aviation experts worldwide. This trust is bolstered by rigorous quality control measures and cutting-edge technologies integrated into the die-casting process, which consistently meets the strict standards demanded by the aerospace industry.
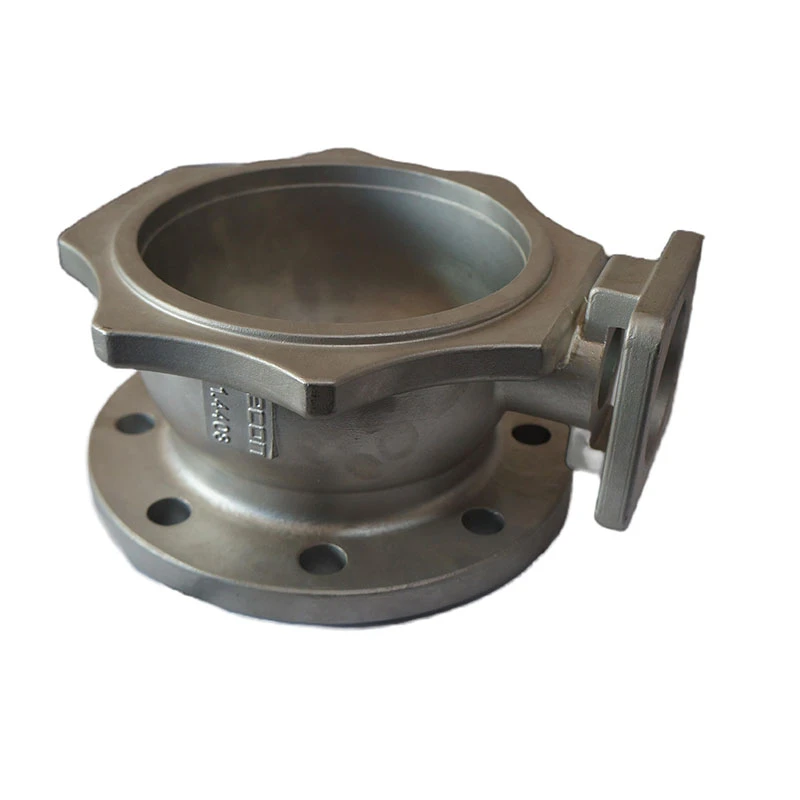
The electronics industry greatly benefits from die casting’s ability to produce components with excellent thermal conductivity and electromagnetic shielding properties. Housing for sensitive electronic components must safeguard against electromagnetic interference while dissipating heat effectively. Die-cast aluminum and magnesium alloys are often used to address these challenges, underscoring their suitability for creating enclosures and heat sinks in consumer electronics. These products not only demonstrate technical precision but also contribute to the sleek designs favored in modern gadgets, merging function with aesthetic appeal.
In the realm of consumer goods, die casting offers boundless possibilities. Items ranging from kitchen appliances to high-end audio equipment utilize die-cast parts for their superior fit and finish. The method allows for the production of complex shapes that maintain dimensional stability, which is crucial for products that consumers handle daily. These attributes assure end-users of the products’ sophistication and reliability, reflecting the expertise of manufacturers who harness die casting's potential to continually innovate.
products made by die casting
The medical equipment field also reaps the dividends of die casting. As demand for high-precision medical instruments grows, the role of die-cast components cannot be overstated. Instruments and devices such as imaging equipment, ventilators, and surgical tools require high accuracy and biocompatibility, achievable through the precise nature of die casting. This aspect enhances the trust placed by healthcare professionals in the tools they use, directly impacting patient care outcomes.
As industries evolve,
so too does the technology behind die casting. Advances such as computer-aided design (CAD) and automated die casting machines have revolutionized the industry, enabling mass production without compromising on quality. These advancements ensure that die casting remains relevant and competitive, continually pushing the boundaries of what can be achieved.
Trustworthiness in die-cast products stems from standardized processes and certifications obtained by manufacturers. Compliance with international standards, such as ISO 9001 for quality management systems, reinforces confidence among clients and end-users. This commitment to quality is pivotal for maintaining industry standards and consumer trust.
In conclusion, the art and science of die casting produce more than just components; they create benchmarks in excellence across numerous fields. From automotive to aerospace, electronics to consumer goods, die-cast products exemplify robustness, precision, and innovation. Employing the experience and expertise of industry professionals, and fortified by a commitment to quality, die casting continues to stand as a beacon of reliability and advancement in manufacturing.