Pressure die casting products are an epitome of modern manufacturing capabilities, reflecting the sophistication and precision that define today’s industrial standards. They emerge from a process renowned for its capacity to produce complex shapes with high dimensional accuracy and superior surface finishes, all while ensuring phenomenal repeatability.
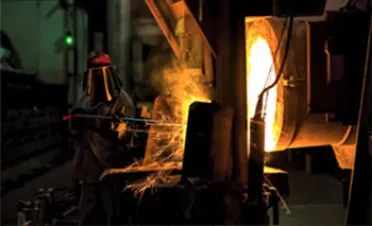
The journey of pressure die casting products begins with the selection of raw materials. When top-grade alloys like aluminum, magnesium, and zinc are utilized, the products exhibit enhanced strength, lightweight properties, and impeccable durability. The choice of alloy not only determines the mechanical properties of the cast component but also influences factors such as corrosion resistance and thermal conductivity. For instance, aluminum die castings are predominantly used in the automotive industry, fitting perfectly into applications where weight reduction is crucial for improving fuel efficiency.
A deep dive into the pressure die casting process reveals why it’s an unmatched choice for high-volume production runs. The process involves injecting molten alloy at high pressures into a steel mold or die, which is precisely machined to form the net shape of the desired product. This method allows manufacturers to create complex, intricate designs that would be nearly impossible with other manufacturing techniques. Furthermore, the inherent capability to produce vast volumes of identical castings swiftly is a testament to the process's efficiency, making it a favorite among industries requiring rapid production cycles without compromising on quality.
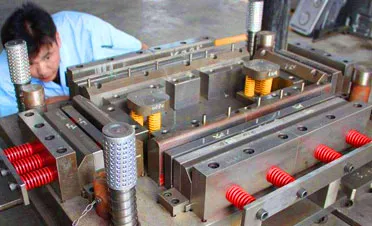
Expertise in designing die-cast parts plays a pivotal role in ensuring product performance and longevity. Skilled engineers optimize the design for manufacturability, considering factors like wall thickness uniformity, draft angles, and rib placements to minimize stress concentrations. Advanced simulation software assists in predicting potential warp zones and shrinkage, thereby enhancing the precision of the final product. This attention to detail and preemptive troubleshooting underscore the expertise required to create die-cast products that excel in both functionality and form.
pressure die casting products
The authority of pressure die casting as a manufacturing choice is reinforced by its widespread adoption across various industries. In the automotive sector, components such as engine blocks, transmission cases, and structural parts pride themselves on being die-cast, meeting rigorous performance and safety standards. The electronics industry also leverages pressure die casting to produce casings and heat sinks that not only conduct heat effectively but also provide electromagnetic shielding. Such diversity in application underscores the adaptability of pressure die casting to cater to unique industry needs while maintaining the highest quality standards.
Trustworthiness in the realm of pressure die casting products is achieved through stringent quality assurance practices. From the initial material selection to the final inspection stage, each product undergoes meticulous scrutiny. Methods such as X-ray inspection, tensile testing, and surface finish evaluation ensure that the components meet or exceed industry benchmarks. Additionally, adherence to international standards such as ISO and IATF certifications further establishes the credibility of pressure die-cast products, assuring clients of their reliability and consistent performance.
In conclusion, pressure die casting products embody the quintessence of manufacturing excellence. Their successful deployment across critical applications attests to their unparalleled precision, strength, and versatility. As industries continue to push the boundaries of innovation, the role of pressure die casting in delivering high-quality, dependable components remains indispensable, cementing its status as a cornerstone of modern production methodologies.