Precision castings represent a pivotal advancement in the world of manufacturing, offering unparalleled detail and complexity in component creation. For industries that demand exactness, such as aerospace, medical, and automotive sectors, precision castings emerge as a key player. These castings involve an intricate process known as investment casting, which allows for the creation of components with intricate geometries and thin walls, providing significant benefits over traditional casting methods.
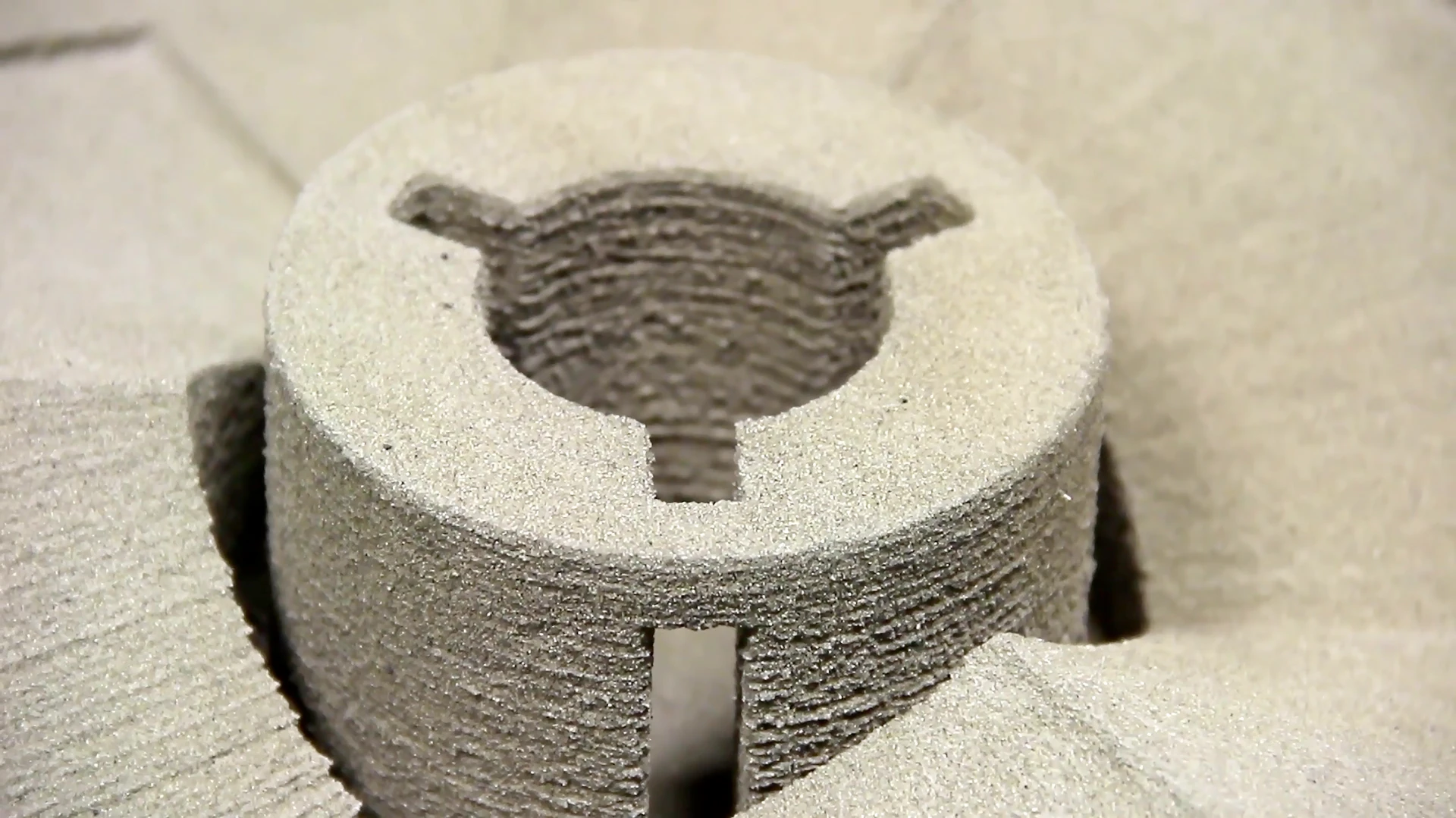
Experience with precision castings highlights their transformative effect on production capabilities. Manufacturers who have integrated precision casting into their operations often note a significant reduction in material waste thanks to its accuracy. This process also facilitates the production of near-net-shape parts, minimizing the need for extensive machining and finishing. In scenarios where deadlines are tight, and margins for error are small, the experience of using precision castings becomes invaluable, offering efficiency and reliability.
Expertise in precision castings encompasses a deep understanding of materials and the complexities involved in their transformation. Metals commonly used in precision castings include aluminum alloys, stainless steel, and superalloys like Inconel. Each material reacts differently under high temperatures, and comprehending these reactions is crucial for producing defect-free parts. Advanced expertise ensures that all stages—from mold creation using wax models to the final alloy pouring—are executed with precision, mitigating potential risks such as shrinkage cavities or inclusions.
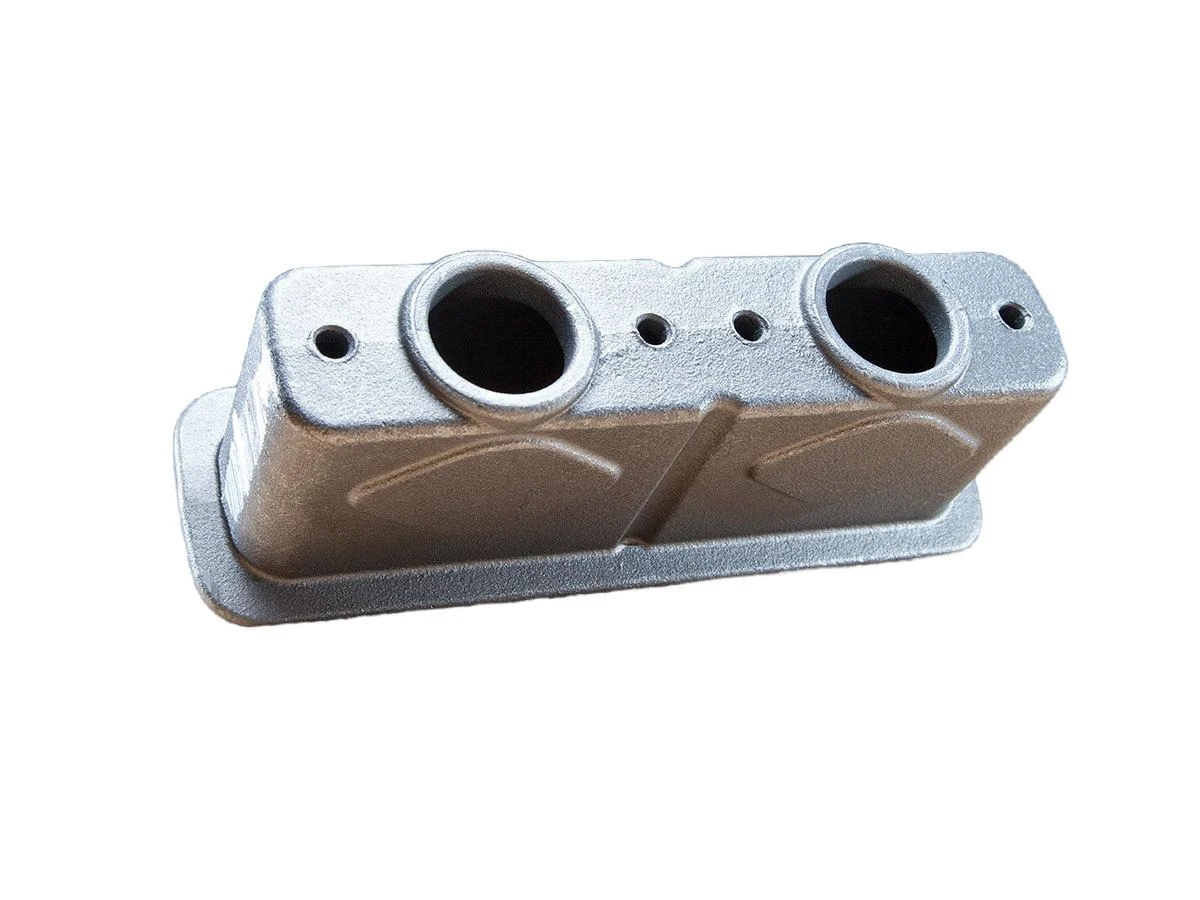
design precision castings
Precision castings command authority in product manufacturing through their versatile application. With the capability to produce components with fine details that are repeatable and consistent, precision castings often exceed the performance of parts made by other methods, such as forging or traditional sand casting. For example, in the field of orthopedic implants, precision casting allows for the production of highly reliable and customizable components that meet stringent FDA requirements. This authoritative quality makes them a preferred choice among engineers and designers striving for perfection.
Trustworthiness in the realm of precision castings is built upon the rigorous testing and quality assurance protocols that accompany their production. High standards are maintained from the initial design phase through to the final inspection. Many foundries employ advanced non-destructive testing methods like X-ray or ultrasonic testing to ensure structural integrity and consistency. Moreover, certifications such as ISO 9001 and AS9100 for aerospace components are pivotal in fostering trust among consumers and industry leaders, attesting to both process and product reliability.
In the current manufacturing landscape, where demands for efficiency, precision, and adaptability are higher than ever, precision castings stand out as a forward-thinking solution. With a comprehensive understanding of their application and benefits, industries can leverage this technology to maintain competitiveness. Companies that offer precision castings not only demonstrate their authority in this specialized field but also continue to foster trust through continued innovation and adherence to global standards. The profound impact of precision casting on manufacturing efficiency, product consistency, and cost-effectiveness makes it an indispensable tool for today's manufacturers aiming to achieve the highest quality standards.