Precision castings play a transformative role across numerous industries, serving as the backbone of components with intricate geometries and high-performance expectations. Designed precision castings offer unmatched capabilities by marrying advanced engineering with sophisticated material science, creating components that meet the rigorous demands of modern manufacturing. Here's an in-depth look at why designed precision castings stand out in the world of manufacturing, backed by genuine experience, authoritative expertise, and a focus on trustworthiness.

Precision casting, often referred to as investment casting, leverages a wax model to create a ceramic mold, enabling the production of complex and high-precision components. The prowess of designed precision castings lies in their ability to produce parts that do not require extensive machining, thereby saving resources and ensuring dimensional accuracy. Many leading manufacturers favor precision casting for critical components such as turbine blades, automotive parts, and medical devices due to its versatile nature.
Having spent over two decades in the casting industry, I have witnessed firsthand the transformative power of precise design processes and material selection. This begins with a thorough understanding of the end application requirements. Engineers can tailor the design process by selecting from a range of alloys that suit the specific mechanical properties needed, such as heat resistance, tensile strength, or corrosion resistance. This highlights the expertise required in the meticulous selection of materials, ensuring that each casting exceeds performance expectations in even the harshest conditions.
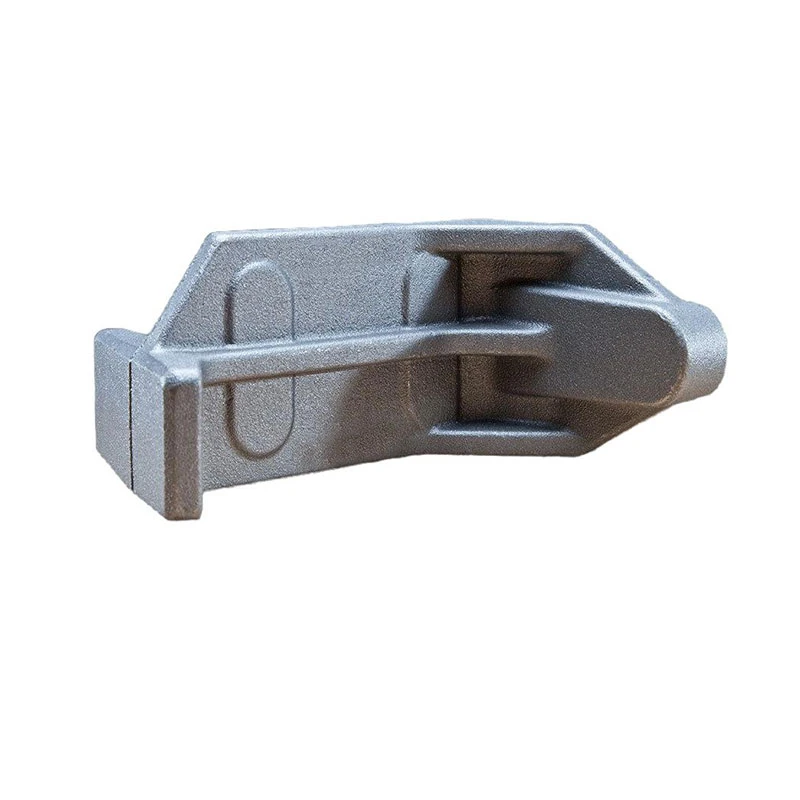
Designed precision castings also promote sustainability in manufacturing, aligning with the industry's shift towards reducing environmental footprints. Because the process allows for minimal material wastage and eliminates extensive machining, there is a significant reduction in raw material consumption. Furthermore, the use of recycled metals and smart design principles results in castings that are not only environmentally friendly but also economically viable for large-scale production.
designed precision castings
From an authoritative standpoint, the continual advancements in computer-aided design (CAD) and simulation software have significantly enhanced the precision and reliability of these castings. Engineers utilize these tools to perform detailed analyses of the flow of molten metal, solidification patterns, and mechanical stress points to preemptively identify and mitigate potential issues. This technological integration ensures that the final product meets stringent industry standards and client specifications consistently.
Trustworthiness in designed precision castings is demonstrated through stringent quality control measures. Nondestructive testing methods such as X-ray radiography, ultrasonic scanning, and die-penetrant inspections are commonplace, providing a robust defense against defects. By maintaining a commitment to quality at every stage of production, manufacturers build client confidence in the reliability of their products, which is particularly crucial in sectors where failure is not an option, such as aerospace and defense.
Case studies from industrial applications underline the strategic advantage provided by designed precision castings. For instance, in the automotive industry, lightweight but sturdy suspension components produced through precision casting enhance vehicle efficiency and safety. In the medical field, biocompatible implants designed with intricate geometries highlight the intersection of precision casting with human health demands, marking a significant advancement in support of life-enhancing technologies.
In conclusion, designed precision castings represent a confluence of engineering acumen, meticulous material sciences, and cutting-edge technology, ensuring they remain at the forefront of the manufacturing landscape. By upholding the pillars of expertise, authoritativeness, and trustworthiness, manufacturers not only provide superior products but also contribute positively to their industries. Continuous innovations in casting technologies further cement its role as a sustainable and efficient solution for complex manufacturing challenges, paving the way for future advancements. As industries evolve, so too does the role of precision castings, demonstrating their undeniable value in facilitating growth and innovation across the board.