Designing metal stamping parts introduces a dynamic intersection of creativity, engineering expertise, and material science, forming the backbone of countless industries requiring precision components. The universe of metal stamping encompasses tools and processes that transform flat metal sheets into desired shapes, employing techniques such as bending, flanging, embossing, and piercing. Mastery in this field demands an intuitive understanding of both the processes and the needs of diverse sectors, each with its distinct requirements and challenges.
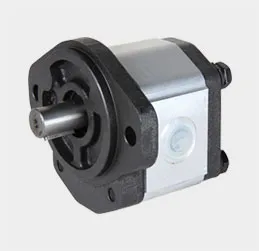
An effective design in metal stamping starts with a profound understanding of the material properties. Metals like steel, aluminum, brass, and copper each bring distinct characteristics to the table, influencing choices around ductility, tensile strength, and corrosion resistance. Using the right material is crucial for meeting the mechanical and environmental demands of the final product. Moreover, selecting the appropriate grade and gauge dictates the durability and sustainability of the stamped parts, especially when working in industries like automotive, aerospace, or electronics, where exactitude is paramount.
A critical aspect of metal stamping part design lies in the tool and die creation. This bespoke process involves crafting the stamping tool with unparalleled precision to ensure the reliable and repeatable production of components. The design of the die must account for the complexity of the shape, the thickness of the material, and the type of stamping process, be it progressive, compound, or transfer die stamping. Proficient designers employ advanced CAD software, allowing them to simulate the stamping process, identify potential stresses, and rectify any anomalies before physical production commences. These simulations help in fine-tuning the design to avoid common pitfalls such as warping, cracking, or incomplete formations.
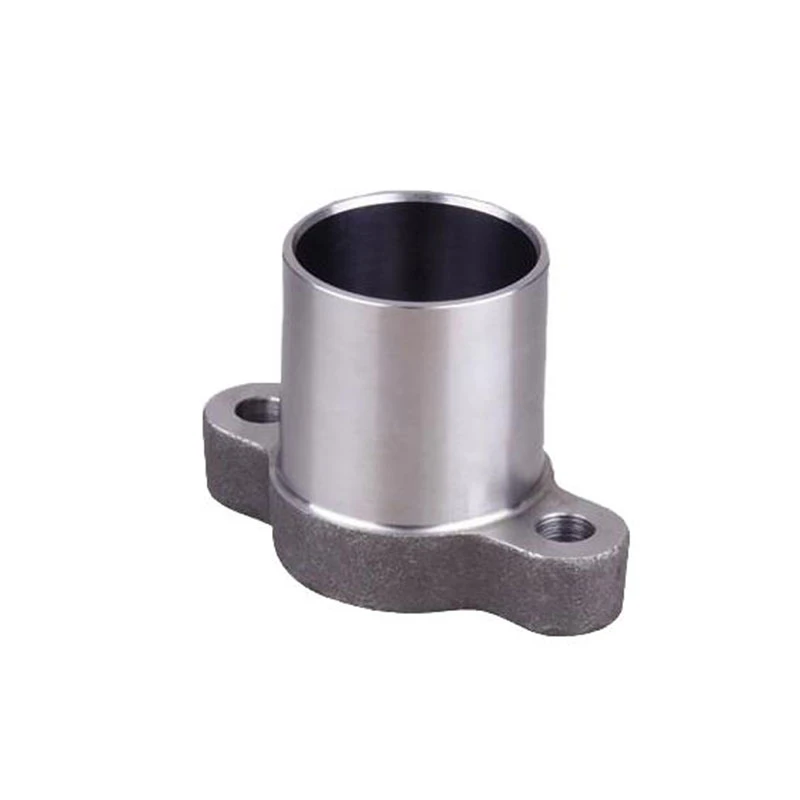
The structure of the stamped part demands careful consideration of both functional and aesthetic criteria. Designers must anticipate issues like material flow and galling, which may occur during the stamping process. One helpful strategy is incorporating ribs and gussets to reinforce areas susceptible to stress, thus enhancing the part's strength without excessive material use. Balancing the complexity of the component's geometry with the stamping method's limitations is essential to achieve the desired result without incurring unnecessary cost or production setbacks.
An often underappreciated facet of designing metal stamping parts is its scalability. Designers must consider not only the immediate production needs but the potential for scaling operations, should demand increase. This requires planning for tool longevity, ease of maintenance, and the ability to adapt dies to accommodate design revisions or different materials. Investing in modular tooling concepts can offer flexibility and reduce downtime, ensuring rapid respond to market needs without sacrificing quality.
metal stamping part design
Moreover,
the quest for innovation fuels metal stamping design. The integration of Industry 4.0 technologies, such as IoT sensors and real-time data analytics, facilitates enhanced monitoring and control over the stamping process. This technological embrace offers manufacturers unprecedented insight into operations, enabling predictive maintenance, and continuous improvement strategies that uphold production efficiency and product quality.
Sustainability, a growing concern across industries, is also reshaping the horizons of metal stamping part design. By adopting waste-minimizing techniques and utilizing recyclable materials, designers contribute to eco-friendly manufacturing processes. From the initial stages of choosing materials with lower environmental impacts to optimizing designs for efficient material usage, sustainable practices underscore the modern designer’s role in responsible manufacturing.
Finally, achieving excellence in metal stamping part design hinges on a collaborative approach across the supply chain. Designers must engage with material suppliers, tooling engineers, and quality assurance teams to synchronize efforts and achieve alignment on product specifications and expectations. This synergistic relationship is pivotal in navigating the complexities of design changes, ensuring that each step of production is technically feasible and aligned with project goals.
In conclusion, designing metal stamping parts is not merely a technical endeavor but a dance between innovation and pragmatism. It involves balancing artistic vision with engineering prowess, all the while keeping an eye on market trends and consumer expectations. Through expertise, a commitment to quality, and an embrace of advanced technologies, designers continue to evolve methodologies, delivering precision components that stand the test of time and spearheading advancements within this integral manufacturing sector.