Sheet metal stamping is a transformative process used extensively in manufacturing industries to shape and form metal sheets into intricate parts and components. The technique involves cutting, bending, and stretching metal sheets into desired geometrical shapes using a set of dies and pressing equipment. Understanding the nuances of this process can be a game-changer for businesses aiming to produce high-quality metal parts efficiently and cost-effectively.
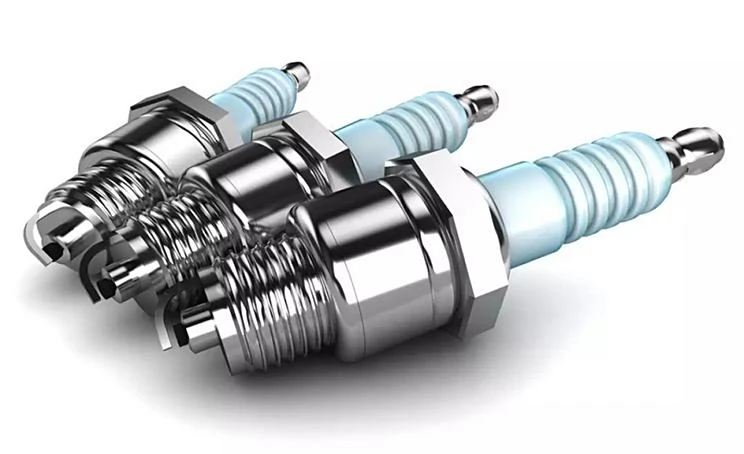
The initial step in mastering sheet metal stamping is selecting the appropriate material. Various metals such as aluminum, brass, copper, and steel each present unique properties, including malleability, strength, and conductivity that should match the intended application of the stamped parts. For instance, aluminum is lightweight and corrosion-resistant, ideal for the automotive and aerospace industries, while stainless steel offers strength and heat resistance suitable for industrial applications.
Once the material is chosen, the design and engineering phase begins. This stage lays the foundation for successful stamping by defining precise specifications and tolerances. Modern CAD (Computer-Aided Design) software is invaluable here, allowing engineers to create detailed models and simulations. These designs ensure that the stamped parts meet exact measurements, significantly reducing the risk of errors during production. Furthermore, considering factors such as springback—a phenomenon where metal attempts to revert to its original shape after bending—during this phase is crucial for achieving accurate dimensions.

Tooling is another critical component of the stamping process. High-quality dies are essential, as they directly influence the speed, precision, and quality of the final product. Investing in durable materials, such as tool steel, for die construction can enhance longevity and resist wear and tear. Precision in die manufacturing cannot be overstated—small errors can lead to defects in the stamped parts, possibly causing operational inefficiencies or failures. To combat this, manufacturers often use CNC (Computer Numerical Control) machining for tool and die making, ensuring high precision and repeatability.
The actual stamping process can involve various methods like blanking, punching, bending, embossing, and coining, each serving different purposes depending on the part's complexity and requirements. Progressive die stamping, for example, allows multiple stamping operations within a single stroke of the press, streamlining production and increasing throughput. This technique is particularly beneficial for high-volume manufacturing, where speed and cost efficiency are paramount.
how to stamp sheet metal parts
Quality control is an ongoing concern throughout the stamping process. Employing rigorous inspection protocols ensures that each part meets the required specifications and adheres to industry standards. Techniques like Statistical Process Control (SPC) can track production metrics in real-time, helping identify defects early and reduce waste. Furthermore, implementing non-destructive testing methods ensures that stamped parts maintain structural integrity without compromising material properties.
Sustainability is an increasingly vital aspect of modern manufacturing, including sheet metal stamping. Utilizing recycling programs for scrap metal not only reduces environmental impact but also lowers material costs. Additionally, optimizing the stamping process to minimize energy consumption and eliminate excessive waste channels contributes to a more sustainable operation while aligning with global environmental standards.
Innovation in sheet metal stamping technology continues to evolve, with remarkable advancements in automation and computer-integrated manufacturing. Integrating robotic systems for handling metal sheets can improve precision and reduce human error, while smart sensors and IoT devices offer real-time data analysis to optimize performance and predict maintenance needs. Such technologies enhance the reliability and efficiency of the stamping process, solidifying its position as a cornerstone in manufacturing.
For businesses looking to thrive in the competitive landscape of metal manufacturing, mastering the intricacies of sheet metal stamping is not merely advantageous but essential. By embracing advanced technologies, prioritizing quality, and committing to sustainable practices, manufacturers can ensure that they produce superior stamped metal parts that meet the demands of modern industries.