Aluminum sand castings have been a cornerstone technique in the metalworking industry for decades, valued for their versatility, durability, and cost-effectiveness. This process involves creating a mold from sand, into which molten aluminum is poured to form intricate metal parts. Understanding the nuances of aluminum sand casting can amplify advantages for businesses looking to integrate it into their manufacturing processes.
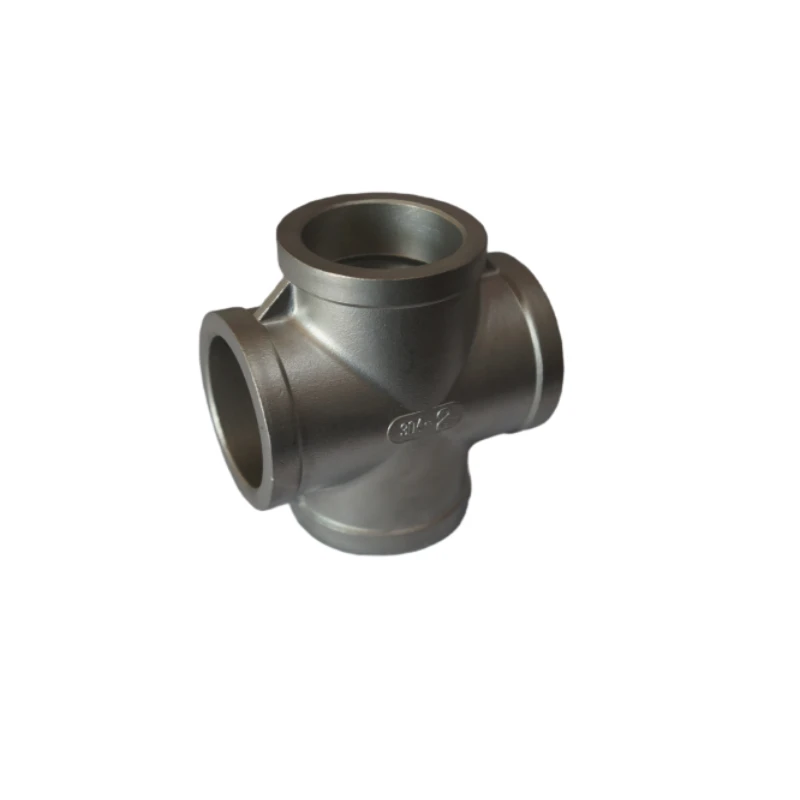
Experience plays a pivotal role in mastering the craft of aluminum sand casting. Seasoned foundries have honed their processes over the years, optimizing everything from mold creation to cooling rates. Skilled technicians understand how the quality of sand can impact the final product. They select sand with appropriate grain size and binding properties, ensuring it can withstand the high temperatures of melted aluminum without compromising the mold structure. By perfecting mold creation, experienced foundries minimize imperfections such as porosity or rough surfaces and increase the overall quality of the casting.
In the realm of Expertise, it’s important to grasp the scientific principles governing aluminum sand casting. The choice of aluminum alloy is crucial as different compositions offer varied mechanical properties and resistance to elements. For example, alloys like A356 are popular due to their excellent casting performance and substantial strength after heat treatment. Recognizing the properties of each alloy allows engineers to design parts with specific characteristics in mind, such as increased weight-to-strength ratio or enhanced corrosion resistance. Professionals in the field conduct simulations of the casting process to predict and rectify potential issues before they occur, employing advanced software to identify the ideal way to fill molds without inducing stress or deformation.
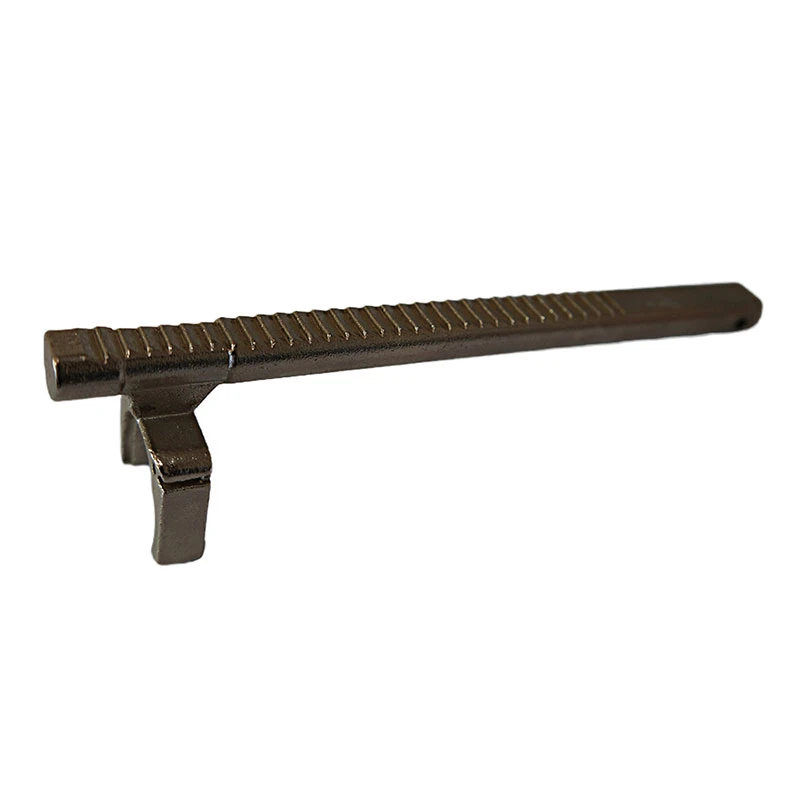
In terms of Authoritativeness, organizations that specialize in aluminum sand casting often contribute to the development of industry standards. They participate in consortia that define best practices and safety guidelines. Publishing findings in academic journals or presenting at conferences further cements their status as leaders in the field. Through continuous research and innovation, these experts push the boundaries of what is achievable with aluminum sand castings, exploring new materials, techniques, and applications.
Trustworthiness is derived from consistent quality and transparent processes. Reputable foundries provide full disclosure of their methods, showcase case studies, and offer testimonials from satisfied clients. Comprehensive quality control measures, such as non-destructive testing, are implemented to ensure each casting meets the required specifications. Certifications from industry bodies serve as benchmarks of reliability and safety, reassuring clients that they can trust in the components produced through this method.
aluminum sand castings
Aluminum sand casting is pivotal for industries ranging from automotive to aerospace, where precision and durability are paramount. This process allows for the creation of not just simple components but also complex geometries that would be challenging to achieve through other manufacturing methods. Due to its flexibility, aluminum sand casting is also a cost-effective solution, especially for low to medium production volumes or custom orders. The ability to recycle sand and scrap aluminum further enhances cost savings and aligns with sustainable manufacturing practices.
A critical aspect of leveraging aluminum sand castings is understanding its integration into larger production systems. Many manufacturers focus on lean production—an approach that aims to minimize waste without sacrificing productivity. Sand casting fits well into this model as it eliminates the need for extensive machining post-casting. Companies achieve synergy by pairing it with other processes like precision machining or surface treatments, thereby creating an efficient workflow that maximizes resource use.
As aluminum sand castings evolve, new technologies like 3D printing have begun to influence traditional practices. Hybrid techniques—combining printed models with sand casting—allow for the rapid creation of prototypes and small-batch items with intricate details. These innovations continue to push the envelope, ensuring aluminum sand casting remains a relevant and potent tool in manufacturing for years to come.
In conclusion, aluminum sand casting is more than just a method of production—it's a dynamic field where experience, expertise, authoritativeness, and trustworthiness converge to drive industrial progress. As businesses aim to stay competitive, embracing the strengths of this technique can lead to significant advancements, ensuring they meet and exceed their operational goals.