Facing sand in foundries is an integral component that significantly impacts the quality of metal castings. The selection and maintenance of facing sand is crucial for efficient foundry operation, a fact well understood by industry experts. This article aims to provide a comprehensive guide for foundry professionals looking to optimize their use of facing sand, enhancing product quality and operational efficiency.
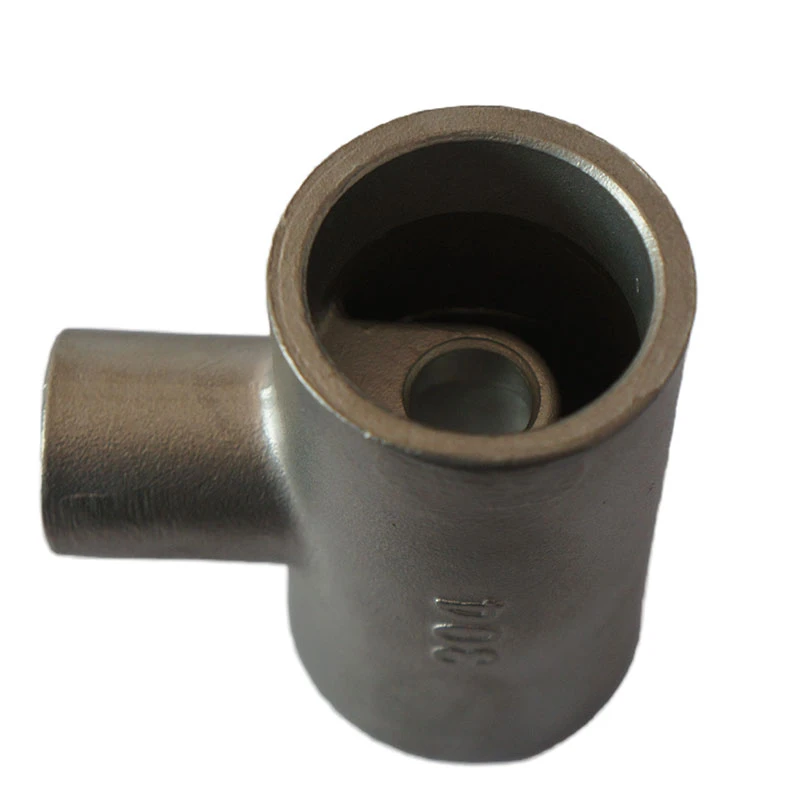
In the foundry industry, facing sand acts as the first contact point between the molding sand and the molten metal. Its primary function is to produce a smooth surface finish on the casting, minimizing defects such as metal penetration and ensuring superior quality. Expert foundrymen are aware that the quality of facing sand directly affects the final product's surface and dimensional accuracy.
To leverage the full potential of facing sand, foundry operators must pay close attention to sand composition and preparation. The typical composition of effective facing sand includes a mix of high-quality silica sand and specific additives that enhance bonding and thermal stability. The silica sand serves as the base, providing structural integrity, while the additives, such as clay binders, improve cohesion and heat resistance.
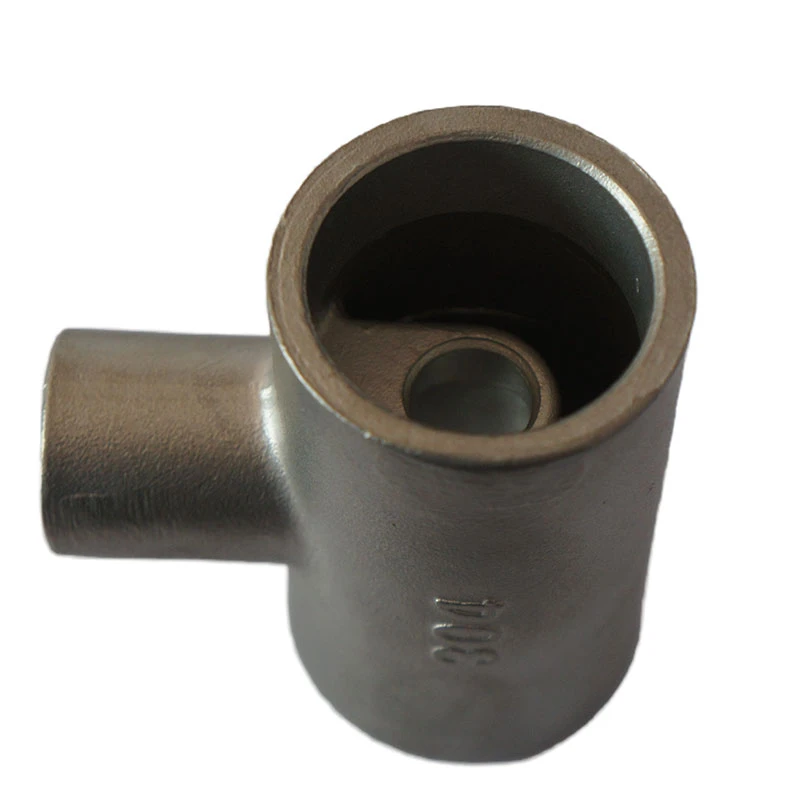
Experience has shown that the proper preparation of facing sand is as crucial as its composition. Professionals in the field implement rigorous processes to ensure sand consistency, involving controlled moisture content and precise particle sizing. Moisture control, in particular, is essential; too much moisture can lead to steam formation and casting defects, while too little can prevent proper compaction and surface smoothness. Achieving the right balance here is part science and part art, honed through years of practice and expertise.
Foundry experts also emphasize the importance of regular sand testing for properties like permeability, strength, and thermal conductivity. Conducting such tests allows for the proactive identification and correction of potential issues before they affect production. By emphasizing routine testing, foundries can maintain a steady state of high-quality output, aligning with the principles of trustworthiness and authoritativeness.
facing sand in foundry
Moreover, sophisticated preparation techniques, such as pre-mixing facing sand with specialty coatings, can further enhance the surface finish and wear resistance of metal castings. These coatings often contain refractory compounds that withstand extreme temperatures and protect the mold surface, addressing the foundry's need for durability and reliability under intense operational conditions.
In practical scenarios, foundry personnel might choose facing sands tailored to specific metals being cast. For example, the nuances required for cast iron differ from those for aluminum or bronze. Thus, the choice of facing sand should reflect the particular needs of each casting process, demonstrating the foundry's expertise in customizing solutions for specific metallurgical requirements.
Additionally, ongoing education and knowledge sharing within the foundry community contribute significantly to maintaining high standards for facing sand usage. Engaging in professional networks and workshops allows foundry workers to stay updated with technological advancements and emerging best practices. This continual learning fosters an environment of trust as stakeholders become confident in the foundry's ability to produce excellent results consistently.
Investing in premium facing sand and adherence to stringent maintenance protocols is an investment in quality assurance for foundries. By incorporating these practices, foundries not only uphold their reputation but also solidify customer satisfaction and industry standing. The effectiveness of facing sand is thus not only measured by the immediate quality of castings but also by its long-term contribution to the foundry's operational success.
Ultimately, the best approach is a holistic one where facing sand is not viewed in isolation but as part of an integrated system of materials and processes. By adopting such comprehensive strategies, foundries ensure that they are not merely keeping up with industry standards but setting new benchmarks in casting excellence.