In the realm of casting, facing sand plays a pivotal role that often gets overshadowed by the more technical aspects of mold and pattern expertise. Far from being just a supportive material in casting, facing sand is crucial in determining the final quality of a cast product. Its influence extends well beyond mere aesthetics, contributing to structural integrity and overall product performance. This article delves into the deep-seated significance of facing sand, drawing on years of authentic industry experience to offer insights into its specialized use, trusted standards, and expert methodologies.
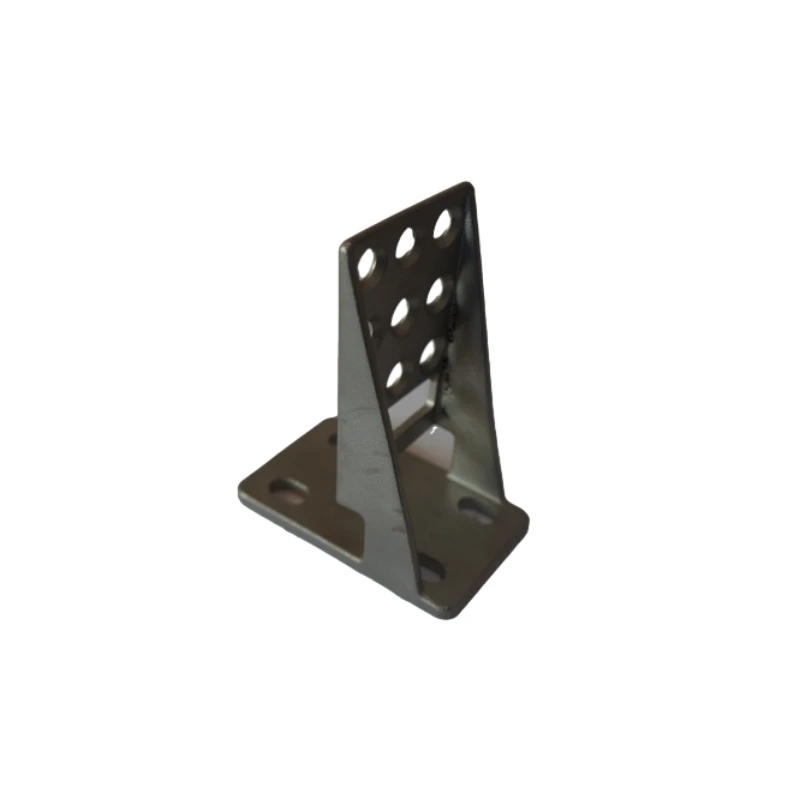
Facing sand is the fine polymer of the casting process, applied directly to the mold surface to ensure a flawless finish on the casting. This is no easy task; the selection of appropriate sand, its preparation, and application require a nuanced understanding of material properties and casting dynamics. The facing sand typically comprises high-quality silica, mixed with binders and additives tailored specifically to the casting environment's unique demands. This composition is meticulously measured to achieve optimal permeability and refractoriness—qualities essential for accommodating the rigors of molten metal.
The expertise involved in choosing the right facing sand cannot be overstated. Variations in alloy composition, mold design, and casting temperature necessitate a customizable approach. For instance, castings requiring a high degree of surface smoothness would benefit from finer sand granularity, impacting both the visual appeal and surface duration of the finished product. Expert foundry technicians meticulously assess these parameters, employing advanced lab analysis to predict sand behavior under heat and pressure, ensuring an authoritative match between facing sand properties and casting requirements.

Trustworthiness in the context of facing sand touches upon the precision in quality control measures implemented during its preparation and use. Every batch of facing sand is subjected to rigorous testing to confirm its particle size distribution, chemical purity, and bonding capacity. Techniques such as x-ray fluorescence (XRF) and thermogravimetric analysis (TGA) are commonplace in advanced foundries, fortifying trust in the sand's consistency and reliability. This ensures that each casting exhibits uniform quality, a critical assurance in industries where component failure is not an option.
facing sand in casting
To illustrate with real-world experience, consider the automotive industry, where engine block casting demands extreme precision. Here, facing sand contributes to achieving the stringent dimensional accuracies and clean surface finishes that are non-negotiable for high-performance engines. Specialists continually refine the sand formulation to adapt to evolving manufacturing technologies such as high-pressure die casting and sand casting automation, aligning traditional craftsmanship with modern innovation.
Authoritativeness is underscored by the comprehensive training and deep-rooted experience that foundry specialists bring to the table. Most are seasoned professionals with decades of hands-on involvement and academic backgrounds in material sciences and industrial engineering. Their expert judgment is trusted when calibrating the thermal properties of facing sand, drawn from an academic understanding of thermodynamics and practical insights gained from continuous sector advancements.
In conclusion, the discussion of facing sand in casting exemplifies the symbiosis of art and science in industrial production. It’s not merely about using a substance but understanding and harnessing its properties to enhance product quality. Through stringent quality measures, customized approaches, and expert oversight, facing sand emerges not just as a component of casting but as an enabler of innovation—ensuring every metallic masterpiece is realized with precision and care. This dedication to excellence cultivates a sustainable, quality-driven casting environment, epitomizing the industry's commitment to integrity and excellence.